A power distribution equipment manufacturer committed to establishing stable power supply and creating a comfortable living environment. A company that manufactures highly reliable products in response to customer and social demand.
San-Eisha Ltd. provides technologies and products to ensure a safe and stable supply of electric power. This has earned the company high credibility for contributing to society by proactively addressing environmental issues such as energy conservation.
In this interview, we talk with the people who are working on product development to ensure the delivery of a stable electric power supply.
FOCUS ON DEVELOPING RELIABLE PRODUCTS
Mr. Mitsuya:
I am working on the design, manufacturing, and sales of power distribution equipment. As indicated in the President’s message on our Website, the company has strived to contribute to society in line with the corporate mission to “Put our customers first” and “Create reliable products”. We want to continue to respond to the demands of customers and society in the energy industry and the entire team is working together to develop products that are necessary in providing a stable power supply.
Mr. Hasegawa:
The life cycle of the products we develop is extremely long, so long our products are commonly used for about 20 years. Some products are used for 30 or 40 years. We are always conscious of whether there may be problems with such products being used over a long period of time.
Mr. Hasegawa:
In that sense, our products may be quite different from commonly used household electric appliances. Once installed, no maintenance is provided. The solenoid is expected to continue operating without maintenance for 20 or 30 years.
Mr. Mitsuya:
Right now, we have not been able to go that far even using analysis. We hope that in the future we will be able to analyze details such as the impact and resistance when the switchgear is in operation.
In terms of using analysis, it depends on whether we can identify a solenoid structure that can provide sufficient pull force to accurately operate the opening and closing mechanism of the contacts inside the switchgear. This has enabled us to reduce the number of prototypes.
Mr. Hasegawa:
In terms of the life of the equipment, analysis is used on the solenoid, in other words, we analyze some elements of the product. So, as Mitsuya said, the emphasis is on the fact that the equipment will work without problems and without fail.
Mr. Hasegawa:
Yes. Having too many rules is not good. Our focus is on creating a product that will operate no matter what.
Mr. Hasegawa:
There are currently 22, of which 2, Mitsuya and Takahashi are the ones mainly working on analysis.
Mr. Mitsuya:
The basic workflow is for other members of the department to request the characteristics they want to use in specific situations and we look into it by running an analysis, to figure out what kind of structure is necessary to bring out such characteristics.
Mr. Akutsu:
We have a manufacturing plant in Tochigi where we ran electromagnetic field analysis on solenoids using other company analysis software. But, there were only a few people who could use the software, so we only used it from time to time and were not always running an analysis before creating a product. The know-how for using the software was never passed on to others. Later, when solenoid design was moved to Tokyo, the maintenance contract on that software had expired, so we discussed ways to improve efficiency, researched several analysis software, and decided to introduce JMAG around 2015.
Mr. Akutsu:
The main reason is because of JMAG’s Japanese user interface and support. Being managed totally in Japan was a significant factor. The software that we had been using back then was difficult to use, so software that is easy to use was also important. At first, we didn’t use JMAG too often, we started with evaluating static analysis. We also saw the possibility of expanding use in the future because we were told that 3D models and transient analysis could be added and decided to introduce JMAG.
JMAG TECHNOLOGY TO UNRAVEL THE MECHANISM OF PHYSICAL PHENOMENA
Mr. Mitsuya:
The first solenoids were cylindrical, so we used a 2D axisymmetric analysis to determine the pull force of the plunger at each position and check if the desired value was obtained. We were using JMAG in the same way that we used the first analysis software.
Nowadays, we run 3D analyses for products with structures in which axisymmetric analysis cannot be used. In addition, we evaluate not only pull force characteristics but also transient characteristics. We check to see the changes in transient response over time. We also run circuit analyses. We set conditions for the circuit and evaluate response characteristics.
We have started to study the structure and plan to incorporate it into the new switchgear.
Mr. Akutsu:
We used analysis mainly for cylindrical shapes. However, when we began to handle different shapes, we were concerned that there was no numerical data to technically explain the results. If the physical phenomenon is accurately analyzed, we would know why the results occurred and can figure out how to fix it. This is where Mitsuya and Takahashi put their heads together to figure out a way to analyze physical phenomena.
Mr. Akutsu:
The product is somewhat unique, having a laminated structure, so we have just begun to understand how to go about analyzing it.
Mr. Mitsuya:
I think we are still missing something but we have a general idea of how to run the analysis.
Mr. Akutsu:
Smaller products use less material and the products that Takahashi’s group handles require many parts to be placed in a small box. With this in mind, it is definitely a design advantage for the product to be small and low in height. We are talking about running more analyses to make the products smaller.
Mr. Mitsuya:
I haven’t gotten to the point of comparing what characteristics are actually produced, but the responsiveness of the plunger may be good because we know the pull force is strong. The idea is a plunger that is easy to operate and easy to stop.
Mr. Akutsu:
Unfortunately, although the solenoid delivers a large amount of force, making it smaller has made the strokes shorter.
Mr. Mitsuya:
Only short strokes are taken into consideration.
Mr. Akutsu:
The mechanism we are designing assumes relatively long strokes, therefore, the short strokes in smaller machines remain an issue.
Mr. Mitsuya:
Specifications require the pull force to be interrupted within a certain number of seconds. If this can be confirmed, the time and effort required in prototyping can be eliminated. I believe this is where analysis truly becomes useful. Specifications for the type of circuits used in control are predetermined, therefore, we can analyze circuits that meet certain conditions and see what kind of current actually flows through them. The maximum current value is also pre-determined and it is extremely helpful to be able to analyze the state of such circuits.
Mr. Takahashi:
The work I do is pretty much the same. Although we work in different groups, the solenoids that are actually operated are the same as well as the content of the analysis.
THE MANY ISSUES TO DEAL WITH IN THE FUTURE
Mr. Mitsuya:
As I just explained, if you would look at Fig.1 below, we often examine how parameters affect the analysis, such as how much the pull force changes when the number of windings is changed in relation to the original structure. While conducting such studies, the newly introduced transient response analysis with circuit settings is also used to check how the pull force characteristics change over time before prototyping.
As shown here (see Fig. 2 below), the circuit is a full-wave rectifier that takes power from an AC power source and rectifies it. This type of circuit is used inside the switchgear and may be used for simple full-wave rectification or with a capacitor placed inside bringing it closer to the direct current. We check in advance, what characteristics each of these circuits produces.
Fig. 1: Cylindrical solenoid
Fig.2: Full wave rectification (voltage)
Fig. 3: Cylindrical solenoid (actual machine)
(Fig.1-Fig.2) Source: Excerpt from JMAG Users Conference Proceedings
Toshihisa Akutsu “ Challenges Moving from Static to Dynamic Analyses, The Merits of Introducing Transient Response Analysis ” (JMAG Users Conference, 2019)
(Fig.3) Photographed at Tokyo Head Office
Mr. Mitsuya:
Yes, that’s right. I would like to try to work on that.
We have tried dealing with eddy currents because they are easy to set up, but it isn’t working out because it is difficult to take measurements and that makes it difficult to make comparisons. Since we use laminated steel plates and I am thinking that we need to match the actual measured results to the simulation.
In terms of studying residual flux, there are cases where the plunger must be held for a short period of time after the power is turned off, depending on the specification. So, in this aspect, I would like to work on the analysis of residual flux, but have not been able to do so yet.
Mr. Akutsu:
With regard to magnetization and residual flux, as it was just mentioned, there are two patterns, one is to hold the plunger for a while and the other is to quickly release it and you need to figure out which way to go.
Mr. Mitsuya:
There are cases where the power is suddenly turned off on the circuit, but there is still a delay in turning it off because it is actually magnetized. Currently, we are studying a case in which the power is suddenly turned off on the circuit and analyzing how to control the current on the circuit when it continues to flow after it is turned off using a diode. At this stage, we are analyzing the case in which the current continues to flow and are examining in advance whether the specifications can be satisfied as much as possible.
I also want to work on studying magnetization and study how long it takes for the magnetic flux to be cut off when the power is turned off all at once.
Mr. Mitsuya:
We currently use an in-house made jig to measure pull force. However, it can only measure one point at a time, so we can only compare the analysis results of each position. Last year Takahashi used a high-speed camera to see if we could compare the speed when force is actually being pulled. It is difficult to measure pull force when the solenoid is in actual operations, but we confirmed that the results were qualitatively correct.
Mr. Akutsu:
If you’re talking about developing a solenoid, it would take about 2 or 3 years. Maybe a little more than a year for a minor change. In both design and prototyping, there are times when we have to go back to the drawing board and if the time it takes to obtain client approval is included, it would take 2 to 3 years to design a new product.
JMAG A GREAT HELP IN REDUCING PROTOTYPES AND DELIVERY TIME
Mr. Akutsu:
We didn’t use it often at first, only to evaluate pull force with static analysis. In that sense, you could say that the start-up didn’t go well. Things started to roll when I started to consider specifications for transient analysis. With advice from JSOL, I started to think that it would work better if considerations were made to use transient and 3D analysis.
Mr. Mitsuya:
Yes. It was just when we wanted to try something new in development so we tried JMAG’s various functions. We ran an actual transient analysis and seeing the results we thought JMAG would be useful, so we introduced it.
Mr. Mitsuya:
The key point is pull force speed. We are working on developing equipment that requires a fast pulling force. Since the delivery time is short, we decided that it would be more efficient to make a prediction from a 2D transient analysis rather than making many prototypes to search for the right one. We were not able to obtain an accurate value but we were able to make a relative evaluation.
Mr. Mitsuya:
Yes. In static analysis, the current values that could be set were fixed but now we have a circuit set up that is used in actual equipment and are also able to see the time variation of transient response. So, it is great that we can see how the current changes and how fast the plunger can be pulled.
Mr. Mitsuya:
Back then we only had a few months’ time, so making two or three prototypes was the best we could do. But we were able to narrow down the number of design plans which I think was a great advantage.
Mr. Akutsu:
For example, it would be nice if we could say that we only needed to make two out of the 10 prototypes we had to create, but making a comparison is difficult. I believe the analysis helped to meet the schedule without dragging out the rest of the process. But this contributed to earning a high reputation in the company and made it easy to introduce.
Mr. Mitsuya:
If we look at the details, some of the analysis we ran back then may have been incorrect. We were trying to figure out how to use JMAG by referring to the Help function. The Help function is quite useful and I was able to operate the software on my own without understanding all the details. So, I created the settings with the closest possible conditions and managed to obtain results. I then narrowed down the results to about 3 patterns and made prototypes. The best prototype turned out to be the same as the results of the analysis.
Mr. Mitsuya:
For now, the Help function. If there is a term or function I don’t understand, I look it up and if I need more information, I will look at the related reference material. Takahashi, who joined us about a year ago is able to run an analysis pretty much on his own. Sometimes he even gives me information that I didn’t know about. I think the Help function is useful.
Mr. Takahashi:
I also relied on the Help function when I first started using JMAG. I sometimes check case studies to see if there is anyone else that is thinking the same way. But when I’m working on an analysis, I basically use the Help function.
Mr. Mitsuya:
We may be using the Help function more because there are fewer case studies on solenoids than motors right now.
REASSURANCE GAINED BY INFORMATION EXCHANGE WITH JMAG USERS
Mr. Mitsuya:
I participated in a seminar immediately after JMAG was introduced and didn’t use it much back then. I started to use JMAG more often when we introduced transient analysis two or three years ago. Even then we were not running analyses for everything, only for certain cases. We use JMAG almost every day for several weeks to a month or so when we are about to start prototyping. Since Takahashi joined our department, I have someone to consult with now and have a better understanding of setting details.
Mr. Takahashi:
I started using JMAG about a year ago. I started out with basically no knowledge at all and learned how to use JMAG starting with static analysis and going on to transient analysis. I’ve been with the company for five years now and before running analysis I was involved in designing various equipment.
Mr. Takahashi:
I never used electromagnetic analysis software. I have a little bit of experience using structural analysis software in college. I thought JMAG is easy to use, so I first asked Mr. Mitsuya to brief me on the flow of analysis and then figured out how to use it on my own through trial and error.
Mr. Mitsuya:
Back then, the first thing I did was to use the self-learning system. Now, we study on our own and exchange information when we don’t understand. I get a lot more done than when I was working alone. It helps to have another person to work with.
Mr. Takahashi:
Yes, working alone makes you feel anxious. I intend to participate in seminars if the subject seems interesting because there is still a lot about JMAG that I am not familiar with.
Mr. Akutsu:
Yes. We are working on important parts used in the product, so we would like to get people interested in JMAG and expand it from there. I want both Mitsuya and Takahashi to gain more knowledge and develop a basic framework including matching with the actual machine before we proceed with passing on the knowledge to other people.
Mr. Mitsuya:
It is all recorded or saved as individual data in JMAG. We are not ready to extend the knowledge on a company-wide scale yet.
Mr. Mitsuya:
We would like to develop a framework where we can save and expand the knowledge within the company, but we haven’t gotten around to it. The two of us working solely on analysis are now focused on maintaining stable and accurate analyses. To begin with, we are still consulting each other, trying to figure out whether a new analysis can be run or not. We would like to share our knowledge with others when we get to a stage where we feel the results are good, including the match-up with the actual figures.
Mr. Akutsu:
I know that findings should be accumulated but data transition on solenoids has not been working out and we are feeling our way around trying to figure out what to do. Mitsuya and Takahashi are actively engaged in analysis now, so we would like to proceed, keeping in mind to eventually accumulate data and expand it across the company.
Evaluation of the actual equipment is extremely difficult and we are constantly groping around for an answer.
Mr. Akutsu:
Yes, that’s right. We are still feeling our way around, so if we expand too early, it may mess things up. First, we need to organize data on solenoids, which is the current subject of analysis.
Mr. Mitsuya:
Until now, we have only accumulated previous knowledge and have not created a solenoid from scratch. What we did was make improvements to existing designs. With the introduction of JMAG, I think it would be good if we can theoretically analyze what we have been exploring and then theoretically summarize what needs to be changed in order to make improvements.
Mr. Mitsuya:
I think it would be best if we could visualize or quantify the physical phenomena so that people could share a common understanding that the design change was for the better because of certain changes.
From left, Equipment Development Department, Section Chief Mr. Akutsu,
Equipment Development No.2 Mr. Takahashi, Equipment Development No.1 Mr. Mitsuya
MATCHING ACTUAL MEASUREMENT TO IMPROVE ANALYSIS ACCURACY
Mr. Mitsuya:
Yes. We are looking for a way to take actual measurements, so making accurate measurements is an issue. In addition, there is a part with a spring that has to be pulled and that spring is not attached straight. It functions to control rotation movement and the difference in force depending on the angle has to be specified. That’s the hard part.
Mr. Akutsu:
The plunger does not move straight and sort of sways when moving in a linear direction. I tried to load the data in steps instead of putting the load on all at once but it didn’t work.
Mr. Mitsuya:
Right now, we can only evaluate the solenoid as a single unit, but the issue now is being able to run analyses on solenoids installed in equipment accounting for the load inside the equipment.
Mr. Mitsuya:
The solenoid itself pulls straight but there are various mechanisms combined to pull it and the load varies depending on the position.
Mr. Mitsuya:
Yes, we haven’t started anything yet but that’s exactly what we are thinking.
Mr. Takahashi:
We are currently conducting an analysis that includes the weight of the plunger as a load, so if we can include conditions that will change external force depending on the position of the plunger, it may be useful for other designs.
Mr. Takahashi:
Pretty much so. It depends on the conditions but 10% or 20% of the time it will not move straight.
Mr. Takahashi:
Yes, it is taken as a waveform but no actual measured waveform is input. It may be better to input the current value as it is.
Mr. Mitsuya:
If a current is specified, is the back EMF accounted for when it flows through the coil?
Mr. Mitsuya:
Is the effect of magnetic material getting on to the coil and causing the current to fall also accounted for?
If you have any further problems, please contact our support desk on a regular basis.
Interviewees
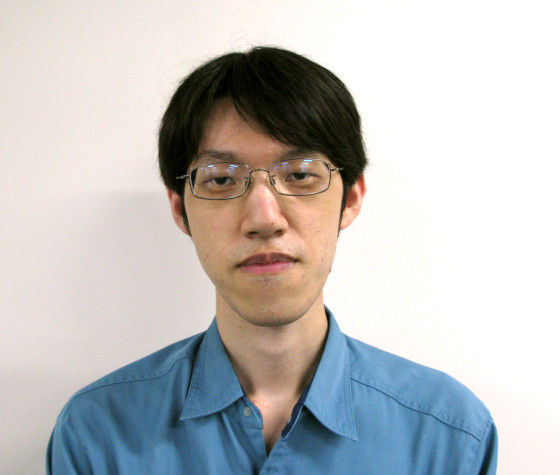
Equipment Development No.1 Group,
Technology Development HQ, Equipment Development Department
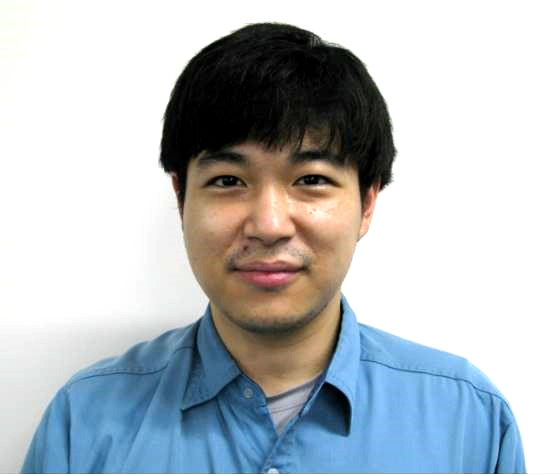
Equipment Development No.2 Group,
Technology Development HQ, Equipment Development Department
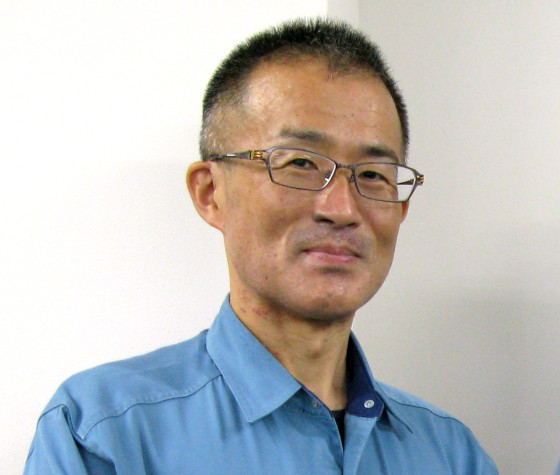
Section chief
Equipment Development No.2 Group,
Technology Development HQ, Equipment Development Department
(not pictured)
Kenichi Hasegawa
Manager
Technology Development HQ, Equipment Development Department
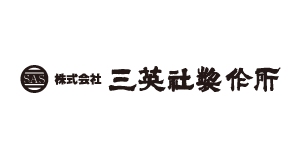
Design, manufacture and sales of power distribution equipment
- Overhead line equipment
- Underground line equipment
- Uninterruptible construction equipment
- Connection material and power fuses
- Distribution line automation equipment
- Measuring instruments for power distribution
- Power receiving equipment/special equipment
You need to sign in as a Regular JMAG Software User (paid user) or JMAG WEB MEMBER (free membership).
By registering as a JMAG WEB MEMBER, you can browse technical materials and other member-only contents for free.
If you are not registered, click the “Create an Account” button.
Create an Account Sign in
Recommended
- San-Eisha, Ltd. : Challenges Moving from Static to Dynamic Analyses: The Merits of Introducing Transient Response Analysis , JMAG Users Conference Proceedings , 2019
- PURPOSE CO.,LTD. : Analysis of Gas Proportional Solenoid Valve Using JMAG , JMAG Users Conference Proceedings , 2021
- AISIN CORPORATION : Calculation Cost Reduction Method in Multi-Objective Optimization Using Machine Learning: Case Study on Actuator Development , JMAG Users Conference Proceedings , 2021
- IWAKI CO., LTD. : The Influence of Material Hysteresis in Electromagnetic Pump Operation Analysis , JMAG Users Conference Proceedings, 2019
- CKD Corporation : Optimization of Solenoid Attraction using JMAG Optimization Function , JMAG Users Conference Proceedings , 2018
- IWAKI CO., LTD. : Predicting Electromagnetic Pump Operation Using a Simulink-JMAG Coupled Analysis , JMAG Users Conference Proceedings , 2017
- Wuxi Fuel Injection Equipment Research Institute,FAW, China : Optimization calculation of JMAG and its application in proportional solenoid valve , JMAG Users Conference Proceedings , 2015
- CKD Corporation : Analysis of responsiveness of air pressure solenoid valves using JMAG-Designer , JMAG Users Conference Proceedings , 2014
- Mitsubishi Electric Corp. : Magnetic field analysis of solenoid actuator using JMAG-Designer , JMAG Users Conference Proceedings , 2014