Overview
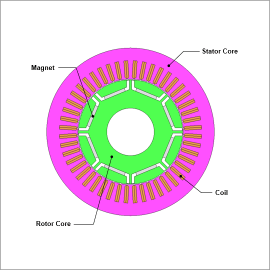
Simulations that use temperature-dependent efficiency maps account for the interaction between the magnetic field and thermal characteristics to create efficiency maps during continuous operation. Users can configure a thermal circuit in JMAG to create a cooling model using a wide range of components, including cooling jackets and hollow shaft cooling combined with spray cooling to account for temperature variations due to cooling.
This case study runs an analysis of an IPM motor in a continuous drive mode to create an efficiency map that limits part temperatures.
Analysis Flow
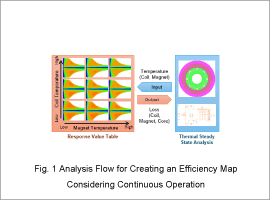
The magnetic field analysis study (efficiency map analysis) generates multiple efficiency maps that include the loss data according to the temperatures of both the coils and magnets.
The thermal analysis study (continuous drive characteristic analysis) positions operating points based on the efficiency map generated by the magnetic field analysis (efficiency map analysis) and runs a steady-state thermal analysis for only those operating points. An iterative calculation of the transient thermal analysis at each operating point integrates the temperature dependency of heat sources in the parts used in the magnetic field analysis (efficiency map analysis) and temperatures at a steady-state. This process obtains an efficiency map that includes current, loss and other characteristics during continuous operation. Temperature constraint settings for the efficiency maps prevent the temperature at operating points from exceeding the temperature limit to obtain N-T characteristics and efficiency maps that account for the continuous drive characteristics under these constraints.
Continuous Drive Characteristics
Fig. 3.2 presents N-T curves during intermittent operation with part temperatures at 60 deg C and during continuous operation at the temperature limit (coil temperature limit: 140 deg C; magnet temperature limit: 180 deg C). Fig. 3 provides the efficiency maps. The cooling flow rate during continuous operation is 2 L/min.
As the N-T curves show in Fig. 2, the continuous drive torque is lower due to the upper temperature limits and because the torque decreases as the magnet temperature rises.
As the efficiency maps show in Fig. 3, the maximum efficiency during continuous operation decreases about 0.6 points compared to intermittent operation.
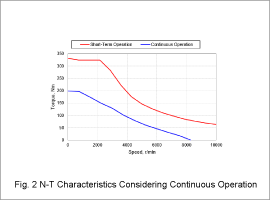
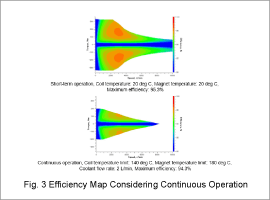
Influence of Coolant Flow Rate on Continuous Drive Characteristics
This case study creates two different efficiency maps during continuous operation. One has a coolant flow rate of 0.5 L/min and the other 10.0 L/min. Fig. 4 presents efficiency maps with a temperature limit for the coil and magnet. Fig. 5 provides an efficiency map based on the coil temperature. Fig. 6 provides efficiency maps based on the copper losses of the coil.
As illustrated by Fig. 4, the continuous drive torque increases alongside the coolant flow rate due to better motor cooling performance. The torque decreases with the low coolant flow rate (0.5 L/min) in a very low-speed region because of reduced shaft cooling performance due to the slow rotation speed.
Better cooling performance mitigates coil heat when comparing temperatures at the same operating points in Fig. 5. Heat in the coils at the outer operating points not affected by the coolant flow rate approach the upper temperature limit in the N-T curves. Therefore, regions with a larger coolant flow rate have better cooling performance and reduce heat to mitigate temperatures at this upper limit.
The efficiency map in Fig. 6 shows that some operating points have larger copper losses with a high coolant flow rate (10 L/min) than a low coolant flow rate (0.5 L/min). However, the better cooling performance enables the motor to mitigate heat generation even at the operating points in the coil that have larger copper losses.
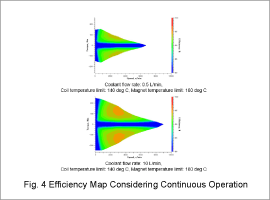
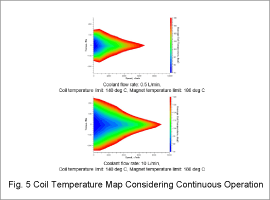
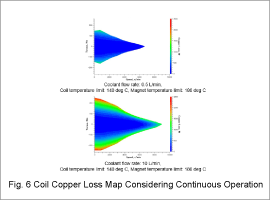