Overview
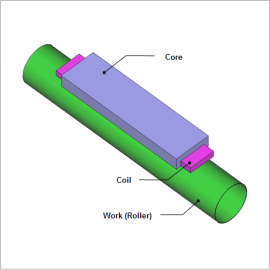
A magnetic field analysis using the finite element method (FEM) is useful in examining several aspects of the process, including: Differences in heating from the heating coil’s geometry or placement, what kind of eddy currents are generated in the roller’s thin surface and whether they provide uniform temperature, and how the magnetic flux flow spreads to the roller, air, and core.
This Application Note confirms the non-uniformity in temperature distribution produced by an assumed coil geometry, as well as the temperature elevation in each part caused by rotation.
Eddy Current Loss Density Distribution
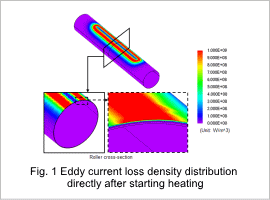
Temperature Distribution/Temperature Variation
The temperature distribution of the roller is indicated in figures 2 and 3, and the temperature variation of the roller surface is indicated in fig. 4. Fig. 4 indicates the temperature variation of the roller at the measuring points shown in fig. 2. The measuring points have been selected in order to be able to confirm the temperature variation in the circumferential direction and the rotation axis direction.
The roller is normally heated to a temperature of approximately 200 deg C, but in this analysis it is only analyzed for one full revolution.
From figures 2 and 3, it is apparent that the rotational motion causes the roller’s surface to be heated in a strip. The temperature increase in the area being heated is fairly even on the axis direction of the roller, as indicated in fig. 4. On the other hand, the temperature is not distributed evenly in the circumferential direction due to timing differences in heating, and heat dissipation into the air. The coil’s geometry does not allow it to generate heat in the center part, so the temperature elevation is not smooth.
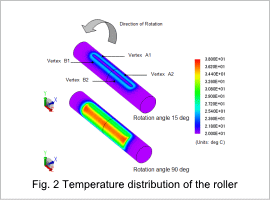
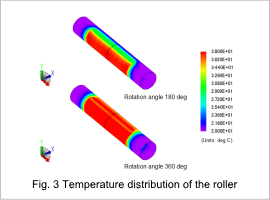
