Interview of technical experts working on developing the traction system (eAxle) for BEVs (Battery Electric Vehicle)
DEVELOPING EACH OTHER’S SKILLS THROUGH INTERACTION BETWEEN DEPARTMENTS
Mr. Yamashita:
I’m Yamashita of the Scientific Analysis Engineering Department. I’m working on developing analysis technology for powertrain motors and sensors. I‘m particularly focused on standardizing magnetic field analysis for the powertrain. Since anyone can use analysis and obtain results easily without understanding the condition settings, my objective is to get people to obtain the same results based on an understanding of the analysis conditions.
Mr. Sugiura:
I’m Sugiura of the PT Motor Engineering Department. I work on electromagnetic design for EV vehicle motors and run magnetic field analysis every day to create designs. I’m also working with Yamashita on developing a standard for in-house magnetic field analysis, which he just explained.
Ms. Sawada:
I’m Sawada of the EV Advanced Development Department I, of the EV Promotion Center. I’m working on developing the next-generation motor for eAxle. These motors will come out on the market after the currently announced motors, so we are making considerations for carbon neutrality and exploring new methods.
Mr. Sugiura:
The PT Motor Engineering Department, is in charge of projects for mass-production vehicles. We have to meet customer demands and maintain quality. Our mission, or rather, what we are conscious of, is to work together with the customer and to work fast.
The people in the electromagnetic design unit I belong to are relatively young, and the younger members of the unit engage the mid-level designers and experts in their daily work in an attempt to achieve a high level of perfection for their designs. I joined the company in 2014, so I am a mid-level employee, but I have little experience with JMAG because I started using it only after moving to this department in 2018. When I first joined the company, I was working on non-motor design, but I had been studying motors as a university student, and still wanted to be involved with motors, so I requested to be transferred.
My wish to work on motor design came true, but now that I’m actually working on it, I’m finding it difficult. My research at university focused on measurement, such as establishing evaluation methods using actual equipment and acquiring basic data, rather than creating designs using magnetic field analysis. Motor design involves watching out for many details and I really feel it is extremely difficult to clear all these issues and achieve a design that works.
Mr. Yamashita:
My team basically works on the development of motor analysis technology for the powertrain. Most of our work is on performance evaluation, but we also work on subjects in technology development such as strength analysis and the effects of miniaturization on magnetic fields.
I joined the company in 2014, the same as Sugiura. My experience with JMAG is also pretty much the same,. It’s only been about 4 or 5 years since I first started using JMAG. I used to specialize in NV (noise/vibration) related mechanical systems and worked on NV reduction technology, etc.
Most of the people on the team are young and quite friendly. We all have expertise in different areas and try to achieve even better analysis technology by putting together our knowledge and experience.
Our current focus is on optimization. The difficult thing about motors is that there are so many design variables, so we are working on improving analysis technology, by figuring out how to best aggregate these variables for optimization and what kind of processing should be used to achieve results. I believe that product quality cannot be improved without developing design technology, and that analysis tools should be used as more than just a tool, so I keep this in mind as a rule.
I have high expectations for JMAG when it comes to optimization. I believe that current designs rely on past knowledge and the introduction of new optimization technology will lead to new motor designs.
Ms. Sawada:
As announced in the press, the EV Promotion Center was established only recently, and since we are focusing on BEVs (battery electric vehicles), many people from various fields, not just eAxle, have gathered to form one department. I am in charge of motors for eAxle, and in relation to the environment, we are now developing motors with the proposition of improving efficiency and lowering electricity consumption in vehicles, as well as solving the issue of installation space by downsizing and cost reduction. In order not to be outdone by new companies entering the market, every day I try to think out of the box and rethink designs from scratch, thoroughly looking through anything that may be unproductive or ineffective in search of hints for new technology.
Of course, PM motors are currently the best performing and most efficient motors. However, we must be able to propose something even if, for example, the price of magnets rises significantly in the next 10 years and we are unable to sell motors at the current price. This is because selecting the most appropriate motor in response to resource issues, magnet procurement risks, and price hikes, and providing it to our customers is what is most important. Therefore, we are expanding into areas beyond our mainstream motors to be able to focus our efforts in all directions.
Mr. Yamashita:
Sawada, Sugiura, and I are connected by the keyword “Harmonics superposition control technology”. We have been working with control engineers on developing technology to reduce motor noise. Sawada plays the role of taking this technology on to the next generation of engineers. There is a lot of activity going on and we have meetings every week.
Ms. Sawada:
I joined Aisin Corporation in 2009 and was seconded to Aisin AW in 2018, but I have more experience than Yamashita and we got acquainted when he asked me something he couldn’t figure out. We’ve been communicating often ever since then.
INTRODUCING NEW TECHNOLOGY USING JMAG FOR DEVELOPMENT OF NEXT-GENERATION DRIVE UNIT eAxle
Mr. Yamashita:
We used JMAG for noise control when developing the unit in the new EV “bZ4X” released in May 2022. At the time, there was a movement to include new technology in the project, and we decided to incorporate harmonic superposition control technology. Simply put, this technology cancels out the component of torque fluctuation with torque fluctuation in the opposite phase, but there is a risk that a slight mistake could result in resonance in the same phase, which would make the vibration worse. We used JMAG to make sure such contradictions are accounted for. JMAG’s torque analysis is highly accurate, and we were able to verify that the amount of torque ripple reduction correlated fairly well with the actual noise. I think we were able to apply this technology because of JMAG. Highly accurate torque prediction was very important and we were able to ask questions such as, “Will this technology really be effective when there are variations of shape and assembly? or “Will the noise control be maintained for all car models when thousands or tens of thousands of cars are manufactured?
Mr. Yamashita:
Yes, there is an in-house developed current generation tool that we used with JMAG. We hear that JMAG-RT can be used to generate currents and would like to consider using it.
Mr. Yamashita:
Yes. Since the design period includes accounting for harmonic superposition control, we definitely want to use JMAG-RT to save time in the future.
Ms. Sawada:
Ideally, I would like to shorten the vibration analysis to within a week, but I know this would be difficult…
To achieve this, we want to reduce the amount of time people spend working on it. The extreme result would be to have the process finished while we are asleep. If shape optimization is included in the process, the ideal situation would be one in which all we have to do is press the “Run” button in JMAG to get an answer.
Ms. Sawada:
Each part, not only the motor has a standard. For example, in motor vibration, it all depends on what part of the motor is vibrating. Now that engines are not used, a car has fewer parts that make noise. The only electrification parts that make noise are the inverter and motor, and also the mechanical parts. Strict standards are given to these parts because the sound is clearly audible.
The disturbing noise when the car starts running at low speed is most likely the motor, and the constant high-frequency sound is probably the inverter. If EVs become even more popular in the future, I think people will get used to these sounds and this will become the norm, but there are still many drivers who drive cars with engines, so the high-frequency sounds of motor systems are still considered to be disturbing. I think more and more vibration reduction technologies in addition to the ones we are working on now should be developed.
Mr. Yamashita:
No, each customer has their own standard. Specifications for noise are set as a standard for gears, motors, and inverters according to requirements by the customer.
Mr. Sawada:
I think the specifications are set according to how much sound is allowed to be emitted as a car. For a luxury car, the standard may be more stringent, and it varies from customer to customer and from car model to model.
The technology we developed this time can basically reduce the sound of any motor, and that was one of the concepts for development.
Mr. Yamashita:
Although the technology is general-purpose, the time it takes to create a design is too long, and the three of us are working on that now. For example, to shorten the design period, we want to find ideas like automating the process using JMAG’s scripting and optimization functions, or performing optimization calculations that include parameters such as current and frequency in addition to geometry.
Mr. Yamashita:
I believe accuracy is expected the most for efficiency and loss.
Ms. Sawada:
As the accuracy of motor loss analysis is improved, it will eventually become necessary to run in-depth analysis such as to figure out which losses need to be lowered. When a certain motor is analyzed, it becomes very clear which loss ratio is large. I think that developing low iron loss materials is one way to address this issue, and it is necessary to continue to feed this information back to JMAG for further analysis. I believe the decomposition accuracy for hysteresis loss and eddy current loss will also become important.
Furthermore, it is necessary to accurately capture the losses exactly the same as the actual machine. With regard to motor losses, we have to rely on CAE to see the breakdown due to complexities with the measurement environment. This becomes important in thermal analysis. Losses occur for each part and heat generation analysis will not work unless each part is separately analyzed. We want CAE to handle this. Then all we need to do is to figure out the balance of the calculation time and accuracy.
eAxle is a high power performance, miniaturized drive that contributes to improving electricity consumption
eAxle is an electric drive module of a motor, inverter and transaxle all combined into one.
UNDERSTANDING THE PHENOMENA IS IMPORTANT. MAKING USE OF JMAG TO GAIN KNOWLEDGE
Mr. Yamashita:
Everyone in my team uses JMAG.
Mr. Sugiura:
My team is divided into two, thermal and magnetic analysis and everyone in the magnetic analysis team uses JMAG.
Mr. Yamashita:
More than 100 people in the company use JMAG. Many people working on sensors and actuators also use JMAG.
Ms. Sawada:
Not many people in the department I belong to have extensive experience running magnetic field analysis for motors, but there are an increasing number of people who have started to use JMAG recently.
Ms. Sawada:
I’ve been using JMAG since I joined the company in 2009. I think that it has really become convenient. So many new functions have been added to the extent that I almost feel a generation gap.
Mr. Yamashita:
The way JMAG is used is an issue at our company. I think the majority of people install JMAG and use it in the same way as they have been using it from the beginning. We are aware of how to check new functions but this information is not shared and everyone is on their own. Many times we have asked our sales representative Mr. Miwa whether something can be done and he has answered that the function is already provided. I believe we need to share this information with everyone in our company. We’re able to stay updated on the relatively major functions that have been added but when it comes to the minor functions such as useful functions on the GUI, we can’t keep up.
Mr. Sugiura:
Just yesterday, I asked about functions for materials. I recall that residual flux density could not be set up before in the magnet settings, but found out that it is now possible.
Ms. Sawada:
I got excited, too when I saw that there were more items. I don’t remember these minor function changes and felt it is so much easier to use when I noticed. When you use it every day, you often repeat the same process and it’s hard to notice. I think it is really important to make an effort to look for such information.
Mr. Sugiura:
With regard to magnetic field analysis, work on our procedure manual has progressed to a level where people can use it, so we have them learn with it. I think everyone has been able to run an analysis up to a certain level, one that anyone can easily achieve. However, we need to establish a check method because the analysis will still provide answers, even if there is an error in the settings. Furthermore, I think it is difficult for first time users to examine the analysis results. I myself am still learning and together with the person I am training, examine JMAG’s contour plots, vector diagrams, and magnetic flux diagrams to figure out why such results were obtained. It’s more like the two of us are studying together instead of my giving instructions.
First, we have them look at the analysis with their superior. When they have made an assumption on why the results were obtained, we have established a flow for them to share information so they can report to a person with expertise or exchange opinions with our internal electromagnetic working group.
Ms. Sawada:
I think you need experience to be able to understand how to perceive the resulting phenomena. Anyone can see the phenomenon in JMAG, but I think there are some parts where you can’t really understand what is happening unless you see the phenomenon for yourself in the actual device. I’ve always thought it is important to actually see what you are working on. Therefore, I try to be involved as much as possible in figuring out how to perceive and evaluate the phenomenon. And I also want to develop an environment where the evaluation can be fed back to the analysis and repeated. Either way, a phenomenon can’t be seen, so all you can do is use your imagination, but I think it is important to compare the analysis with the actual phenomenon and repeat the process many times. It would be nice if you could actually see the flux lines.
Ms. Nagae:
I often see reports saying “certain losses were derived from the geometry, or was improved”, but the issue is why this occurred. I think we need to teach people to run a frequency analysis on the losses and look at the contour plot to analyze the change in magnetic flux. I want everyone to verify for themselves that they are able to obtain various results with JMAG functions and properly analyze them on their own.
It would be nice to have a validation window that can be used for analysis when the system is automated. If everything is automated, it will become more and more of a black box, but if we could also automate the verification of technical concepts, it would be much easier to make evaluations.
Ms. Yamashita:
We have a manual for every analysis type. There were hardly any up until last year and we made about 10 this year.
Mr. Sugiura:
When we didn’t have procedure manuals, we learned analysis on the job from experienced people in the same department.
We gathered all those involved in the electromagnetic working group to propose good methods, and obtained opinion from technology experts before putting it in a manual.
WITH A BROAD VIEW FOR THE FUTURE, USE JMAG FOR TRAINING AND NEW TECHNOLOGY DEVELOPMENT
Ms. Sawada:
My department is completely about advanced development, so there are many new people who have just started using JMAG. Regardless of what field of technology you have studied, anyone who is interested in motors is welcome. When it comes to doing something new, sometimes it’s better not to have fixed concepts, so I would like future engineers to come up with fresh ideas and get involved with a lot of different people.
Ms. Yamashita:
I think that students also have the environment to use JMAG, so students with JMAG experience are ready to work on design at our company. I think there is an advantage in being able to make use of the skills and experience accumulated with JMAG. It is a common tool regardless of the school a student has attended or the company a person works for.
Ms. Sawada:
Yes, I think so, too. JMAG is a common language. Since it is used by various companies, we can communicate using only the JMAG model, and the analysis accuracy is highly reliable. There are many people who have been using it since they were students, and we welcome such people because we can teach them about design later. Not only students but also people who worked for other companies and mid-career hires having JMAG experience are also welcome because there are many products that use JMAG and we are willing to adopt different perspectives.
Starting with the establishment of an EV promotion center that gathers a wide variety of human resources, the company is looking for a wide range of people to work on creating new products.
Mr. Nakagawa:
There are many functions, so the best thing is to make one model and get all the results. Not only torque and loss, but also heat, temperature, durability, and NV. Ideally, these calculations are completed after the required performance, electrical specifications, and external geometry are set as parameters.
Mr. Sugiura:
Simply put, designers hardly need to spend any time on modeling when using optimization technology. It eliminates the time for a designer to create models and run analysis. In design work, it is important not to accept all the results that are obtained, but to examine the logic of the results, or examine why it turned out a certain way, so I don’t think having optimization as a tool will solve everything.
Ms. Sawada:
What I expect from optimization is not the results we thought were good until now, but the other answers that were obtained. I think you get the impression that many motors from each company look the same, but I want to find a shape that has never been created before. I believe that optimization is a technology that extends beyond my own thoughts. Since I have a long history working with motor design, I often feel that there are fixed concepts that are a detriment to coming up with new ideas. I want to have technology that can break thought this wall.
Mr. Yamashita:
Yes, we would also like to have a joint development type of relationship where we work together to create new technology rather than just a user asking questions and a developer providing answers. It’s not something we usually do with software vendors, but if we allocate responsibilities and work together focusing on creating new technology, I think we would be able to get one step ahead of our competitors. It would be great if we could do that.
Interviewees
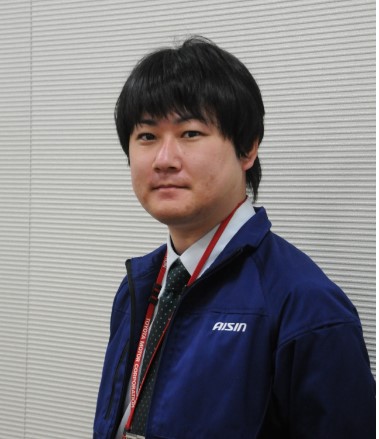
Assistant Project Manager
Group 2, Design Section 4, PT Motor Engineering Department
Powertrain Company
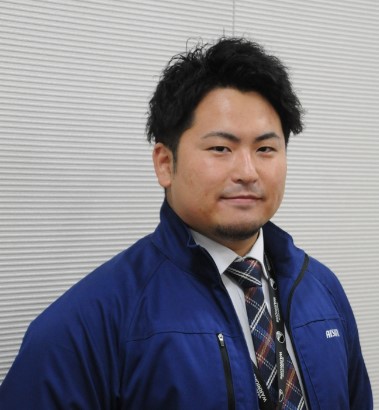
Assistant Project Manager
Electron/Magnetic Field Group, CAE Development Section
Scientific Analysis Engineering Department
Aisin-Group R&D Division
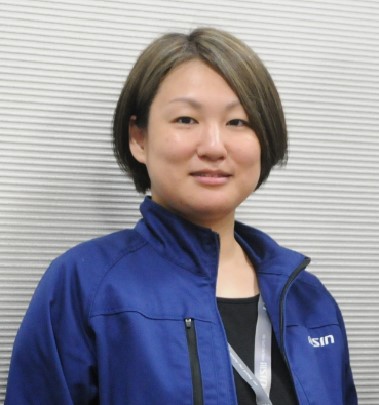
Assistant Project Manager
Motor Development Section Group 3
EV Advanced Development Department I
EV Promotion Center
(not pictured)
Mr. Yoshinari Nakagawa
Project General Manager
PT Motor Engineering Department
Powertrain Company
Mr. Tokihito Nagae
Group Manager
Electron/Magnetic Field Group, CAE Development Section
Scientific Analysis Engineering Department
Aisin-Group R&D Division

You need to sign in as a Regular JMAG Software User (paid user) or JMAG WEB MEMBER (free membership).
By registering as a JMAG WEB MEMBER, you can browse technical materials and other member-only contents for free.
If you are not registered, click the “Create an Account” button.
Create an Account Sign in
Recommended
- AISIN CORPORATION : Calculation Cost Reduction Method in Multi-Objective Optimization Using Machine Learning: Case Study on Actuator Development , JMAG Users Conference Proceedings , 2021
- AISIN SEIKI CO.,LTD : JMAG & GT-SUITE Link for EV Traction Motor 1D Thermal Analysis , JMAG Users Conference Proceedings , 2020
- AISIN SEIKI CO.,LTD : FET Switching Control of PAM Inverter Circuit and Motor Characteristics Optimization of PWM Inverter Circuit , JMAG Users Conference Proceedings , 2019
- AISIN SEIKI CO.,LTD : A Temperature Prediction Technique of Motors by the Combination Between Harmonic Loss Simulation by JMAG-Designer and Thermal Simulation by FloTHERM. , JMAG Users Conference Proceedings, 2018
- AISIN SEIKI CO.,LTD : Cooperation analysis of optimization and quality engineering by modeFRONTIER and JMAG , JMAG Users Conference Proceedings , 2016
- AISIN AW Co.,LTD. : Multi-objective optimization with wide-range shape parametric design space for IPM motor , JMAG Users Conference Proceedings , 2014
- AISIN SEIKI Co.,Ltd. : Introduction to magnetic field design support system using JMAG , JMAG Users Conference Proceedings , 2014
- AISIN AW Co.,LTD. : Magnet temperature analysis and prototype verification in permanent magnet synchronous motor , JMAG Users Conference Proceedings , 2013
- AISIN SEIKI CO.,LTD : Electromagnetic Field Analysis for Smart Key Antenna , JMAG Users Conference Proceedings , 2010