“Developing technology and selling technology”, based on this corporate philosophy, Tamagawa Seiki has grown with firm roots in the local community of its offices and production centers. Since their founding, they have disseminated their “sensors” and other unique technologies cultivated from the development of servo components from these communities to the world.
Tamagawa Seiki is celebrating its 85th anniversary in 2023. Their ongoing challenge to achieve higher accuracy in control equipment has led to the application of high-precision technology in their products in aeronautics as well as other areas of industry. Today, we talk to Senior Managing Director, Hideo Kumagai (Ph.D., in Electrical Engineering) who has been at the helm of their technology and development over the years, and the Engineering and Quality Management Department staff who specializes in analysis.
A company founded in hopes of developing local industry in the impoverished Iida region
Hideo Kumagai:
The current head office is located in Iida city in Nagano prefecture, the hometown of Tamagawa Seiki’s founder, Hiroichi Hagimoto. The founder was born in Yasuoka, a neighboring village, and went to the Aoyama Teachers College to fulfill his childhood ambition to become a school teacher. Back then, Iida and Shimoina region was an impoverished area with sericulture being the main source of income. Hagimoto was concerned and went back to college, this time to the current Tokyo Institute of Technology to study industrial engineering, and founded Tamagawa Seiki in 1938 in hopes of promoting industrialization for the future growth and prosperity of the region.
This founder’s belief for his hometown has been passed down to the present. In business, a change of location is often made while continuing to manufacture the same product, but we have declared that “we will not leave” the region where we started. We move forward by adopting new technologies while thinking about what we should do and what we should create, right here, where we are. Being a privately owned company, technology is an important asset. Our business style is to run the total process from development to manufacturing, quality assurance, and sales within our company.
Our main business is servo components, focusing on angle sensors that detect rotation, and motors. There are two types of angle sensors. The resolvers detect the angle of rotation around an axis and the gyros detect the angular velocity of rotation in space without an axis. Each manufacturing plant handles different products. The head office and the First Plant in Iida run the design and manufacturing of aviation, space, and defense products. The Second Plant also in Iida handles vehicle parts, and the Hachinohe Plant in Hachinohe, Aomori handles plant facility-related equipment. Even if the products are similar, the business method and costs depend on the user. The aviation and defense sector derives no sales growth being dictated by a budget but business is stable. Business in the automobile market is growing , particularly in products for EV’s and hybrid vehicles. In contrast, FA (factory automation) is a market with large swings. We manage to maintain a balance by combining business in these markets. We also have manufacturing plants in China and Vietnam since it has become increasingly more difficult to manufacture only in Japan, but our basic policy is to run technology development, the key to our business, in Iida, Nagano and in Aomori.
Hideo Kumagai:
To respond to “the need to develop technology”, we have a system in which new research is undertaken every year. We look closely at the current technology in each of our products to think about what the next-generation product should be like. We feel it is important to develop technology with careful consideration for “why the technology is needed” and “what customers want”.
Of course, our business is often customer-driven where we emphasize and work on development in response to customer needs. It’s a pattern that customers are pulling for us. We do not sell the final products. Our products are components that are used by customers to manufacture their finished products. This goes for all of our products in the aviation/space/defense, factory equipment, and transport vehicle markets. What is important for us is to reflect customer needs to be competitive in their business with their finished products. This is why we work on technology development from two perspectives: what we need to do and what the customer needs.
Hideo Kumagai:
Yes, the Engineering and Quality Management Department is responsible for a wide range of activities from design environment construction including design tools, regulation maintenance, sharing and managing technical information to patents, certification of standards, and quality control. They are an elite few. Among them, analysis is performed by a specialized analyst at the request of designers.
Our products are used in the five markets shown below. All of these components have been developed by accumulating advanced technology and provide reliability, high accuracy, high functionality and efficiency. Many analyses are run for these products at the request of the designers.
The five markets of Tamagawa Seiki
Good design brings profits and good technology creates new business
Hideo Kumagai:
When an interesting technology is found, everyone jumps at it because the corporate culture has always been the “pursuit of technology”, but recently we have been emphasizing “create good designs to gain profits”.
When you try something new, you end up dealing with a lot of defects and sacrificing profits. We shifted our attention to using our ideas not only in solving issues but in design. Focusing on design has resulted in profit gain and we now use these profits to “learn more and acquire more useful skills”.
This concept of gaining profit has spread and is acknowledged throughout the company. Everyone agrees to “use profits to enhance knowledge” and understands that new businesses cannot be developed without technology.
Hideo Kumagai:
We owe it all to Koji Kokue and his hard work.
In the beginning, we, including our engineering company, Tamagawa Techno Creation, created a 3D CAD system and started analysis. We created a workflow where everything went through the CAD system, even control devices for which CAD is not necessarily required. The wires and connectors for control devices that contain circuit boards were drawn up and represented in the 3D CAD exactly the way they actually are.
Kokue’s efforts paid off as we improved our skills and were able to make good use of analysis to the point of solving design problems. Since we set up a procedure it takes less time now and we’ve had fewer problems compared to when we were doing things manually. We test the heat and vibration, check if EMC is safe, and see what results we can obtain with electromagnetic field analysis. As a result, profits have gone up and since then we just analyze everything.
But that doesn’t mean all you have to do is analyze. It is still important to make sure that you clearly understand the results.
In the past, we once submitted the results of a structural analysis to a customer when designing aircraft components. The customer was furious and yelled at us “Is this all that Tamagawa Seiki can do?” The results we submitted were significantly different from the stress analysis run by the customer. So, we brought everyone involved to our company to study analysis until we were able to run a decent analysis the way we do now. Now, 3D CAD is linked to various types of analysis which is quite useful. We are currently working on the research and development of high power density motors with support from the Ministry of Economy, Trade and Industry (METI). We can run various analyses with the help of JMAG and unlike in the past, we can create designs without creating prototypes.
Koji Kokue:
I think that all the designers now try to explain the logical reason for all phenomena since we started running analysis. We are getting used to checking whether an actual product is made according to the design by measuring, observing, and pinpointing the cause if it isn’t. We also are more conscious about accurately understanding physical phenomena.
Hideo Kumagai:
Once when we were making a prototype for a special purpose motor, we were unable to gain any power and only ended up with heat. When I asked if an analysis was run, the answer was “no”, so I called for Kokue and asked him to run an analysis.
Koji Kokue:
Before I ran the analysis, I asked to see the measurement data and there was something strange about the waveform of the induced voltage. The waveforms were not ordinary considering that the induced voltage is the derivative of the magnetic flux passing through the stator teeth. I first doubted the measurement method because the waveforms were significantly different from the analysis results. The designer insisted that his results were based on actual measurements and had to be the correct value. If the analysis is different from the measured waveform, then the analysis must be wrong, he estimated. We then defined every possible error in the analysis model and ran the analysis over and over again. We found that when we added an error to the machining accuracy of the stator teeth, we were able to reproduce the exact abnormal induced voltage waveform. This error explained both the lack of expected torque when energized and the higher-than-expected cogging torque measured.
Hideo Kumagai:
This is a good example of the wonders of analysis. I later took the analysis results to the customer, explained it to them and they accepted the results. It all worked out well.
Koji Kokue:
We never forced our analysis results to match the actual measurements. We make sure we are always aware of the difference between “what we are solving with analysis” and “what we are trying to evaluate with analysis”. It is wrong to think that all analyses will match the actual measurements.
Koji Kokue:
I make a point of doing three things.
- Shorten the time it takes to report the results.
- Show correct results as a theoretical solution. Consider what kind of theoretical solutions can be obtained. Whether the trend is the same as the actual machine is the next step.
- Be aware of why the analysis is run. Running the analysis is not the objective, the analysis is a means to solve design issues.
Engineers who are dedicated to running analysis tend to make analysis their objective. I make sure to be aware that analysis is merely a means to solve the issues in design.
I am concerned that recently there are more and more designers that unconditionally believe the analysis results without a second thought. It is wrong to consider that analysis results are correct and unconditionally determine design parameters only from these results. Otherwise, it will cease to be a design of any sort. I tell designers who take analysis for granted that “it is sometimes important to anticipate the results rather than running the analysis”. If physical phenomena are correctly understood and the correct results are predicted based on design theory, analysis is not that important. Analysis is merely a tool to confirm your design theory, to make quantitative evaluations, and to provide explanations to others. In the past, it was difficult to get people to believe in analysis results, but now, it’s quite the opposite.
Vehicle mounted angle sensor (Singlsyn) History Hall (Exhibition)
Resolver analysis diagram
Finding answers with factor analysis
Koji Kokue:
We started using JMAG in 2006. There was little recognition for the finite element method back then and we had a tough time trying to get people to use JMAG because designers didn’t think analysis was reliable. At the time I didn’t know anything about motors or sensors and didn’t have enough knowledge to talk to the designers on an equal footing. So no one would even take a look at an analysis run by an amateur. I don’t think there were any designers who thought about how analysis could be used in design. When they saw me trying to get more people to use JMAG and achieve results, I was told that “no one expects anything from analysis”.
Obviously, in this environment, there were hardly any requests for analysis and I only had the opportunity to run three or four analyses a year. One of the reasons is that it took too much time to obtain analysis results. At the time it took about one month to obtain results after receiving a request.
Hideo Kumagai:
We had so many problems back then, that it was totally unprofitable. Running an analysis incurs costs, so there were always doubts within the company as to whether an analysis is worth the cost.
Koji Kokue:
The analysis that solved the issue of special purpose motors was a good opportunity for people to recognize that analysis is beneficial. I think this has helped people to acknowledge the importance of using analysis to obtain an accurate design calculation before creating a product and to check that a product performs as expected. Also, if the results are not according to expectations, there is always a cause. I believe the awareness among designers has changed to the point that they now realize that if analysis is used correctly, the cause can be identified.
Hideo Kumagai:
It’s been 17 years since we started using JMAG and I sincerely feel that being able to sell a product that has been created from accurate design is really a great achievement.
Koji Kokue:
Yes, there are quite a few.
A coreless finite angle motor did not produce the expected torque by a small margin, even though it was created based on analysis and proper design calculations. While discussing the cause with the designer, we found that the actual motor had magnet clamps that were not there when the analysis was run. These magnet clamps caused leakage of the magnetic flux and were the reason why the expected level of torque could not be obtained.
In another case, I was once consulted about a resolver which has a transformer to pass current to the rotor. When the engineers made a hole for the cable in the transformer core, the accuracy of detection was affected, they said. I didn’t think this size of a hole would affect the accuracy of detection in the sensor considering the magnetic density of the transformer and the distance between the sensor part and the transformer. I actually ran an analysis and could not see any influence, but the designers thought that the analysis was wrong because the actual machine detected the problem. The detection accuracy analysis of the resolver evaluates the slightest difference in magnetic flux and just trying to solve it with accuracy is a difficult task because a 3D magnetic flux leakage needs to be evaluated. However, I didn’t think the hole would affect the sensor. So I thought the parallelism of the sensor and transformer may have something to do with it. I ran the analysis with a parallelism error of a mere few μm in the analysis model and obtained the same results as the actual machine. This was also a really difficult analysis. I don’t think it could have been solved with a normal analysis. Later, we ran a confirmation test on the actual machine and confirmed that the cause of error was not the hole but the parallelism. It wasn’t the hole in the transformer but the parallelism caused by passing the cable through the hole that was affecting the accuracy of sensor detection. We then developed a countermeasure with the actual machine and this problem was also solved.
Koji Kokue:
It is important to think about the physical phenomena of what you are trying to evaluate because what you obtain from an analysis is only a theoretical solution to a mathematical model. These days when the analysis and actual machine show different trends, we suspect the possibility of something not anticipated in the design is occurring in the actual machine. I feel that this way of thinking has spread to the designers as well.
Thinking about ideal automation and the future
Hideo Kumagai:
We have just started learning how to use modeFRONTIER. We are testing to see how much we can use it. Resolvers are angle sensors with only a few parts, but we receive various requests from customers such as for higher performance and lighter weight. If we respond by changing the material of peripheral parts to plastic, the behavior, such as resonance frequency will change as well. modeFRONTIER will run the process of the old fashioned elimination method by trying out all the conditions according to the experiment plan. We are checking it out in hopes that if it works with the sensor, it will also work for the servo motor.
The nice thing about modeFRONTIER is being able to calculate optimization of thermal, stress, and structural analysis as a set.
Koji Kokue:
In terms of magnetism, I think that if JMAG’s GA (Genetic Algorithm) is used correctly, it can also select the optimal motor. The sensitivity of each design parameter is obtained from the analysis results of motors selected by the experiment method, then the combination that achieves maximum sensitivity is identified and narrowed down to the optimal value. This is a pretty difficult process that takes a lot of time and effort. We use GA thinking that it will automatically perform this task, but I don’t think using it correctly is as easy as it is thought to be. It takes much more effort than merely drawing up a model and pushing a button to obtain the optimum motor.
Hideo Kumagai:
AI is a keyword that is often used these days. I heard from a person who launched an automatic driving software company that he wants to “change the way of thinking” up to the point of developing an automated vehicle manufacturing system. He feels automation is necessary to tackle the imminent lack of younger people due to the declining birthrate and aging population. I thought about what would happen to our company when the time comes. If automation became mainstream and anyone could achieve the same results, we wouldn’t stand a chance when China starts mass production of low-cost motors. We will have to think of something different. Rather than trying to follow the trend for automated design, I feel we will need to work on a different product development sooner than expected.
Hideo Kumagai:
I don’t think we are creating designs with a fixed concept but it would be great if we could create an extraordinary servo motor that would change conventional concepts. The benefit of using automated design would be to show that it’s OK for example that the rotor and stator can be on opposite sides or the shaft can be outside of the axis center instead of being in the center.
Koji Kokue:
I think using automated design to come up with ideas that humans can’t think of is good for research but I personally wouldn’t want to use it now. I feel it is more important to train designers to be able to identify the problems in what computers selected; designers who can understand just by looking at a diagram and figure out which part of a magnetic circuit is not necessary, where the source of heat is, and how the performance will change depending on what we do. I believe this can all be done with analysis. Currently, you can tell at a glance that many of the examples of automated design are not optimal. That may be because these examples are explanations or PR material for optimization algorithms, but most of the motors that are selected as examples of optimum motors are not optimal. If a motor selected as optimal varies depending on how to be approached, that motor would not be optimal.
I’m not saying that every bit of automation is not good. As I explained, automated design is a tool that would be a great help in design if used correctly. However, using computers to select the optimal solution without human involvement or having computers think of ideas that humans can’t come up with are things that should be done in a university laboratory. This kind of development is sure to happen in the future.
Message for JMAG
Koji Kokue:
There are two major things we expect from JMAG.
The first is improvement to make the JMAG-Designer tool easier to use. There are several areas that I feel would be much easier to use if a few changes were made.
For example, the part ID that is automatically assigned by Geometry Editor is also used in JMAG-Designer. However, the user is unable to change the ID, so every time the model is modified a new ID is assigned and you end up with a whole lot of IDs. This creates quite a bit of extra work. I would also like to see enhancements made in minor less noticeable functions.
Second, we would like to see more consideration given to the use of external spreadsheets and other software. It is more convenient to use other spreadsheet software to display graphs and check analysis conditions. I save only the project file with the mesh deleted and the result table CSV file of past analyses so that I can rerun an analysis at any time. It would be easier to use if data is output based on the assumption that external tools will be used without trying to do everything in JMAG-Designer.
Interviewee
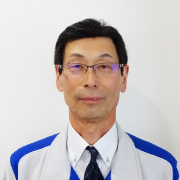
(Ph.D., in Electrical Engineering)
Senior Managing Director
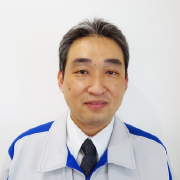
General Manager,
Engineering and Quality Management Department
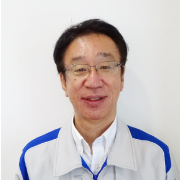
Engineering and Quality Management Department,
Quality Control Section
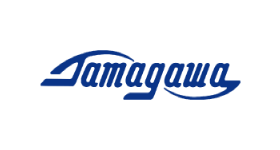
395-0068, Japan
You need to sign in as a Regular JMAG Software User (paid user) or JMAG WEB MEMBER (free membership).
By registering as a JMAG WEB MEMBER, you can browse technical materials and other member-only contents for free.
If you are not registered, click the “Create an Account” button.
Create an Account Sign in
Recommended resources about sensors/resolvers
- Tosei Engineering corp. : Activity in the Visualization in Non-contact Sensing for Assurance Accuracy, JMAG Users Conference Proceedings, 2022
- Tamagawa Seiki Co.,Ltd. : Design of a High-Density and High-Output Motor Using Optimization Analysis by GA, JMAG Users Conference Proceedings, 2022
- Tamagawa Seiki Co.,Ltd. : Electromagnetic Field Analysis of AB Phases and Z Phase Magnetic Interference in a Magnetic Encoder, JMAG Users Conference Proceedings, 2020
- Coto Technology : The Value of Magnetic FEA Simulation in Magnetic Sensing Applications, JMAG Users Conference Proceedings, 2020
- Tamagawa Seiki Co.,Ltd. : Efficient 3-dimensional optimization technology for high-precise magnetic rotation angle sensor, JMAG Users Conference Proceedings, 2012
- [W-MB-157] Evaluation of the Effect of Resolver Eccentricity on PM Motor Torque Ripple Control, White Papers
- [RTML-049] PMSM/IPM Constant rating 75(kW) 3-phase Resolver
Recommended resources about factor analyses using simulations
- TOYOTA CENTRAL R&D LABS., INC. : Measurement Technique for Magnetic Flux in a Motor Core under Operating Conditions, JMAG Users Conference Proceedings, 2019
- Mitsubishi Electric Corporation : Study on Robust Optimization Method for Cogging Torque Reduction Accounting for Manufacturing Errors of the Motor, JMAG Users Conference Proceedings, 2016
- Valeo Equipement Electrique Moteur FRANCE : Influence of the manufacturing process on the behaviour of a claw-pole generator, JMAG Users Conference Proceedings, 2014