*Please prepare a license ID and password for the license administrator.
*It is different from the service for JMAG WEB MEMBER (free membership). Please be careful.
Overview
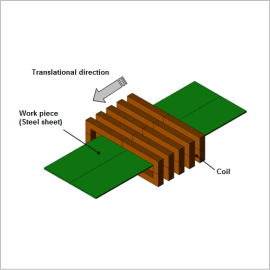
The rolling process of steel sheets changes the strength and properties of the product, so heat treatment is used. High frequency induction heating is a type of heat treatment that uses a high frequency power source to produce rapid heating, allowing the equipment on the production line to be smaller. It also has a multitude of benefits, such as being highly efficient and providing a clean working environment. When the object being heated is a long steel sheet, this process heats it quickly while sending it through a heating coil. For this reason, there are several factors that need to be studied when assigning a heating amount to correspond to the speed at which the sheet passes through the coil. Examples of these are: the arrangement of the heating coil so that it can fulfill the necessary heating amount, and how to adjust the current’s frequency and size.
This Application Note presents a simulation of the heating conditions of a sufficiently long steel sheet that passes through a heating coil. The eddy currents produced from the high frequency’s varying magnetic fields are uneven on the steel sheet’s surface, so its material properties change due to increases in temperature. This is why it is necessary to approximate the amount of heat generated in a numerical analysis based on the finite element method (FEM) in order to handle the detailed phenomena.
This Application Note explains how to create a numerical analysis model when obtaining the optimum coil geometry, current conditions (power supply frequency, current value), and movement speed. It also shows how to evaluate whether the model fulfills the target heating speed by analyzing the elevated temperature process.
This Application Note presents a simulation of the heating conditions of a sufficiently long steel sheet that passes through a heating coil. The eddy currents produced from the high frequency’s varying magnetic fields are uneven on the steel sheet’s surface, so its material properties change due to increases in temperature. This is why it is necessary to approximate the amount of heat generated in a numerical analysis based on the finite element method (FEM) in order to handle the detailed phenomena.
This Application Note explains how to create a numerical analysis model when obtaining the optimum coil geometry, current conditions (power supply frequency, current value), and movement speed. It also shows how to evaluate whether the model fulfills the target heating speed by analyzing the elevated temperature process.
Eddy Current Loss Density Distribution
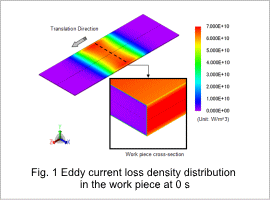
Fig. 1 shows the eddy current loss density distribution in the work piece’s surface, as well as a cross section. Eddy currents are generated in the work piece by the magnetic field produced by the coil. Eddy currents generated by the skin effect are distributed through the surface of the work piece.
Temperature Distribution
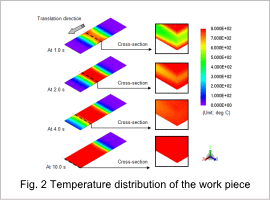
Fig. 2 shows the temperature distribution in the work piece. The eddy currents generate heat in the work piece, and after having moved through the coil for 10 s it has been heated to a temperature of over 800 deg. Moving the work piece through the coil at 0.1 m/s heats it without almost no irregularities in temperature. Heat transmission heats the work piece’s interior, as well.