Overview
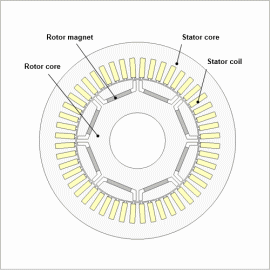
In simulations using the finite element method, iron loss can be calculated taking into account the effect of this stress and distortion.
In this example, an analysis of an IPM motor accounting for the residual strain that occurs as a result of punching processes, and evaluates the effect on torque, magnetic flux density, and iron loss.
Expressing Deterioration as a Result of Residual Strain
The deterioration that occurs as a result of residual strain is expressed via the deterioration coefficient in the cut plane, and the deterioration function from the surface.
Fig. 1 shows the permeability deterioration coefficient of the magnetic field dependency, and Fig. 2 shows the hysteresis loss correction coefficient of the magnetic flux density dependency.
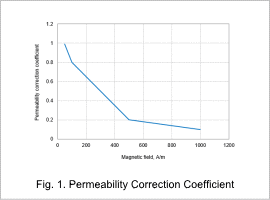
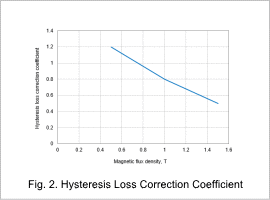
Effect on Magnetic Flux Density and Torque
Fig. 3 shows differences in magnetic flux density due to the presence or absence of residual strain, while Fig. 4 shows the comparison of average torque.
It can be understood from Fig. 3 that by accounting for residual strain, magnetic flux density grows smaller in the vicinity of the core cut plane. This is because permeability deteriorates due to manufacturing.
From Fig. 4, it can be understood that the effect on average torque from residual strain is approximately 1 %.
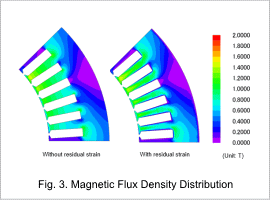
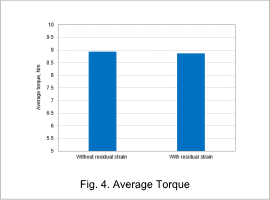
Effect on Iron Loss
Fig. 5 to Fig. 8 show the differences in the breakdown of iron loss, iron loss density, and hysteresis loss density, all from the presence or absence of residual strain.
It is understood from Fig. 5 that iron loss increases by approximately 13 % by accounting for residual strain.
From Fig. 6 to Fig. 8, it is understood that differences occur not only in hysteresis loss, but Joule loss also.
The increase in Joule loss occurs as a result of the deterioration of magnetization characteristics at the edges due to residual strain, as well as the increase in magnetic flux density at the center of the teeth.
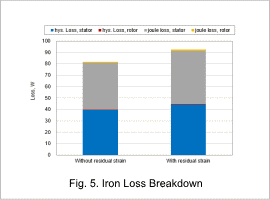

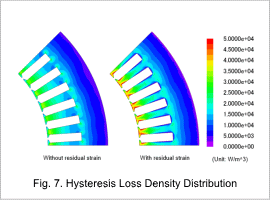
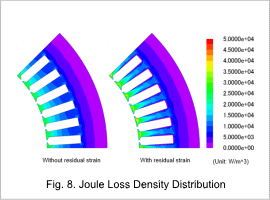