Overview
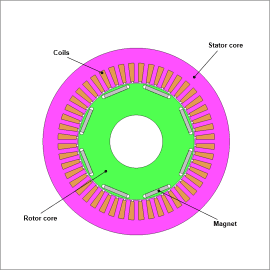
Designers have to optimize not only the dimensions of the motor geometry but also the winding design to find solutions that can satisfy these sophisticated requirements.
Discrete optimizations are effective when using integer values to set the number of coil turns and standard wire diameters as design variables. These optimizations can also account for the thickness of laminated steel sheet. An optimization that treats these variables as continuous values require designers to round the optimization results to the nearest integer feasible for the design before running another analysis. These subsequent simulations often encounter problems, such as results that no longer satisfy the constraint conditions after rounding the optimization results. A discrete optimization can precisely evaluate the objective functions and constraint conditions.
This case study optimizes IPM motor geometry and coil turns by using objective functions to maximize the average efficiency of several operating points and minimize the volume to lower costs.
Optimization Conditions
The design variables are outlined in Table 1, the objective functions in Table 2, the constraint conditions in Table 3 and the parametric variables in Fig. 1.
The average efficiency is the average of the efficiency for the following five operating points:
– 1,000 r/min; 20 Nm
– 1,000 r/min; 300 Nm
– 3,000 r/min; 300 Nm
– 4,000 r/min; 100 Nm
– 9,000 r/min; 20 Nm
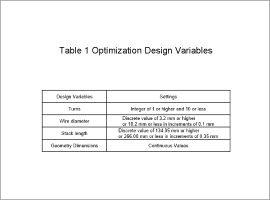
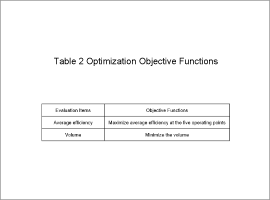
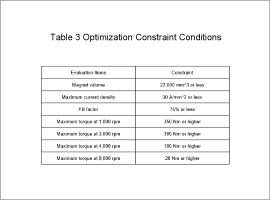
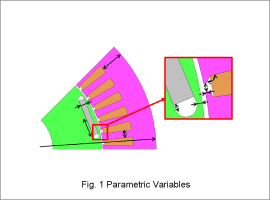
Optimization Results
Fig. 2 illustrates the distribution of the objective functions for feasible solutions obtained by the optimization. Fig. 3 presents the distribution of turns and wire diameter for the feasible solutions. The graphs also plot results for an optimization using continuous values for all of the design variables for comparison. Fig. 4 shows the distribution of constraint functions for the Pareto solutions. Fig. 5 indicates the changes in the objective functions of the Pareto solutions after rounding results to the nearest digit. The graph plots the results of a second optimization after rounding the turns, wire diameter, and stack length obtained by the continuous optimization to the nearest digit to satisfy the discrete constraints. The yellow arrows illustrate the changes in the Pareto front after rounding the initial results. Fig. 6 and Table 4 provide an efficiency map for initial design and one for a Pareto solution selected from the discrete optimization.
As illustrated by Fig. 2 and Fig. 3, the continuous optimization has a Pareto front with better progression while the discrete optimization results provide a distribution of discrete values exactly as specified.
However, many of the design solutions violate the constraint conditions once the results are rounded to the nearest digit as seen in Fig. 4.
The progress made by the Pareto front recedes, especially in the high efficiency region as seen in Fig. 5. This demonstrates how a continuous optimization overestimates the results. Moreover, many of the solutions once rounded to the nearest digit no longer satisfy the constraint conditions, which drastically reduces the number of feasible solutions compared to a discrete optimization.
As illustrated by Fig. 6 and Table 4, the optimization obtains design solutions for a motor that is smaller with higher average efficiency than the initial design.
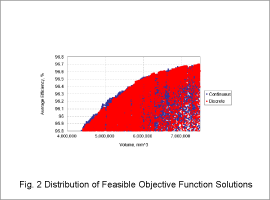
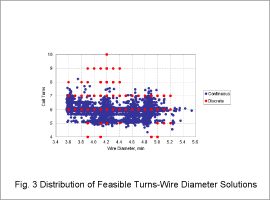
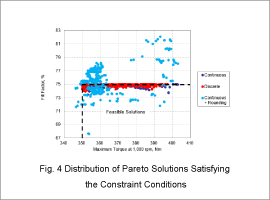
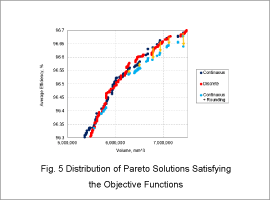
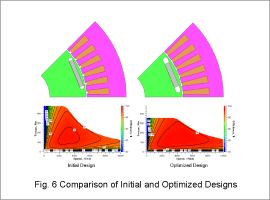
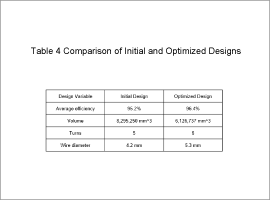