A Powerful Simulation Engine
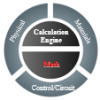
This edition introduces the value and future of one of the two major foundations of the simulation engine, the mesh generation engine.
Optimized Mesh for Analysis of Electromechanical Machines
The JMAG mesh generation engine is for specialized analyses of electromechanical machines. The mesh is optimized based on the needs of our users.
There is a wide range of phenomena acting on electromechanical devices from magnetic saturation and the skin effect to electromagnetic induction and motion. The areas that interest each user differ with the various phenomenon requiring a unique mesh for each type of analysis. This means that our users need the ability to generate a wide range of mesh.
A highly accurate mesh can be generated based on the analysis experience of the user with the universal mesh generation engines that are on the market today, provided there is enough time. However, the need to be able to generate a high quality mesh “simply” is huge. CAE is a tool used to “support” in manufacturing, and is not beneficial unless it can be used in the design and development process.
The JMAG mesh generation engine specializes in the analysis of electromechanical machines, requiring no analysis experience and very little time. A mesh that accurately simulates a wide range of electromagnetic phenomena can be generated simply. A comparison of eddy current losses obtained by generating mesh at different resolutions is indicated in Fig. 1. The resolution of the mesh affects the results that are obtained.
Fig. 1 Comparison of eddy current loss with different resolutions of mesh [1]
Accuracy and Simplicity is Vital
The mesh generation engine in JMAG that specializes in analyzing electromagnetic machines focuses on a highly accurate mesh that is simple to generate. Two areas of development that allows JMAG to enhance the accuracy of the mesh while making it simpler to generate are outlined below.
(1) Improving accuracy by reducing mesh noise
A high quality of mesh is necessary because a highly accurate cogging torque analysis is required to further reduce the cogging torque of motors, which is only approximately 0.1% of the output torque, in addition to reducing vibration and noise. In this case, the mesh noise affects the analysis causing inaccurate results.
The JMAG mesh generation engine reduces the mesh noise using noise canceling technology. The noise canceling technology allows for the cogging torque to be examined highly accurately without any analysis experience. A comparison of the cogging torque with and without noise canceling technology is indicated in Fig. 2. The periodicity and symmetry of the cogging torque waveform becomes deformed when the mesh noise is not reduced causing inaccurate analysis results while the accuracy can be maintained when the mesh noise is reduced.
(2) Automatically generating high quality mesh efficiently
Generating mesh is merely a part of creating a model for an analysis. However, generating an appropriate mesh necessary to improve the accuracy of an analysis requires the user understands the electromagnetic phenomena occurring within machines and has the pertinent analysis experience. The user has to be capable of automatically generating a high quality mesh efficiently to obtain accurate results.
The JMAG mesh generation engine is enhancing the automatic mesh generation function that can generate a high quality mesh using adaptive mesh. Adaptive mesh generates the optimal mesh for a highly accurate analysis of electromagnetic phenomena while linking to the JMAG solver in the program.
A high quality mesh can be automatically generated efficiently without the user being aware of its existence. The Keihin Corporation presented a hands on example of the automatic mesh generation function for developing actuators at the JMAG Users Conference 2005.
Fig. 2. Comparison of cogging torque with and without noise canceling technology[2]
Robustness and Speed is Vital
Of coarse, specialized analysis of electromechanical machines is not the only vital aspect of development. The robustness to geometry and data as well as the speed the mesh can be generated is also indispensable. An analysis cannot be performed if the mesh cannot be generated accurately, yet performing an analysis that requires a vast amount of time to generate mesh is also pointless.
The JMAG mesh generation engine is faster than ever before. The variations of the time required to generate mesh with the different mesh engines is indicated in Fig. 3. The time required to generate mesh in the new mesh generation engine has been reduced to 1/9 of the time required for the conventional mesh generation engine, although the time required depends on the analysis target and number of elements.
Specialized Mesh Team
The JSOL corporation strives to continually enhance the JMAG mesh generation engine to satisfy the needs of our users. The mesh team is responsible for the vast research and development that has been implemented into JMAG.
Fig. 3. Variations of time required to generate mesh with the different mesh engines
The JMAG mesh team provides technology to generate the right mesh for analyzing electromechanical machines based on years of analysis experience. The technology is obviously implemented into JMAG, but the mesh team also actively communicates with our users by providing papers of their research, such as [2]-[5], while continually receiving feedback directly from our users.
Cutting-Edge JMAG Mesh Generation Solver for Electromagnetic Field Analysis
The JMAG mesh generation engine will continue to evolve, enhancing the accuracy and speed as well as supporting larger scale models. There are still many avenues of innovation that can be taken to provide our users with the most accurate mesh that can be generated simply.
JMAG will continue to push the boundaries of electromagnetic field analyses aiming for “simplicity” as part of the modeling process while providing “high quality” mesh vital to achieving the highest level of analysis accuracy.
The next edition introduces material modeling for simulations.
[1] : JMAG Users Conference 2008 Poster Session
[2] : K.Tani, H.Hashimoto, T.Yamada,”High Accuracy Torque Calculation for a Rotating Machine Using Adaptive Meshing,”IEEJ-D, Vol.123, No.7 pp.790-797, 2003
[3] : K.Tani, T.Yamada, Y.Kawase, “Dynamic Analysis of Linear Actuator Taking into Account Eddy Current Using Finite Element Method and 3-D Mesh Coupling Method,” IEEJ SA-98-10, RM-98-74, 1998
[4] : K.Tani, T.Yamada, Y.Kawase, “3D Mesh Generation Procedures And Error Estimation Procedures to Magnetic Field Analysis of Magnetic Heads by Finite Element Method,” IEICE technical report MR98-52, pp.29-35, 1999
[5] : K.Tani, T.Yamada, Y.Kawase, “Dynamic Response Analysis of Linear Actuator Using Finite Element Method and 3-D Mesh Coupling,”IEEJ SA-99-16, RM-99-70, 1999
[JMAG Newsletter Winter, 2010]