University students using JMAG in their research will present their achievements in posters.
Come and see what they are working on and how JMAG is used in their research.
Stop by to hear the presentations and hold discussion with the students.
Order of application received
Experimental verification of ultra-high-speed magnetic gear
Nakamura Laboratory, Tohoku University
Ms. Emiri Asahina
Consideration of Magnetic Worm-geared Motor (MWGM) aiming at higher torque density
Tsutsui Laboratory, Department of Electrical and Electronic Engineering, School of Engineering, Tokyo Institute of Technology
Mr. Haruki Yamanaka
Mechanism analysis of no-load losses on the induction motor
Chiba/Kiyota Laboratory, Department of Electrical and Electronic Engineering, School of Engineering, Tokyo Institute of Technology
Mr. Keigo Matsuzaki
Faster convergence of flux in the SynRM with Concentrated winding structure of sinusoidal voltage drive
Chiba/Kiyota Laboratory, Department of electrical and Electronic Engineering, School of Engineering, Tokyo Institute of Technology
Mr. Ryo Hasegawa
Design Optimization of 12/8 Type Flux Switching Motor
Chiba/Kiyota Laboratory, Department of Electrical and Electronic Engineering, School of Engineering, Tokyo Institute of Technology
Mr. Iori Kokubo
Contribution of Magnetostriction in Motor Vibration and Acoustic Noise
Chiba/Kiyota Laboratory, Department of Electrical and Electronic Engineering, School of Engineering, Tokyo Institute of Technology
Mr. Cai Yifei
Contribution of Magnetostriction in Motor Vibration and Acoustic Noise
Chiba/Kiyota Laboratory, Department of Electrical and Electronic Engineering, School of Engineering, Tokyo Institute of Technology
Mr. Naoki Saikawa
Development of Novel Aluminum Winding PMSM with Reduced Winding AC Loss
Electrical and Electronic System Engineering, Graduate School of Advanced Science and Technology, Tokyo Denki University
Mr. Yuto Yamada
Flux Modulated Motor Using Magnetic-Geared Structure
Hirata Laboratory, Division of Materials and Manufacturing Science, Graduate School of Engineering, Osaka University
Mr. Hikaru Suzuki
Radial Gap type Doubly-fed Motor for Electric Aircraft
Energy conversion & environment laboratory, Graduate school of science and engineering, Toyo University
Mr. Ryo Shimizu
Axial-gap Double-fed Machine for Electric Aircraft
Energy conversion & Environment Laboratory, Electrical, Electronic and Communications Major, Graduate School of Science and Engineering, Toyo University
Mr. Kosei Kiyoura
Development of Compact Zθ Actuator
Hirata Laboratory, Department of Applied Science and Engineering, Osaka University
Mr. Yuta Toyoda
Characteristics of a induction motor installed in Tesla Model S
Energy Conversion and Environment Laboratory, Department of Electrical, Electronic and Communications Engineering, Toyo University
Mr. Akira Uemura
Prototype Demonstration of Single Sided Axial Flux Machine
Electrical Machinery Systems Laboratory, Department of Electrical and Electronic Engineering Faculty of Science and Technology, Shizuoka Institute of Science and Technology
Mr. Ryotaro Sano
The difference of the Interference Inductances detected in 2D/3D electromagnetic field FEM of Doubly-Salient SynRM
Chiba/Kiyota Laboratory, Department of Electrical and Electronic Engineering, School of Engineering, Tokyo Institute of Technology
Mr. Ryo Kokubu
In recent years, motor speeds have been increasing to improve power density. Motors are used with mechanical gears to obtain the desired torque and speed. Recently, mechanical gears that can operate at 50,000 rpm have been studied, but they are still in the research stage. This study focuses on magnetic gears that can transmit power without contact, and reports on the design of a magnetic gear that can operate at 80,000 rpm, as well as on prototype tests conducted.
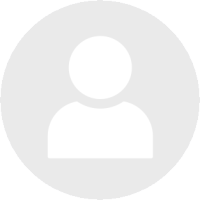
Weight reduction of actuator is required in Cobot which operates without fence, because it leads increase in speed and easiness of changing layout.
Therefore, in this research, Magnetic Worm-geared Motor (MWGM) imitating worm gear is proposed aiming at developing higher torque density motor. MWGM has a structure that linear motors along rotational axis rotates the rotor with diagonally distributed permanent magnets.
In this presentation, three-dimensional analysis of linear motor composing MWGM and MWGM itself will be introduced. The analysis of linear motor is used to compare the values of flux and thrust force with theory, and the analysis of MWGM is used to calculate torque and torque density. In these analyses, making models with variables enables changing the size in one study.
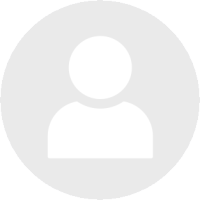
Induction motor (IM) is used for industrial equipment and EV, etc., because IM doesn’t use rare earth and they are simple and robust in structure. On the other hand, rotor temperature increases by no-load losses at no load test on the actual machine. In using IMs, it is undesirable for their losses to occur, so we want to keep their down. To do that, we first need to know how no-load losses occurs.
In this presentation, we report the mechanism of occurrence of no-load losses by doing 2D-transient response analysis at no-load on IM and confirming that transition of current density and flux line.
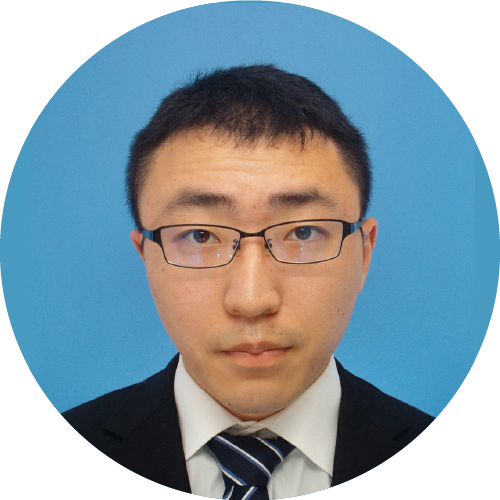
Concentrated winding structure generates the harmonic components of flux linkage, decreases its maximum output and efficiency. This research aims to improve the maximum output and efficiency by sinusoidal voltage drive to make sinusoidal flux linkage.
Convergence of sinusoidal voltage drive is very slow in FEM analysis and takes around 1 day. By applying voltages from the peak point, the number of steps to convergence is significantly reduced.
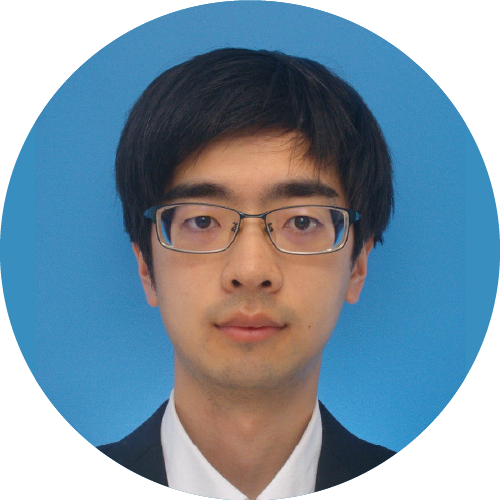
This study aims to realize a Wound Field Flux Switching Motor(WFFSM) that can switch to a Synchronous Reluctance Motor. For this purpose, a stator 12-pole/rotor 8-pole structure that can operate as a Synchronous Reluctance Motor is employed. This structure differs from the number of poles used in general WFFSMs (24 stator poles/10 rotor poles), and it is also necessary to consider the characteristics when the motor is driven as a Synchronous Reluctance Motor. Furthermore, a WFFSM has two types of windings (field winding and armature winding), so the number of design variables is much larger than in normal motor design, and the time required for optimization increases significantly. We report here that an optimization tool using a genetic algorithm can be used to search for a shape that can maximize torque in a short time.
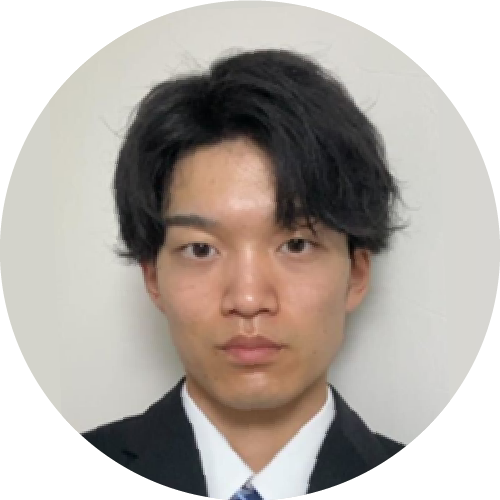
Mr. Naoki Saikawa
Switched reluctance motors (SRMs) suffers from high vibration and acoustic noise. In this study, aside from electromagnetic forces, the influence of magnetostriction on acoustic noise and vibration in SRMs is investigated.
In this presentation, magnetostriction measured using a closed-loop core is input to JMAG. Vibration analysis of the SRM is performed afterwards. The analysis results show that the vibration caused by the electromagnetic force and the magnetostriction cancel each other out. The same results were also confirmed in experiments.
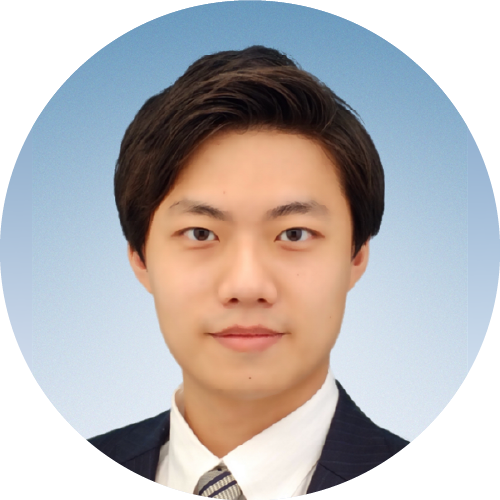
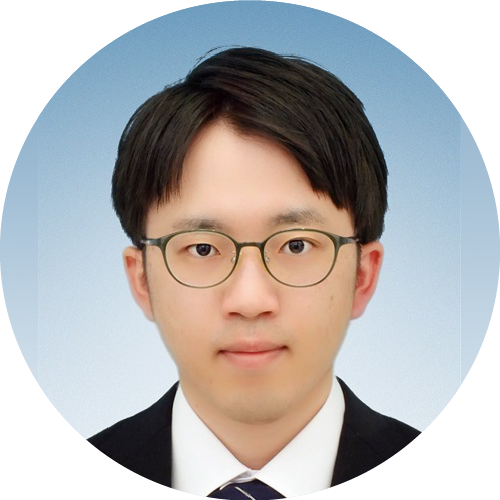
Aluminum windings is effective for reducing motor weight because the mass density is approximately one-third compared to copper windings. However, the motor efficiency is low due to low electrical conductivity. Therefore, the slot fill factor has been improved for reducing DC resistances. On the other hand, the efficiency is competitive at high-speed region because AC losses are increased.
In this presentation, the cause of winding AC loss in the high frequency region is clarified using FEM analysis in JMAG-Designer. In addition, a winding structure is proposed for reducing AC losses.
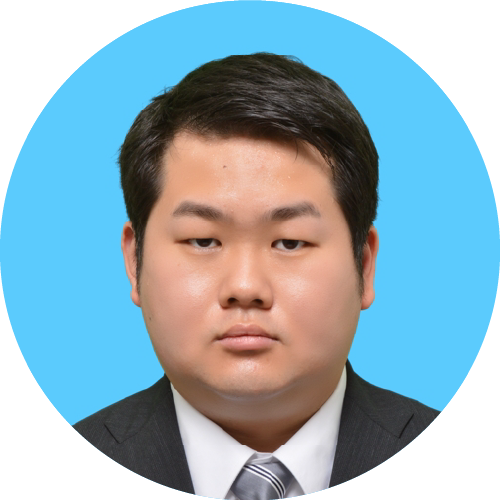
Small bus-type EVs are drawing attention for the mobility society of the future. This mobility requires a large interior space. Therefore, in-wheel motors, which are compact and capable of large output torque, are considered to be applied.
In this study, a new magnetic flux modulated motor is proposed based on the principle of a magnetic geared motor with two rotors: an inner rotor and a middle rotor. This motor has 2 operation modes by fixing one rotor. In this paper, the performance of 2 operation modes is compared using a coupled analysis between JMAG-Designer and MATLAB/Simulink in terms of the torque-speed characteristics. The maximum torque under field weakening control was the same. In addition, the phase current amplitude under field weakening control was not maximum for the maximum torque.
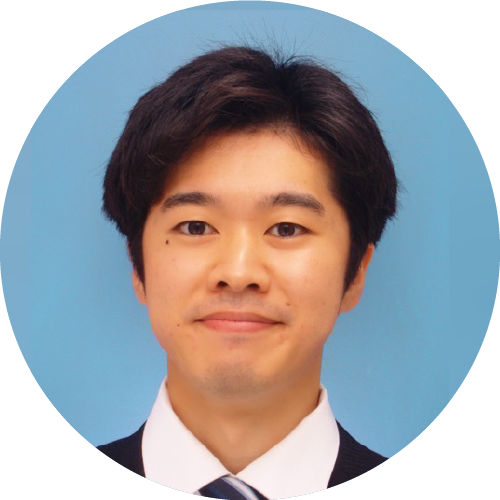
Drive motors for electric aircraft are required to be lightweight, high efficiency, and high output power. In this research, we are investigating a doubly-fed motor that can increase an output power by feeding powers from both sides of the stator and rotor. Our proposed doubly-fed motor can enhance the power density. It is expected that it will be lighter and more efficient by reducing iron loss by applying an air-core of air-gap winding. In addition, high output power is achieved due to high speed rotation and power feeding from both sides. In this poster, it is clarified the operating characteristics of a radial gap doubly-fed motor at high speed rotation by using JMAG-Designer.
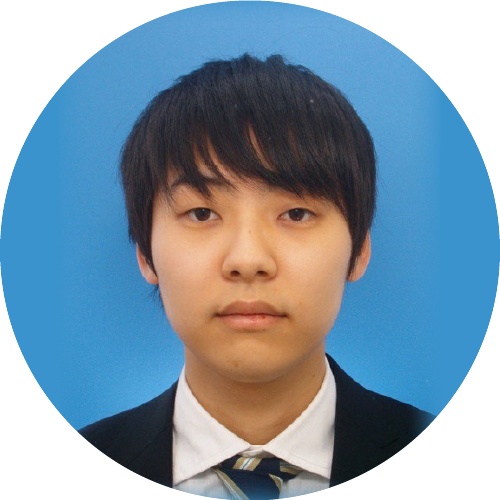
Recently, an axial gap motor with yokeless and segmented armature (YASA) has been garnering attention for electric vehicles. Motors for driving electric vehicles are required a light weight, compact structure, high power and high efficiency. If input po wers from stator and rotor are fed to machines, the output power increases significantly. We present characteristics of t he axial gap double fed machine w ith air core of air gap windings
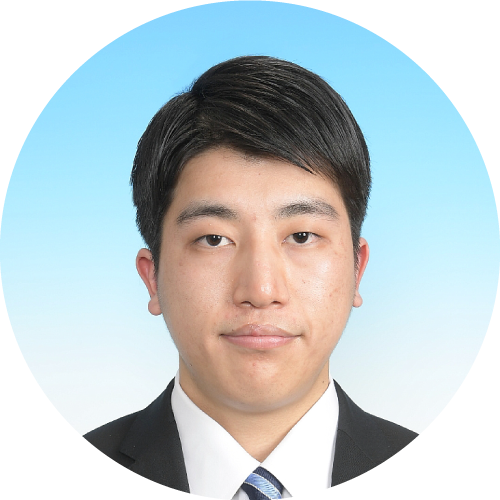
When components are mounted on a board in a chip mounter, a multiple-degree-of-freedom motion is required. Currently, there is a need to downsize the mechanism by using a single actuator to perform multiple-degree-of-freedom motions. In this presentation, we propose a Zθ actuator that can perform translational and rotational motions using only 1 set of coil. The structure is investigated to increase the thrust and torque using JMAG-Designer.
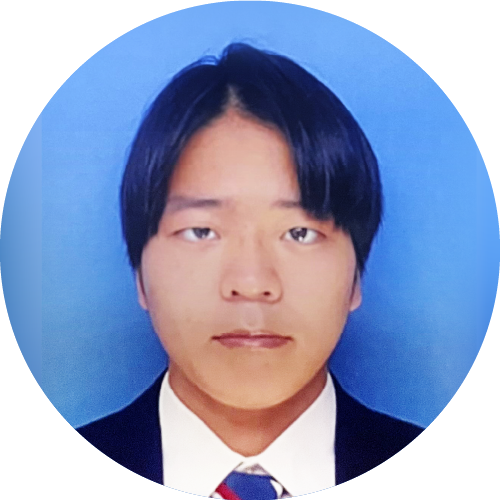
The induction motor installed in the Tesla Model S has the world’s top-level performance among electric vehicles. Then, a FEM field analysis of a frequency and transient response were performed to obtain and clarify the motor performance of the induction motor installed in the Tesla Model S.
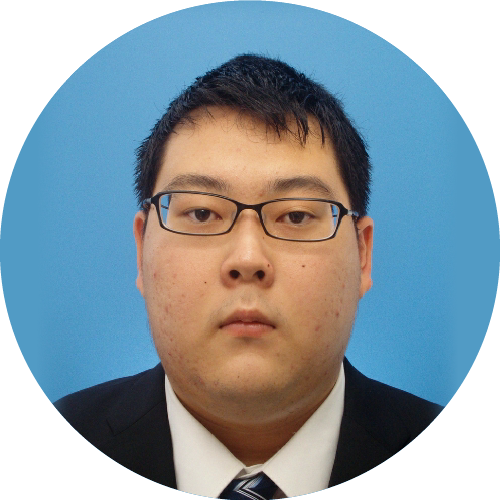
In this study, prototype demonstration of single sided axial flux machine has been researched to find out a suitable soft magnetic composite (SMC) solution with Höganäs Japan, Ltd.
In this presentation, we demonstrate the experimental test results of the axial flux machine with compacted SMC core.
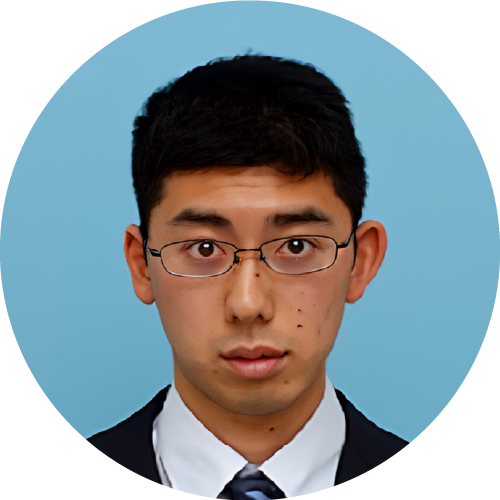
When an Open-Wound (OW) Doubly-Salient (DS) synchronous motor is driven by vector control, the interference inductances which consist of 3rd harmonic components between dq-axis and z-axes are introduced into the electrical equation. The effects of these zero-phase EMFs need to be considered into account for detailed verification of operation and control performance, but it has been found that there are several differences between 2D and 3D analyses using electromagnetic field FEA. In this session, 2D and 3D models of the target OW-DS SynRM are analyzed and generic models are built in JMAG-RT. The models are linked to a simulator created in MATLAB/Simulink and some simulations are performed assuming the actual device drive. It is shown that the zero-phase EMFs due to the interference inductances are different for each of the 2D and 3D models.
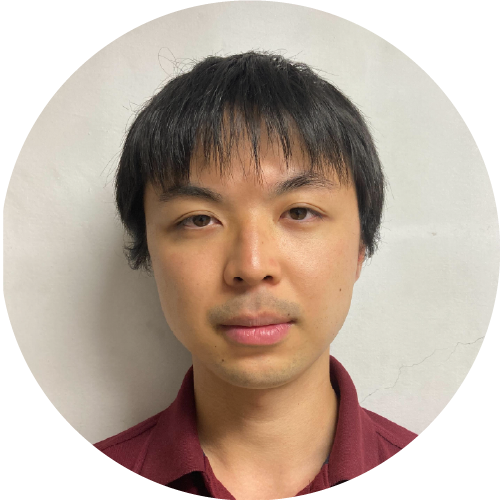