Overview
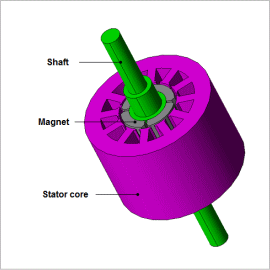
In order to grasp these at the design stage, highly precise evaluation sensitive to parts’ manufacturing errors is needed, so electromagnetic field analysis using the finite element method (FEM) is effective.
This Application Note presents how to evaluate the cogging torque waveform and effects on the electromagnetic force acting on the stator in an SPM motor with and without eccentricity.
Torque Waveform / Magnetic Flux Density Distribution
The torque waveform with and without eccentricity is indicated in fig. 1. The magnetic flux density distribution with a rotation angle of 180 deg at the largest difference in the position of the rotor is indicated in fig. 2. Torque variations occur with each one rotation of one period when eccentricity is applied, as indicated in fig. 1. The magnetic flux density increases in the direction of the eccentricity in the stator core, as indicated in fig. 2. This is how variations in the magnetic flux density distribution caused by eccentricity affect the torque waveform.
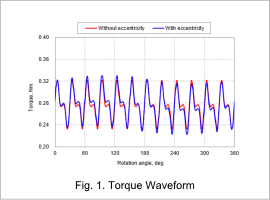
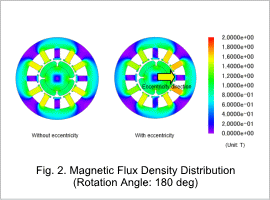
Electromagnetic Force Acting on the Stator
The eccentricity direction component of the electromagnetic force acting on the stator is indicated in fig. 3. The perpendicular direction component of the eccentricity is indicated in fig. 4. Each of the components has an electromagnetic force waveform with one period of one rotation due to eccentricity. Vibration and noise can be caused by electromagnetic resonance if the frequency component of the electromagnetic force acting on each part is close to the eigenmode of the motor.
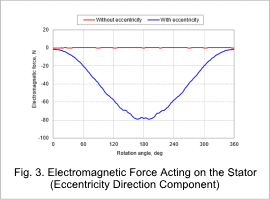
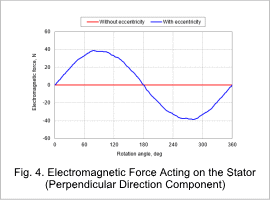