Overview
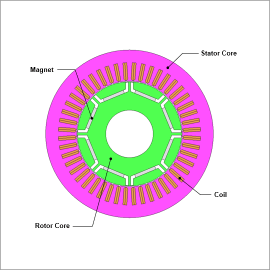
Simulations that use temperature-dependent efficiency maps can evaluate the rise in losses as the temperature of the coil and magnets increase during the drive cycle. Users can configure a thermal circuit to create a cooling model using a wide range of components, including cooling jackets and spray shaft cooling that accounts for temperature variations resulting from the cooling.
This case study evaluates the losses and temperature changes over time of an IPM motor during a WLTC drive cycle using temperature-dependent efficiency maps.
Analysis Flow
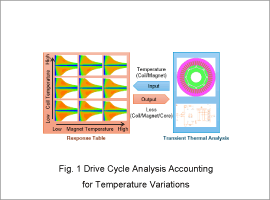
The magnetic field analysis generates multiple efficiency maps that include the loss data according to the temperatures of both the coils and magnets.
The thermal analysis extracts the heat generation of each part from the efficiency map to obtain the temperatures at the current step based on the operating points of the drive cycle and the temperatures in the previous step.
Efficiency Map Before/After Temperature Rise
Fig. 2 indicates the operating points of the motor for the efficiency maps during the WLTC drive cycle. Fig. 3 presents efficiency maps before and after the temperature rise. Fig. 4 provides a loss difference map.
The operating points of the motor during the WLTC drive cycle expand over a broad area as seen in Fig. 2.
The maximum efficiency as the temperature rises in the parts declines about 6 points as seen in Fig. 3.
The higher coil temperature causes the copper losses to rise in the coil under high load due to larger resistance as seen in Fig. 4, but the iron losses in the stator decline at high speeds as the flux decreases due to higher magnet temperatures. That is why a drive cycle analysis is essential to account for the phenomena caused by complex changes in the losses resulting from higher temperatures in each part.
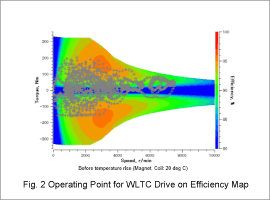
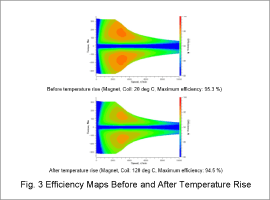
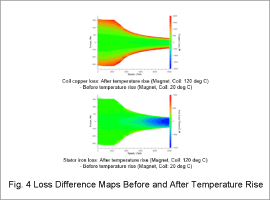
Drive Cycle Analysis Accounting for Temperature Variations
This case study ran a WLTC drive cycle analysis accounting for temperature variations in the coils and magnets. Fig. 5 illustrates the losses in each part over time. Fig. 6 presents the temperature variations over time.
The losses in the stator core and coil are high as seen in Fig. 5.
The temperatures of the stator core and coil that have numerous losses are not only high but change quickly as seen in Fig. 6.
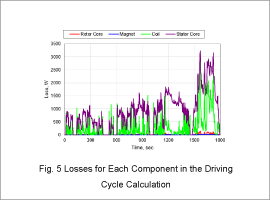
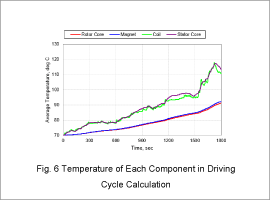