Event Overview and Introduction
POWERSYS is pleased to announce that the JMAG Users Conference will be held in DETROIT, MICHIGAN, USA on OCTOBER 16th, 2012.
The JMAG Users Conference
Organizer | POWERSYS |
---|---|
Date | October 16th, 2012 |
Venue |
WESTIN DETROIT METROPOLITAN AIRPORT HOTEL 2501 Worldgateway Place Detroit, Michigan 48242 Phone: (734) 942-6500 |
Program of the conference
8:00 | Registration / breakfast |
---|---|
8:50 | Opening session |
9:00 | Magnetic Gears Hamid A. Toliyat, Texas A&M University (Keynote Speaker of the conference) |
9:45 |
Resistivity analysis of stacked planar Litz structure using Finite Element Method Tsuyoshi Nomura, Toyota Inductor loss-simulation using JMAG-Designer and comparison with measurement results Kayoko Seto, Toyota |
10:30 | Estimating the effects of partial flux linkages on the resistance of PMAC motor windings John Suriano, Nidec |
11:00 | Break 15min |
11:15 | High Fidelity Hardware-in-the-Loop Simulation with JMAG-RT and NI VeriStand Nick Keel, National Instruments |
11:45 | Flux Focusing Magnetic Gear Design Using JMAG Jonathan Bird, University of North Carolina – Charlotte |
12:15 | Lunch |
13:15 | Designing Novel Doubly-Fed Machines using JMAG Andy Knight, Alberta University |
13:45 | Effects of manufacturing process on IPM motor losses Hossein Dadkhah and Anand Sathyan, Chrysler |
14:15 | Multiscale Noise and Vibration models for a Switched Reluctance-based drivetrain for EV and HEV Ramana Kappagantu, Ph.D. – Sr. Technical Specialist, LMS Americas |
14:45 | Break 15min |
15:00 | Evaluation of Different Electrical Steels in IPM Hybrid Rotating Machines C.R. Frontczak, Tempel |
15:30 | Highlights of the latest developments of OPAL-RT solutions Sebastien Cense, OPAL-RT Technologies Inc. |
16:00 | Break 15min |
16:15 | Introduction to JMAG V12 JSOL |
16:45 | To be defined Simulia |
17:15 | Electrical Machines for Automotive Applications and a second look at Induction Machines Sinisa Jurkovic, General Motors |
17:45 | Cocktail |
Poster
Let’s discuss technical issues with JMAG development engineers and support engineers.
- Analysis Methods for SR Motors
- Specialized Evaluation Methods for PM Motor Development
- Analysis Technology for Highly Efficient Generator Design
- Induction Machines — Introducing Analyses by Application
- Power Transformers — Comprehensive Analyses for Robustness and Safety
- Analysis Technology for Electromagnetic Induction Heating
- Electromagnetic Vibration Analyses of Motors
- JMAG + Circuit Simulator
Our sponsors
Information
JMAG – 1 Day FREE Training will be held on October 15th, that is the preceding day of this conference.
Please attend this event as well.
JMAG Users Conference in USA – October 16th, 2012 Detroit, USA SPEAKERS & TOPICS
Magnetic Gears
Hamid A. Toliyat, Texas A&M University
Keynote Speaker of the conference
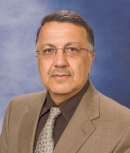
Hamid A. Toliyat (S’87, M’91, SM’96, F’08) received the B.S, degree from Sharif University of Technology, Tehran, Iran in 1982, the M.S. degree from West Virginia University, Morgantown, WV in 1986, and the Ph.D. degree from University of Wisconsin-Madison, Madison, WI in 1991, all in electrical engineering. Following receipt of the Ph.D. degree, he joined the faculty of Ferdowsi University of Mashhad, Mashhad, Iran as an Assistant Professor of Electrical Engineering. In March 1994 he joined the Department of Electrical and Computer Engineering, Texas A&M University where he is currently Raytheon endowed professor of electrical engineering.
Dr. Toliyat has received the prestigious Cyrill Veinott Award in Electromechanical Energy Conversion from the IEEE Power Engineering Society in 2004, Patent and Innovation Award from Texas A&M University System Office of Technology Commercialization’s in 2007, TEES Faculty Fellow Award in 2006, distinguished Teaching Award in 2003, E.D. Brockett Professorship Award in 2002, Eugene Webb Faculty Fellow Award in 2000, and Texas A&M Select Young Investigator Award in 1999 from Texas A&M University. He has also received the Space Act Award from NASA in 1999, and the Schlumberger Foundation Technical Awards in 2001 and 2000.
Dr. Toliyat was an Editor of IEEE Transactions on Energy Conversion. He was Chair of the IEEE-IAS Industrial Power Conversion Systems Department of IEEE-IAS, and is a member of Sigma Xi. He is a fellow of the Power Engineering, Industrial Applications, Industrial Electronics, Power Electronics Societies of the IEEE, and the recipient of the 2008 Industrial Electronics Society Electric Machines Committee Second Best Paper Award, 1996 and 2006 IEEE Power Engineering Society Prize Paper Awards and 2006 IEEE Industry Applications Society Transactions Third Prize Paper Award. His main research interests and experience include analysis and design of electrical machines, variable speed drives for traction and propulsion applications, fault diagnosis of electric machinery, and sensorless variable speed drives. Prof. Toliyat has supervised more than 50 graduate students, published over 370 technical papers where over 110 papers are in IEEE Transactions, presented more than 80 invited lectures all over the world, and has 12 issued and pending US patents. He is the author of DSP-Based Electromechanical Motion Control, CRC Press, 2003, Co-Editor of Handbook of Electric Motors – 2nd Edition, Marcel Dekker, 2004, and Co-author of Electric Machines – Modeling, Condition Monitoring, and Fault Diagnosis, CRC Press, Florida, 2012.
He was the General Chair of the 2005 IEEE International Electric Machines and Drives Conference in San Antonio, Texas. Dr. Toliyat is a Professional Engineer in the State of Texas.
Abstract:
Although magnetic counterparts of the mechanical gears were first introduced in the early twentieth century, it was not until recently that they caught significant interest from the researchers in the field as a promising technology for various torque-demanding applications; specifically among which is the rapidly growing market of EVs and HEVs. While enjoying a high torque density upon use of high energy density permanent magnets, magnetic gears offer several advantages over mechanical gears: very low to no maintenance requirement, low noise operation, and inherent overload capability. This talk, first, brushes over different types of magnetic gears and then focuses on a particular type which has attracted attentions the most: concentric planetary gear. Its structure and modes of operation are presented and it is shown how Two-Dimensional (2D) and Three-Dimensional (3D) Finite Element Analysis (FEA) can be employed to analyse this magnetic device.
JMAG Users Conference in USA – October 16th, 2012 Detroit, USA SPEAKERS & TOPICS
Resistivity analysis of stacked planar Litz structure using Finite Element Method
Tsuyoshi Nomura, Toyota
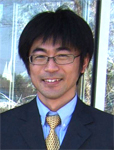
Tsuyoshi Nomura received the B.S. and M.S. from the Department of Mechano-Informatics and Systems, Nagoya University, Japan, in 1995 and 1997, respectively, and the Ph.D. degree from Department of Aeronautics and Astronautics, Kyoto University, Japan, in 2008. He joined Toyota Central Research and Development Laboratories, Inc. in 1997. He has been engaged in research on numerical analysis of composite materials and topology optimization. Since 2011, he is on a research assignment at Toyota Research Institute of North America, Ann Arbor, Michigan.
Abstract:
Planar type inductors provide an opportunity to meet the size requirement, but improving efficiency, especially at elevated frequency, still needs great research efforts. Since AC winding loss (caused by proximity effect and skin effect) takes a significant portion in high frequency inductor loss, Litz wire structure windings are being investigated. In 2005, PCB type Litz wire windings for planar inductors was proposed, in which the analysis was focused on single board structure. However, inductors in automotive applications require multiple winding layers, but so far there is no published work addressing planar Litz wire stacking and its effect to Litz wire performance. This paper will discuss the multiple winding layers stacking effect, i.e. proximity effect between layers, and how it affects the optimization of the Litz wire strand width and pitch. The analysis is based on FEM with periodic boundary condition in order to model stacking configuration with available computational resources.
JMAG Users Conference in USA – October 16th, 2012 Detroit, USA SPEAKERS & TOPICS
Inductor loss-simulation using JMAG-Designer and comparison with measurement results
Kayoko Seto, Toyota

Kayoko Seto received the B.S. and M.S. degree from the Department of Electrical and Electronic Engineering, Kobe University, Japan, in 2007 and 2009 respectively.
She has been an engineer at Toyota Motor Corporation since 2009. She has been engaged in the developing of automotive custom ICs and its applications such as a brake system, etc. She is now with Toyota Research Institute of North America, Ann Arbor, Mi.
Abstract:
Reducing an inductor loss is important for automotive power electronics systems. Many efforts on inductor structure designs depend on experiences and prototypings. This process takes time and cost, and an accurate simulation can make the process more efficient. In this paper, a design method of planer type inductors for high current and high frequency applications is introduced. Wire-loss is a time-consuming simulation and difficult to understand phenomena of loss such as eddy current loss, skineffect, etc. Individual loss measurements and core loss and wire loss fittings considering these phenomena meke an accurate inductor design available.
JMAG Users Conference in USA – October 16th, 2012 Detroit, USA SPEAKERS & TOPICS
Estimating the effects of partial flux linkages on the resistance of PMAC motor windings.
John Suriano, Nidec
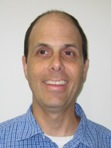
John Suriano received a bachelor’s degree in Electrical Engineering from GMI Engineering & Management Institute in 1985. He received a master’s and PhD degrees in Electrical Engineering from Purdue University in 1986 and 1992 respectively. John has been involved in the design and analysis of electric motors for the automotive industry for more than 1/4 century. Presently he is the supervisor of the electromagnetic compatibility laboratory for Nidec Motors & Actuators in Auburn Hills, MI.
Abstract:
Similar to the well known deep bar effect in AC induction motors, the winidngs of permanent magnet AC machines experience an increase in effective resistance as the frequency of excitation current from the winding increases. The field produced by the winding forces current toward the open end of the stator slot leading to non-uniform current density in the coils. The effect is caused by flux which leaks across the slot only partially linking the coils. Ignorance of this effect can lead to poor stator winding design and a loss of efficiency from the machine. This presentation uses JMAG to illustrate this effect and to compare various winding designs. Test results are also used to bolster the conclusions.
JMAG Users Conference in USA – October 16th, 2012 Detroit, USA SPEAKERS & TOPICS
High Fidelity Hardware-in-the-Loop Simulation with JMAG-RT and NI VeriStand
Nick Keel, National Instruments
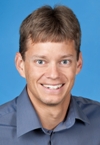
Nick Keel is the NI VeriStand Product Manager at National Instruments. He works extensively with real-time testing and hardware-in-the-loop applications. Prior to working at National Instruments, he spent 6 years in the United States Navy working as a nuclear reactor operator on a submarine. He has worked for National Instruments for about 4 years, and he has a BSEE from The University of Wisconsin.
Abstract:
The role of electric motors in the automotive and energy industries is expanding. Testing embedded software for electric motor ECUs introduces new challenges, such as increased simulation speed and model fidelity, that cannot be addressed by traditional HIL testing methods. Learn about how National Instruments and JMAG have partnered together to address these new challenges by creating an industry leading electric motor simulation platform for hardware-in-the-loop testing.
JMAG Users Conference in USA – October 16th, 2012 Detroit, USA SPEAKERS & TOPICS
Flux Focusing Magnetic Gear Design Using JMAG
Jonathan Bird, University of North Carolina – Charlotte
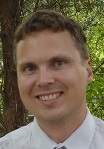
Jonathan Bird, obtained his B.S from the University of Auckland in 2000 and his M.S. and Ph.D. from the University of Wisconsin-Madison in 2004 and 2006 respectively. From 2006 to 2008 he was a senior design engineer at General Motors Advanced Technology Center in Torrance, CA. Since 2009 he has been an Assistant Professor at the University of North Carolina at Charlotte. His research interests are in the areas of electric machine design, electromagnetics and control.
Abstract:
A magnetic gearbox offers many advantages over its mechanical counterpart such as contact free torque production, no gear lubrication and inherent overload protection. Current magnetic gear designs use rare-earth magnet material. Unfortunately, for the foreseeable future, devices using large quantities of rare-earth material are not going to be cost competitive with existing gear technology. This paper investigates the performance of low cost flux focusing magnetic gears using ferrite magnets. Parameter optimizing as well as the influence of eddy current loss and demagnetization issues will be studied using JMAG.
JMAG Users Conference in USA – October 16th, 2012 Detroit, USA SPEAKERS & TOPICS
Designing Novel Doubly-Fed Machines using JMAG
Andy Knight, Alberta University
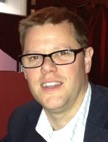
Andy. Knight received the Ph.D. degree in Electrical Engineering from the University of Cambridge, U.K., in 1998. In 1999, he joined the University of Alberta, where he is currently a Professor with the Department of Electrical and Computer Engineering. His research interests include energy conversion and storage, particularly renewable energy and electrical machines and drives; practical aspects of analysis and design of electric machines; modeling of nonlinear electromagnetic systems and losses in those systems. Dr. Knight is a recipient of the IEEE PES Prize Paper Award and three prize papers from the IEEE IAS
Abstract:
Brushless doubly fed machines are a class of machine that has existed for over 100 years. At various points in this history, researchers have published results that indicate the potential benefits of this type of machine relative to other more common machines. However, consistently good designs are hard to find and there are several examples of poor designs in the literature. Some of the reasons for this include the difficulty in modelling the complex interaction of the magnetic fields produced by two stator windings with different pole numbers and the difficulty in accurately predicting iron losses. In the talk, the results of a systematic design approach using JMAG will be presented. The importance of nonlinear modeling to accurately predict mutual coupling between windings and leakage will be presented, together with structural analysis of the rotor design.
JMAG Users Conference in USA – October 16th, 2012 Detroit, USA SPEAKERS & TOPICS
Effects of manufacturing process on IPM motor losses
Hossein Dadkhah and Anand Sathyan, Chrysler
Hossein Dadkhah received a B.S. degree in Electrical engineering from the University of Alabama – Huntsville, AL in 1989, M.S. degree in electrical engineering and MS degree in engineering Management from the University of Alabama in 1993 and 1999 respectively. He is currently employed at Chrysler LLC – Auburn hills, Michigan, where he is responsible for electric machine design, development and integration for HEV/PHEV and EV vehicles. He has a wide experience in automotive electronics component and subsystem design and development and manufacturing process, electrified powertrain, power electronics and electric motors, audio and telematics component and system, RF, antenna and tuners, Circuit board design, EMI/EMC, passive safety components and systems, and electric motor advance design and modeling.
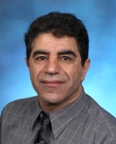
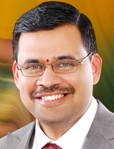
Abstract:
Finite Element Analysis (FEA) is widely used for motor design and performance evaluation. Most FEA tools are good at predicting the torque, power and back emf values. However loss measurement varies widely between simulation and experimental results. Manufacturing process can have a major role in determining how much this loss variation would be. This presentation will give an introduction to the various losses in an Interior Permanent Magnet Machine followed by a review of how the manufacturing process can affect these losses.
JMAG Users Conference in USA – October 16th, 2012 Detroit, USA SPEAKERS & TOPICS
Multiscale Noise and Vibration models for a Switched Reluctance-based drivetrain for EV and HEV
Ramana Kappagantu, Ph.D. – Sr. Technical Specialist, LMS Americas
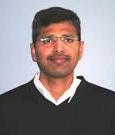
Dr. Kappagantu has been working in the simulation industry for the past 20+ years. He worked at Ford Motor Company developing and implementing methods for NVH for 8 years. He continued to work on NVH solutions at Material Sciences Corporation for 4 years designing Body panels and Brake NVH products. For the past 5 years he is working at LMS Americas primarily on simulation side of their business handling Acoustics, Vibrations, Durability and Multi-Body Dynamics.
Abstract:
The recent growth in Electric and Hybrid Electric Vehicles has resulted in the increased use of electric motors in automotive vehicles. At the same time, the cost of materials (magnets) have also gone up multi-fold. This resulted in the increased use of switch reluctance motors for drivetrains and other auxilaries. They are inherently noisy and contribute to the NVH degradation of the vehicle. In this presentation we would address the modeling and analysis of SRM by integrating EM solutions like JMAG with Vibration & Acoustic solutions like LMS/Virtual.Lab.
JMAG Users Conference in USA – October 16th, 2012 Detroit, USA SPEAKERS & TOPICS
Evaluation of Different Electrical Steels in IPM Hybrid Rotating Machines
C.R. Frontczak, Tempel
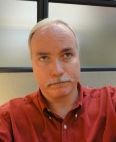
Mr. Frontczak has 24 years of experience in the field of electrical rotating machines. His accomplishments include clean sheet and redesigns of all types of machines ; including PMDC, BLDC, AC Induction, AC Asynchrounous, Shaded Pole, Switched Reluctance, and Stepper Motors. During his time with Tempel, Mr. Frontczak has worked on other types of machines as well, i.e. transformers, ignition coils, and generators. It is here where Mr. Frontczak utilizes the JMAG software to help solve design questions from customers.
Abstract:
The use of JMAG allowed me to create multiple case studies in which I change the electrical steel grades in order to determine which steel properties would yield the best motor performance. This presentation takes the viewer through the set-up and logic the F.E. Model, and shows the results in terms of motor parameters.
JMAG Users Conference in USA – October 16th, 2012 Detroit, USA SPEAKERS & TOPICS
Highlights of the latest developments of OPAL-RT solutions
Sebastien Cense, OPAL-RT Technologies Inc.
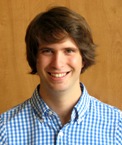
Sebastien Cense received his B.S. and M.S. degrees in micro electronics from the ISEN Engineering School in Lille, France in 2010. His final paper on FPGA embedded command of polyphase motor using space vector algorithm was conducted at the Arts et Metiers Paris Tech in collaboration with OPAL-RT. He joined OPAL-RT in October 2010 where he has been engaged in developing FPGA application solutions such as rapid control prototyping and on-board motor simulation. Sebastien also contributed to a number of technical presentations.
Abstract:
As motor controller’s algorithms become more complex, so do tests and development of new control strategies. This presentation will highlight the latest developments of OPAL-RT solutions to work efficiently with these new challenges and to improve time to market of electric motor drive systems. JMAG-RT v10.5 spatial harmonics PMSM model was chosen as the company’s new standard for accurate FPGA-based simulation of PMSM motors.
Learn how to use the results of the finite element analysis of your motor to build your own FPGA-based HIL model in a few quick and easy steps. As the development of FPGA-based systems is more for advanced users, OPAL-RT development is oriented towards non-flashing technology using a generic and optimised approach to solve power electronics circuit. OPAL-RT turnkey system for ECU testing and rapid motor prototyping is in line with this philosophy as the user interfaces allow easy modification of motor or drive topology without requiring knowledge in FPGA or reprogramming the board.