Providing customers with all new devices. Better products, faster service. Understanding the process one step at a time. New challenges with JMAG.
Dai-ichi Kiden develops various devices using high temperature heating technology. The company is an expert when it comes to the manipulation of heat, and is occupied in various industrial furnaces and hot stamping equipment, with a focus on crystal growth equipment (for producing silicon for solar panels in addition to SiC for power devices, and so on).
Providing customers with all new devices. Better products, faster service.
Our work here at the New Business Propulsion Department involves devising, investigating, and developing new materials and devices. The NBPD and a sales team will work together to investigate customers’ needs and devices that customers will find themselves seeking out in the future, looking into the possibility of pioneering themes with the potential of being newly commercialized. Occasionally we will even receive requests from customers about the kind of devices that they’d like to make, where we also look into the feasibility of those requests using electromagnetic and thermal theoretical calculations and simulations.
As a company, we originally started out manufacturing devices for power supplies, which is power supplies related to heating, in other words heat sources such as induction heating, electrical heating, and resistance heating as core technologies. The development and sales of devices using those elements became our main line of business.
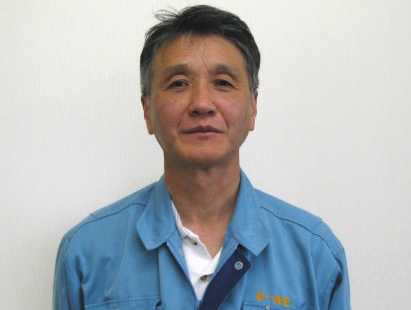
Mr. harumasa Ito
director and general manager,
New Business Propulsion Department,
Dai-ichi Kiden Co.,Ltd.
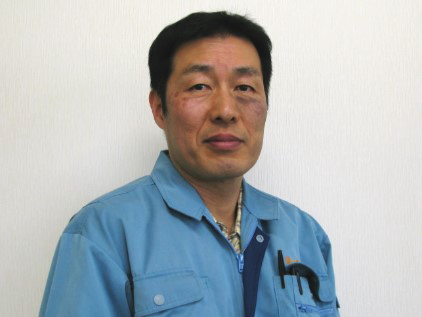
Mr. Tomohiro Adachi
Group Leader,
Process Tecnology Group,
New Business Propulsion Department,
Dai-ichi Kiden Co.,Ltd.
The concept behind the compact hot stamping system was that of a product that is both compact and reasonably priced. Hot stamping equipment used for mass production can be both costly and large in size. It was for this reason that those in R&D, and elsewhere, found the need for the same equipment to be available in a smaller and more affordable format so that our customers could trial various types of heating themselves.
One feature of our company’s compact hot stamping systems is the incorporation of high-frequency heating technology. While there are some large-scale models that require power measuring at some hundreds of kilowatts to run, I’m not aware of many companies that incorporate any high-frequency induction heating for small-scale models. Our system only requires a range between 20 and 30 kilowatts to run, taking advantage of the quick response time that high-frequency induction heating possesses, realizing both rapid and local heating.
Our research and development finished up in March 2019. We hope that many customers will be interested in what we have to offer.
Mr. Ito:
We were actually in possession of some other software for magnetic field analysis prior to involving JMAG in development. Because it was unable to make any links with heat, however, we found ourselves unable to confirm any kind of heat distribution. It was for that reason that we decided to outsource the simulation of heat distribution to other companies. This would prove to be somewhat time consuming, leading us to the idea of introducing software directly into the company ourselves. The purpose of our simulations consisted of three main points. The first was the investigation of induction heating for irregular geometries with the exception of cylinders and columns. Second was confirming temperature distribution using induction heating, and third was eliminating design errors in matching sections. We received several software proposals, and I recall deciding to go with JMAG as a solution because of the ability to confirm temperature distributions well within our budget.
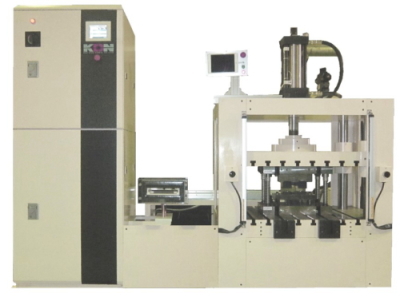
Effective communication through the visualization of various phenomena.
Mr. Adachi:
I think it’s easier for customers to make decisions now.
Mr. Ito:
A customer, for example, may present to us any number options. And when this happens, it is now possible for customers to make a decision after confirming to what extent temperature actually rises, and what kind of temperature distribution that will result in. I’m also under the impression that customers will always perform simulations before ordering any equipment. In that way, you could say that it’s been a very useful sales tool for us all.
Mr. Adachi:
Customers working with heating are very concerned with temperature distribution, after all. Whether you want to add gradients or make everything uniform will vary depending on the applications involved, and it is particularly important that elements slightly more difficult to predict, such as irregular shapes, are simulated.
Mr. Ito:
There’s been a reduction in the amount of working hours as well. We had always been outsourcing simulations until the introduction of JMAG directly within the company, meaning that preparing all the necessary materials for any decision would take a considerable amount of time. We can respond to customer requests much quicker now that simulations can be done directly in-house. There’s been a dramatic change in work speed, certainly.
Mr. Ito:
We have indeed had many customers requesting both experiments and simulations, yes.
Mr. Adachi:
We’ve certainly had those who have asked for simulations to be run in accordance with the experiments. Being able to measure temperature in detail can be rather difficult in that the heating that our company handles can reach extremely high temperatures. We now have even more customers who have expressed their interest in seeing the approximate states of experiments as well as the ability to confirm various details with simulations.
Mr. Ito:
I do think that we’ve been able to rather match the results of both experiments and simulations, which customers have greatly appreciated.
Mr. Adachi:
Although it can be difficult matching a temperature’s absolute value, you can understand a number of tendencies such as the extent to which uneven temperatures are likely to occur, which areas are having difficulty in being heated up, and where all the highest temperatures are happening. These are the kind of things that I think customers are rating fairly highly.
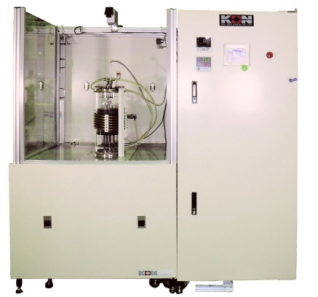
Multi-stage carbon ring induction heating simulation

Carbon rings layered in multiple stages
Simulation results 1
With two stages, we were able to look for conditions that could suppress temperature bias by positioning cylindrical coils both inside and outside.
When heating just the one side, either inside or outside, deviations will occur where temperature nearer to the coils is high, whereas temperatures further away from the coil are low.
Rotational symmetry 36-division model
Simulation results 2
We have the upper and lower stages as dummies, and coils are positioned to both the inside and the outside. These coils have an hourglass shape and a drum shape respectively, and we understand that temperature deviations are suppressed by induction heating on either side.
The main point here is the suppression of these temperature deviations, and there is a multitude of parameters present in order to do so, meaning that being able to narrow these down in simulations can be rather effective.
Rotational symmetry 36-division model
Understanding the process one step at a time. Making one continuous effort with the assistance of seminars and technical documents.
Mr. Adachi:
Needless to say, I didn’t know how to use it at all. Obviously feeling a need to do so, I first attended a seminar. That’s where I first learned about the general procedure involved, gradually gaining a knowledge of the thing while operating it myself. There’s also plenty of supporting documentation available, so I think a proper use of those can contribute to your learning as well. It was after I’d come to know the general procedure that I then began using JMAG myself, little by little.
Mr. Ito:
I seem to remember him learning to master JMAG rather quickly. He was certainly able to use it to some extent after attending the seminar.
Mr. Adachi:
It was the introductory seminar that I went to first of all. It covered an understanding of the analysis flow through a use of case studies, and the entire thing took around half a day. A number of things that I wanted to try myself kind of built up as I learned how to use JMAG more and more, and I wanted to further polish my skills as well, so I also started attending a few skill-up seminars.
Mr. Adachi:
Incorporating the temperature dependency of magnetic materials wasn’t the easiest part of the journey. I’d not dealt much with iron up until that point, so I went ahead using materials data as is without giving too much thought as to the kind of characteristics that iron would necessarily exhibit. As I’d only entered the BH curve, temperature kept on rising with no fall in magnetism. Heat continued to rise despite passing the Curie point. I realized that there was something wrong and tried to find what was causing it.
Mr. Ito:
The temperature didn’t rise in the actual experiment, of course.
Mr. Adachi:
I looked into how to incorporate the Curie point afterwards, and was later able to successfully add temperature dependence. It was only when I took a look at the application notes that I found the content concerning temperature dependency graphs, which is when I realized that I could do the same thing.
Mr. Adachi:
Understanding the analysis flow, certainly. I feel that it’s very useful being able to see the content of settings and the very basis of all the values. When I find myself wondering if there’s something that might be possible in JMAG, it’s the application notes that I check to see if there’s any such information already in there. And then when I find such information, that’s when I’m excited to try it out for myself. It provides a real opportunity to try out all kinds of new challenges.
New challenges with JMAG.
Mr. Adachi:
I’d like to maybe request accelerations to thermal analysis and usability.
I’m aware that progress has been made in making magnetic field analysis gradually faster and faster, but just a little more speed added to thermal analyses would be very much appreciated. Calculations handling emissivity takes a particularly large amount of time. Us dealing with such high temperatures means that emissivity is an absolutely vital part of our work. It would be a great help to me to know that the issue of emissivity could also be dealt with within a certain timeframe.
In terms of usability, I’m able to master things that I’ve already done once before without any real difficulty, but when it comes to something entirely new, I find myself struggling with configuring the settings now and then. There might be some descriptions provided in the application notes, but there might not necessarily be any clear link to any particular condition panel, meaning that I have to look for it while operating JMAG myself. It’s still possible for me to do these things even in the absence of any clear link, but if there’s a better relation between the technical documents and the actual software, then I can expect that I might end up saving just a little more time.
Mr. Ito:
There was some talk surrounding whether or not simulations for work involving movement might be possible. I was thinking, for example, of an application where I might want to raise temperature on a surface while an iron cylinder 1m in diameter and 2m in length is in constant rotation. This is essentially where the coil is fixed and the heated parts are the ones that are rotating.
Mr. Adachi:
I found some similar examples while looking over the application notes, so there’s plans for us to try out something like this in the future. We’d then be looking at eliminating design errors in the matching sections, which was again, one of our initial objectives in introducing JMAG in the first place. We’re yet to fully realize this, however, and are currently looking into calculation methods. Resistance values are necessary here for deciding on the specifications of the transformer of the matching sections, and those values aren’t entirely correct at the moment, which is why we’d like calculation methods established in particular.
Mr. Ito and Mr. Adachi, I’d like to thank you very much for joining me in this interview.
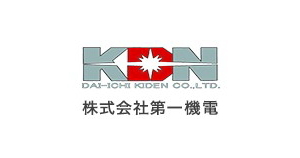
Crystal growth equipment, high-temperature heating equipment, high-frequency power supplies, the manufacturing and sales of industrial furnaces
Related Documents
You need to sign in as a Regular JMAG Software User (paid user) or JMAG WEB MEMBER (free membership).
By registering as a JMAG WEB MEMBER, you can browse technical materials and other member-only contents for free.
If you are not registered, click the “Create an Account” button.
Create an Account Sign in