Sinfonia Technology has been developing technologies steadfast in its effort to respond to customer needs for more than a century since its founding. Today, the Company expands twelve different businesses and offers a broad lineup of products. Sinfonia Technology consistently offers industrial systems founded in high-quality products and technologies via its Sinfonia New Stage 2024 medium-term management vision, all of which contribute not only to the development of society but also the lifestyle of each person on Earth as well as human pursuits into outer space.
As an electrical machine manufacturer, Sinfonia Technology boasts a diverse product lineup that leverages its technological development capabilities centered on rotation machines and power electronic technologies.
We had the opportunity to interview the team responsible for pioneering so many innovative new products around these core technologies from the Research & Development Laboratory. This is what they had to say.
A Century of Helping Advance Our Lifestyles and Society at Large
Junkichi Inaba:
Sinfonia Technology started out as an electrical machinery plant at Toba Shipyard in Mie Prefecture in 1917. We were under the umbrella of Suzuki Shoten in Kobe before changing our name from Shinko Electric Co., Ltd. to Sinfonia Technology Co., Ltd. in 2009. In 2017, we celebrated our 100th anniversary.
We develop a wide range of products as an electric machine manufacturer with a long history in motors, generators, and other rotation machines going back to our founding. Our core strengths are in rotation machines and power electronic technologies. Today, Sinfonia Technology is focusing on four main business segments: motion systems, power electronics, support and engineering, and clean transportation systems. Within these segments, our businesses can be divided into the twelve categories listed below.
Source: Sinfonia Technology Corporate Website
Our largest business right now is the Clean Transport System business. We hold the top market share for load port products. This equipment acts as an entry port for the semiconductor manufacturing system to receive wafers supplied by the semiconductor production line. Our Toyohashi plant is primarily responsible for the design and production of these products.
The Toyohashi Plant also handles products that leverage electromagnetic force. On the automotive testing side, we develop equipment that can test and evaluate the performance of primary motors in electric and other vehicles. On the industrial infrastructure front, we develop motors and other machines that can be submerged in liquids. This includes the submerged motors built into pumps for transporting LNG and other cryogenic liquified gases. In fact, we are using JMAG to design induction heaters for ultra-high vacuum melting furnaces that are used to develop sophisticated metal materials.
The Ise Plant develops products for the aerospace business. We developed the servo actuators for the attitude control used to change the orientation of the nozzles on the H-IIA and other space rockets. JMAG has begun to play a role in these designs recently as well. Our Aerospace Systems Works Engineering Department coordinates with us in the Research & Development Laboratory to develop the high-power density motors that have shown promise in reducing the CO2 emissions produced by aircrafts. In the Motion Systems Segment, we are developing industrial motors, direct drive motors that support the miniaturization of semiconductor manufacturing equipment as well as high-speed rotation motors specifically designed for textile machinery. In addition, Sinfonia Technology develops other electromagnetic machines besides rotation motors. We not only use JMAG to design high-speed generators for speed detectors in rolling stock for the Transportation and Power Control Systems Business but also electromagnetic clutches and industrial breaks for the Clutches and Brakes Business.
I have focused on products that utilize electromagnetic force thus far, but I would also like to mention that Sinfonia Technology has launched a new business in the regenerative medicine sector. This venture has successfully commercialized a fully automated cell culture instrument that is completely closed and separated from the outer environment. We have also set up a Solution Lab in the Foundation for Biomedical Research and Innovation (FBRI) next-generation cell contract manufacturing facility inside the Kobe Medical Innovation Center. This hub will better support the industry in building more efficient environments for culture cells.
We are currently in the second half of the Sinfonia New Stage 2024 medium-term management vision that started in fiscal 2022. In accordance with this vision, our efforts are focusing on new product and business development for the purpose of fostering sustainable corporate growth in the future. These initiatives will transform the product portfolio with the aim to reach a new stage where Sinfonia Technology can realize stable corporate growth as well as contribute to the development of a sustainable society.
Junkichi Inaba:
The new Sinfonia New Stage 2024 medium-term management vision designated stronger technological development capabilities, new product development, and new business creation as priority themes for the Research & Development Laboratory. We strongly recognize our use of electromagnetic force to be the core of Sinfonia’s technologies. That is why the Mechatronics Technology Group under the Research & Development Laboratory will work to revolutionize and commercialize technologies as new products take better advantage of electromagnetic force. The Base Technology Group consists of four teams tasked with specific missions—analysis, material development, vibrating technology development, and the technical configuration of analysis technologies. These teams mainly deal with the design and development of fundamental technologies rather than being directly involved with the products. Each team plays its own unique role in solidifying our technological capabilities.
Training Using Real Product Models
to Enhance Technology and Deepen Understanding
Junkichi Inaba:
Sinfonia had been using its own in-house finite element analysis software up until the 1990s when we began using standard commercial finite element analysis software alongside our own systems. However, commercial software only provided static magnetic field analysis, which limited how much we could use it in designing rotation machines. In the early 2000 though, many people in the company began using 3D-CAD software. We decided to start using JMAG-Designer in 2006 to take advantage of the open interface that linked to a variety of 3D-CAD software. Our design engineers found JMAG very easy to use. As word spread with praise about how easy it was to use to design rotation machines, the percentage of engineers using JMAG skyrocketed. We ended up adding two additional JMAG licenses in that first year, and have continued to add even more licenses ever since.
Junkichi Inaba:
Two of my colleagues with us for the interview today joined Sinfonia Technology in 2012. This was the first year that Sinfonia started to provide annual magnetic field analysis seminars for new employees using JMAG. Even since these two participated in that seminar, the number of JMAG users has continued to grow in each business department. I think this shows how effective these regular in-house analysis seminars have been. This face-to-face training program that uses the Self Learning System (SLS) provided by JMAG teaches trainees how to use the software. To teach modeling techniques essential to an analysis, the seminar even uses example models of our products because a generic model is simply not enough to learn how to practically run these kinds of analyses.
That is why our approach teaches employees how to create models and run simulations using actual models of our own products. Although this is only an introductory program, team members from the Research & Development Laboratory step in as instructors, which lets trainees get to know the people who they can consult with when running analyses on the job. I would guess this makes everyone in the Research & Development Laboratory more approachable for new employees. However, computer-aided engineering (CEA) software is one tool in the tool box. I think the only way to fully understand the power of analyses is to also learn how to utilize those skills in the design process. Therefore, in addition to the training program for new employees, we started a small group training seminar for our next generation of core motor designers in 2021.
Yudai Fujioka:
Although I will refrain from giving a specific number of employees who run analyses, I will say there has been a steady increase in each department thanks to the analysis training that has been provided to new employees for over a decade. This training seminar now includes every type of analysis necessary for motor design from magnetic field analyses to structural and thermal analyses as well. In the Mechatronics Technology Group where Tatsuya Nemoto and Shunya Watanabe work, we use many different analyses to mainly create new motor technologies. In the Base Technology Group where Junkichi Inaba and I work, we test analysis accuracy and develop analysis technologies to enhance design versatility and usability.
Yudai Fujioka:
I have found that JMAG has brought a common language into the company to discuss electromagnetic design, which is great. I have used various design tools in the past, but those types of tools only run simple calculations to output the torque based on the motor dimensions and current values input by users. One benefit of JMAG is that it goes beyond this simple output to simulate and visualize actual physical phenomena using flux lines and contour plots. It makes it easy to quickly find places where I can improve designs because I can easily tell whether there is a lack of torque due to a concentration of magnetic flux in certain areas or iron loss produced from alternating magnetic flux.
JMAG is also much more user-friendly than other analysis software for other types of analyses. User-friendliness is an extremely important part of these types of software. No matter how accurate the results are, software that is hard to use will never find a foothold inside a company. If only a select few people are able to use a tool, there is also no way to increase the overall skill level and expand use to everyone. That is why having software that is accessible to everyone is so important. In that way, JMAG is easy to use and provides results that are easy to evaluate. Even in internal design reviews, we are able to use screens pulled right from JMAG in presentation materials to illustrate exactly what is happening in the electromagnetic design.
The accuracy of the loss analysis is one area that I think could be improved. I would like you to share information about this with us in the future. Another would be speed of the analyses. JMAG is getting faster and faster every year though, which is something I am happy about. I’m expecting even faster analyses in the future too.
Shunya Watanabe:
I need to specify each and every setting when running a simulation of alternating current loss or when examining a part in detail, which takes time. I would love to have a feature that provides various templates for these settings.
Tatsuya Nemoto:
Each business department needs to pursue designs in an ever-shorter timeframe. I agree with Shunya that specifying all the settings in JMAG-Designer can be tedious. Some people choose to use JMAG-Express rather than JMAG-Designer for this reason. The Research & Development Laboratory has more leeway in this regard.
From a proficiency perspective, I do feel it takes time to modify models, materials, and other analysis conditions. SPEED or JMAG-Express gets a bit closer to the needs of motor designers by providing tools that anticipate what a motor designer might do. This makes the software very user-friendly for us as motor designers.
It would also be nice if the JMAG Geometry Editor was more user-friendly. The link to SolidWorks may be a solution to this problem, but it takes time to update geometry modified in the CAD program in JMAG, sometimes halting the optimization process. The best-case scenario for me would be the ability to handle everything right in JMAG.
JMAG Enhances Both Internal and External Informational Sharing
Yudai Fujioka:
As I said earlier, we have a long history and our products cover the full gamut of machines. Each department differs in terms of motor capacity, usage environment, and even application, which brings a strongly unique product lineup to Sinfonia Technology. This also means that the tools each department uses to create designs are also different. In one of the departments that creates its own program for motor design based on equations of electromagnetism, the programs may sometimes reflect past results and experience. This builds a communication barrier between these designers and designers from other departments. In recent years, Sinfonia has been looking to expand products across these organizational boundaries. Common design tools streamline this communication to ensure very smooth discussions between designers. The benefits have become very apparent lately for me.
Each of our departments has someone who uses JMAG. In cross-departmental discussions about electromagnetic designs, we communicate with one another using JMAG data. As a technology used throughout the company, JMAG has made it very easy for each department to communicate with one another.
Yudai Fujioka:
That is true for us too. Our motor subcontractors who request motor analyses are currently using JMAG as well. We make a wide range of requests to these people outside of Sinfonia Technology. Everyone using the same analysis software makes everything so much easier. There is common ground to say that the accuracy will be great in some areas if, for example, you calculated the iron loss in a certain way, but that will sacrifice accuracy in other areas.
Yudai Fujioka:
Shunya Watanabe and I are the first generation of designers to use JMAG across departments, which was difficult at first. We struggled to figure out how accurate the analysis results may or may not be.
We could get a rough idea about how well the analysis results would match the actual measurements based on past results from our prior development projects, but this kind of past knowledge doesn’t apply when the development seeks to drastically change the machine specifications. That is when we need to validate things using JMAG, but designers from the Engineering Department often asked how much we can really trust the analysis results. The Research & Development Laboratory would look at the track record to explain that the torque is usually pretty close but the losses do vary from analysis to analysis. This is where we had the most trouble at first.
Yudai Fujioka:
Of course. We have a wealth of analysis results and experience now to know how much the losses may vary based on the type of motor that we are simulating. However, I still do think even more experience will be beneficial as JMAG becomes used more and more broadly at Sinfonia Technology.
Higher Loss Analysis Accuracy for High-efficiency Product Development
Yudai Fujioka:
I am currently trying to improve the accuracy of loss analyses. When I first started using JMAG, I would refer to material data in order to calculate the iron losses. Around 2015 or 2016, we began to use play models and the ID method, which can calculate losses for magnetic flux density at higher frequencies. The correction for anomalous eddy current loss has also been updated from the use of constant values to an eddy current loss factor table. JMAG rapidly incorporates these types of new calculation methods, so I check to see what happens when I apply different approaches to an analysis.
In the past, the challenge was how to modify a design to increase motor efficiency. This was done by looking at contour plots illustrating the loss distribution. I think JMAG’s feature to visualize the loss distribution is quite handy. By switching to a new method to analyze the losses, I discovered that the losses were concentrated in a different area than I thought that they would be. After I changed the dimensions to reduce the losses in that area of the model, I was able to retain the motor structure but still enhance the efficiency.
Yudai Fujioka:
Motors are quickly pursuing higher and higher speeds. We want to reduce the iron losses as much as we can, but the struggle has always been that the iron losses analyzed at high speeds do not accurately match the measured results. The thermal design is also challenging. We have to cool any heat that is produced in a motor, which means that we have to identify the mechanism to understand where, why, and how much heat is being generated.
Yudai Fujioka:
At Sinfonia Technology, we decided whether to use a 2D or 3D analysis based on the product. For instance, a 2D analysis provides relatively accurate results for testing systems. Our department that deals with flat motors uses 2D analyses to create a general design before running a 3D analysis in the final decision-making phase to account for the leakage flux.
Tatsuya Nemoto:
To add onto this a bit, we have to run 3D analyses for induction motors because the leakage inductance has quite a lot more impact on an induction motor than a PM motor. As proposed by one example of the JMAG Application Catalog, we initially run a 3D analysis to verify the effects of the leakage inductance, and then incorporate these results into subsequent 2D analyses. This approach has generally worked well as a correction for the leakage inductance in the 2D analyses.
1.Hysteresis Loss Distribution (Time Average)
2.Eddy Current Loss Distribution (Instantaneous)
Motor Loss Contour Plots
Yudai Fujioka:
The Research & Development Laboratory is responsible for coordinating with designers in each business department. For things like loss analyses, I share what we are doing by supporting designers who need help using the analysis technology that our laboratory has amassed over the years. We work with each business department to investigate and solve any problems they have because the Research & Development Laboratory is tasked with evaluating any and all analysis technologies. Most recently, we have been consulted more and more by designers from a variety of departments asking about how to realize higher motor speeds in their designs.
Tatsuya Nemoto:
Of course, not every motor seeks to achieve higher speeds. Low-speed and precision motors are also important machines. The Motion Systems Business is often trying to design motors rotating at extremely slow speeds to use for precise positioning applications. In this way, the types of questions that we handle really vary depending on the application.
Realizing the Highest Output Density Ever Seen
Tatsuya Nemoto:
Yes, we researched and developed a multi-pole motor drive intended for applications in aircraft. To research a high-output density design and establish a design approach, Sinfonia Technology participated in the NEDO High Power Density Electric Propulsion Motor System R&D for Low CO₂ Emission Aircraft Feasibility Study Program from fiscal 2019 through fiscal 2021.
Our design was able to save space by arranging the magnets in a V-shaped orientation to realize a high output density. To reduce the high-frequency losses produced by a multi-pole motor, we used segmented magnets to restrict the eddy currents often occurring in magnets. The use of an edgewise coil mitigated alternating current loss in the coil as well. This development project used JMAG to analyze different options that could realize a high-output density motor to achieve a design that would satisfy the design specifications. Another challenge though is building an optimal cooling system because high-output machines do generate a lot of heat. We are in the process of developing the ideal motor cooling system by using heat flow analyses in combination with the development of various other technologies.
Tatsuya Nemoto:
Initially, we sought to reduce the weight, including the mechanical structure. Rather than start off by running highly precise JMAG analyses, we first hashed out a rough idea for the overall size of the motor structure. Next, we used JMAG-Express, a tool that can quickly model, analyze, and refine the motor design as a way to balance the size versus torque. Finally, we looked at the magnetic circuit design using JMAG-Designer. As with other machine designs, our approach is to dig deeper and deeper into the design while increasing accuracy along the way to examine what is feasible.
Tatsuya Nemoto:
I guess the first step when examining the motor structure is generally to devise a design that can satisfy the required specifications if there are any. Sometimes, the design specifications can be quite restrictive. The question becomes how much torque we can generate within those constraints, which is not only estimated on a theoretical basis but also using JMAG-Express to consider the design in more detail. However, JMAG-Express does not provide a comprehensive enough analysis to reach the final product. That is when we turn to JMAG-Designer to run analyses while gradually increasing the accuracy. Of course, running analyses in JMAG-Designer does take time. That is why we only look at the various structural design patterns that have the highest potential for use as the motor design.
Exterior View of the High-Output Density Aircraft Motor
Tatsuya Nemoto:
We do not use thermal fluid analyses at the really early stages of a design. During the initial phase of development, we estimate the thermal flow by approximating the amount of thermal conductivity theoretically. Once we have detailed geometry, that is when we need to tackle pressure losses and issues like that. We take each of these challenges on while gradually increasing the analysis accuracy.
Junkichi Inaba:
It has only been in the last few years that thermal fluid characteristics have really started to apply to the design. In all honesty, the analyses are still not accurate enough to be trusted. That is why we combine elemental testing of a potential cooling system with analyses as well as empirical formulas for the heat transfer. This seems to be the most efficient way to accurately examine the thermal characteristics as long as it is within the range of those empirical formulas. We can identify specific thermal phenomena that we know we should definitely run an analysis to evaluate, and then apply the heat transfer coefficient in thermal analyses to simulate that heat.
Yudai Fujioka:
Although there are still some issues in simulating iron losses in analysis software, I think some of the responsibility does fall on the users. That said, I have no doubt that the difference between the analysis results and measured results is smaller than when we first started using JMAG. Going forward, we will continue to look at what we can do on our side, whether it be how to handle the current waveform or how to take into account discrepancies between the geometry model and actual machine dimensions.
The play models are a good example of this. Sinfonia Technology has put in place a system that can measure the hysteresis loops to use with these play models so that we can handle the entire process in-house. JMAG has given us new iron loss estimation methods that offer even higher accuracy. In order to take full advantage of those features, we knew we needed to acquire the necessary input data ourselves as users.
The New Frontier Shifting Simulation Technology
from Part to Total System Design
Yudai Fujioka:
I saw a lot of presentations at the JMAG User Conference last year about combining various analyses. Over the last few years, I have noticed this become a trend with engineers. More and more of them are reaching out beyond just JMAG to integrate thermal and structural analyses as well as control circuits. I feel like there are so many more case studies that evaluate the system at large.
At Sinfonia Technology, we encounter vibration and noise issues as we work to satisfy the motor design requirements for not only higher speeds but also miniaturization and weight reductions. To overcome these issues, I would like to evaluate the vibrations and noise resulting from the electromagnetic excitation force using coupled vibration analyses.
Heat is one that I mentioned before. Heat is becoming a much larger issue than it was before as we pursue smaller and lighter designs that sustain the same motor output, which increases the heat density. I feel we need to evaluate the entire system at large by combining JMAG with thermal analyses to determine specific areas that we either need to concentrate cooling or focus on reducing losses. I would like to put effort in to the kinds of multifaceted analysis initiatives considering the entire system.
Yudai Fujioka:
Yes, they do. Although it is not about catching up to or besting our competitors, these presentations show us the level that many motor manufacturers have reached and the minimum that we have to do to stay in the game. I think the JMAG User Conference has been great as a place to get our hands on insightful information.
I remember that many of the presentations at one point emphasized ways to reduce the electromagnetic excitation force in the motor itself. I believe many engineers have obtained the electromagnetic force of a motor model and presented the changes that they made to the core geometry to reduce that electromagnetic force.
More recently though, the presentations seem to look at how the electromagnetic force impacts the structural system and how that would affect the entire vehicle equipped with that motor. It is presentations like these that seem to demonstrate the rapid shift toward evaluating the overall system design rather than just the motor design.
I would like to thank all of you so much for taking time to talk with us today.
Sinfonia Technology Research & Development Team
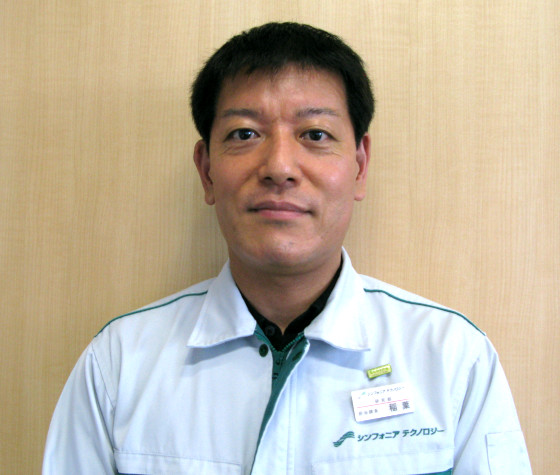
Manager & Senior Engineer
Research & Development Laboratory
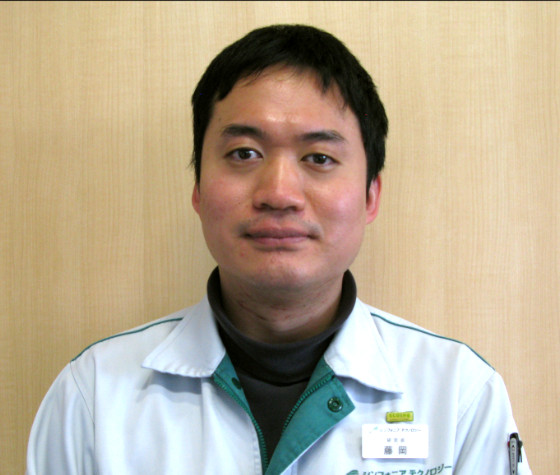
Base Technology Group
Research & Development Laboratory
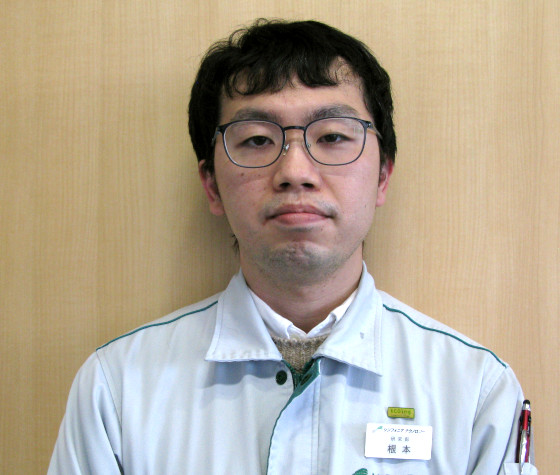
Mechatronics Technology Group
Research & Development Laboratory
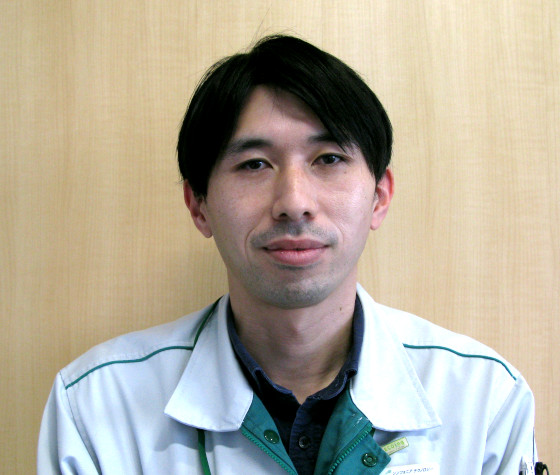
Mechatronics Technology Group
Research & Development Laboratory
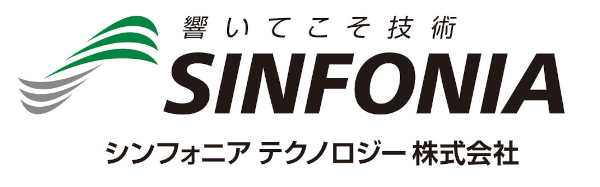
1-30 Shibadaimon 1-chome, Minato-ku, Tokyo,
105-8564, Japan
- Clean transport systems (semiconductors)
- Testing systems
- Vibrating equipment
- Parts feeders
- Industrial infrastructure
- Social infrastructure
- Aerospace
- Motion systems
- Transportation and power control systems
- Large transportation systems
- Printer systems
- Clutches and brakes
- Regenerative medicine, logistics, and agriculture
You need to sign in as a Regular JMAG Software User (paid user) or JMAG WEB MEMBER (free membership).
By registering as a JMAG WEB MEMBER, you can browse technical materials and other member-only contents for free.
If you are not registered, click the “Create an Account” button.
Create an Account Sign in
Recommended
- Okayama University : Aiming for Further Improved High Power Density Motor , JMAG Users Conference Proceedings , 2022
- Tamagawa Seiki Co.,Ltd. : Design of a High-Density and High-Output Motor Using Optimization Analysis by GA , JMAG Users Conference Proceedings , 2022
- Rolls-Royce Hungary kft : Electrical Machine Loss Simulation and Model Validation Using JMAG and MATLAB Simulink , JMAG Users Conference Proceedings , 2022
- IAV GmbH : Next Generation EV Motor Design Using JMAG-Designer , JMAG Users Conference Proceedings, 2021
- Honda R&D Co.,Ltd : Performance Analysis Method of IPM Motor for EV Using Electromagnetic Simulation(JMAG) , JMAG Users Conference Proceedings , 2021
- Sumitomo Electric Industries, Ltd. : Comparison of Axial Gap Motor with SMC Between Analysis and Experimental , JMAG Users Conference Proceedings , 2020
- AVL software & function GmbH : Load Influence on AC Resistance of a High-Speed Permanent Magnet Electric Machine for Electric Vehicle Applications , JMAG Users Conference Proceedings , 2019