Supporting the Success of New Businesses
The Nidec Corporation, a top manufacturer of small precision motors used in devices such as hard disk drives and CD-ROM drives, entered the automotive market with a mid-size motor for power steering in 2000. The tool that facilitated their growth and success in a market the Nidec Corporation had little experience or knowledge was JMAG, an electromagnetic field analysis software from the JSOL Corporation. Less than 10 years have passed and the Nidec Corporation has grown to hold roughly 10% of the market share. Mr. Hitoshi Inoue, head of development for the Nidec Corporation, and Mr. Nakaba Kataoka discuss the merits of implementing the JMAG system.
JMAG Supports Growth Entering New Markets
Mr. Inoue
There are three major types of power steering; “hydraulic systems” which uses the engine’s output, “hydraulic-electric systems” where the motor output assists the hydraulic pressure, and ” electric systems” which use an electric motor. We decided to enter the market with a motor for hydraulic-electric power steering in 1995. Our first product was used in the “Peugeot 307” in August 2008. Amazingly this vehicle earned the European “Car of the Year” award, increasing our sales to provide us with a powerful foothold in the power steering market.
Currently, we lead in hydraulic-electric type power steering and hold approximately 10% of the market share. Our power steering has been implemented in vehicles from manufacturers such as Peugeot, Citroen, Ford, Nissan, and Renaud.
The power steering market, especially the electric types, is expected to grow drastically in the field of automotive components. Only an electric type motor can be implemented when the engine of hybrid automobiles stops at idle and the demand for precise steering and fuel efficiency grows. We are focusing all of our effort into the development of fully electric motor prototypes as we expect the demand to increase.
Mr. Inoue
Entering the competitive ring for components mounted on vehicles with a motor for power steering was quite challenging for us. We had experience in designing continuously variable transmissions and reduction gears, but we had never designed motors for power steering. As a vital safety device that protects the lives of the driver and passengers, power steering needs to be viable in severe climates from -40 to 120 degrees Celsius. The severity of conditions for motors we where designing at the time was from -10 to 40 degrees Celsius. I mean, we had no idea what kind of characteristics to expect from a motor at 120 degrees Celsius. The major factor to secure when designing these types of components is reliability. Simulation and analysis software was vital in supporting us throughout the design process.
Mr. Kataoka
I was asked to evaluate a variety of analysis software because we knew, even at that time, it would be indispensable. Kataoka We had already been using analysis software provided by a different company, but we needed the tools specializing in design that JMAG offered to catch up and move past rival manufactures. In 1996, we benchmarked analysis software from 4 different companies, but JMAG was the software that met the specifications we desired in an analysis software.
First, the usability was fantastic. Next, the accuracy of the software when comparing analysis results and the actual measurements obtained after building a prototype were almost identical. The designers were able to use this software practically, reducing the number of prototypes that need to be made. We were confident that we could take on this new market using JMAG because we could reduce the number of prototypes. JMAG was evaluated so highly inside our company, that it was the only software we wanted to implement.
Fig. 1. Nidec Motor Sales for Power Steering
Fig. 2.Nidec Motor for Power Steering
Adhering to Development Costs while Increasing Speed
Mr. Kataoka
Even after evaluating the performance and actually using JMAG, I was surprised. We were able to reduce the number of prototypes, the amount of time, and the cost because of how closely the results matched the actual measurements. Basically, we were able to adhere to strict costs and increase the speed of development making it easier for us to step into this new market.
Mr. Kataoka
Mainly, we simulate specialized components, and components with complicated geometry. For example, as the temperature of a magnet in a motor raises and the current increases, the magnetic force is reduced by demagnetization. The analysis results we obtain are invaluable in miniaturizing our designs by reducing demagnetization as much as possible. We can perfect the designs to smooth the heaviness of the steering when the motor losses torque as well as hone the geometrical design of position sensors in motors, such as a resolver. The resolver rotor has a multi-pole design that offers extremely high-precision.
The requests of the automotive manufacturers get more and more demanding every year. Without simulation software like JMAG, we could not meet the request our customers have for the motors used in power steering, or improve balance between reliable and consistent performance for all of our product designs. You could even say that without analysis through simulation software, we would be expected to meet unattainable requirements. JMAG is a tool that allows us to develop more efficient parts that are smaller and lighter even as the development schedules get shorter each year.
Mr. Inoue
Some of the specifications and sizes our customers request are unrealistic, but explaining why is a difficult proposition. But using results from the JMAG simulation our designers can have confidence going to our customers and proposing, “We cannot achieve these characteristics at this size, but we can at this size.”
The most important aspect about using JMAG is that the results obtained with the simulation can actually be realized. The analysis results have to be accurate because the output provided by the design division is what the product becomes. JMAG is great at doing this. I think when Mr. Okamoto said, “designers are able to use this software practically,” this is exactly what he meant.
Fig. 3. Reduction in Lost Torque
Fig. 4. Internal Resolver Development
Flexible Software Allows Innovative Development
Mr. Kataoka
We are very grateful for the support we have received. The JSOL Corporation has a specialized support team that patiently handled all of our questions. For example, they created various tools as well as solved any flaws that we found. This support helped us vastly. As JMAG began being used throughout Nidec, I feel as though the support was enhanced to meet our growing need.
There are specialized analyses for motors to assist in design, such as analyses for demagnetization and variations in torque. Calculating this phenomena by hand was difficult, but JMAG allows us a tool to obtain analysis results automatically with a single operation. Through the innovation of the GUI, the conditions settings that used to take half a day to enter can now be done in ten minutes.
The amount of time to obtain the results from the analysis has also been vastly reduced by the ease of generating and dividing the mesh through an auto mesh feature that was implemented.
Mr. Kataoka
The amount of time for motor development requested by our customers has been reduced from 4 years when we entered the market to 2 and half years. There are many ways we are upgrading the development process to meet these requests, innovating development, reducing the number of prototypes, and reducing the amount of time required for the design process. JMAG is a vital part of these enhancements.
To remain strong in a competitive market, further innovation that reduces the amount of time required for an analysis as well as the ability to link to the 3D CAD data are necessary. Currently, an analysis of 3D data distributed to multiple computers takes three to four days. I would like to see the speed and the accuracy of the calculation improved even more. Currently linking to 3D CAD data is supported, but I want to be able to modify the data in the CAD software and have that data automatically reflected in the analysis software.
Strengthening Their Position in the Motor Market
Mr. Inoue
JMAG is a tool that makes it possible for designers to discover problems that occur from design to prototype through simulations they can run independently. American manufacturers break development into groups for analysis, design, and prototypes which often causes misunderstandings as well as errors in data between each party. But I think a concurrent type of development can be achieved by using JMAG.
JMAG will be a large part of our development process in the future. The popularity of motors is based on the maturity of the economy and culture.The number of motors being used in vehicles will increase. Furthermore, the importance of motors as a key drive train type device will most likely expand with the growing awareness of the products effects on the environment, such as energy efficiency.
We are also innovating various motor technology for hybrid vehicles as we aim to achieve EV (electric vehicles) motor technology. Magnetic field analysis is vital to facilitate this goal. We plan to increase the areas JMAG is being fully implemented, and I believe that JMAG will open doors for us to new opportunities.
Mr. Inoue
Inoue We always say, “contribute to environmental conservation by reducing CO2 emissions by converting automobiles, ships, and airplanes that currently run on fuel to an electric system.” The Nidec Corporation is striving to develop high-output motors. We competed in the F5B Championships, known as the F1 of radio controlled airplanes. The estimated performance of the motor developed by the Motor Engineering Research Laboratory installed in these planes achieved a power to weight ratio of 8kW/kg. This is a 30 percent increase from the standard F1 engine at 6kW/kg. Team Nidec, using planes powered by Nidec motors, swept the top three places of the 2008 Japan Championships, for the second year in a row. This motor technology will be implemented in hybrid vehicles and electric vehicles and most likely be adapted for electric ships and airplanes in the future.
Top 3 Two Years Running!
Motor and ECL for the F5B
Interviewee
NIDEC Corporation
Shiga Technical Center
Vice President
Mr. Hitoshi Inoue
NIDEC Corporation
Shiga Technical Center
Research & Development Dept.1
General Manager
Mr. Nakaba Kataoka
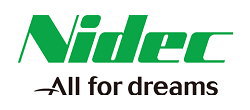
The Shiga Technical Center develops various motors for automobiles, OA/IT, and fans as well as strives to support commercial production and quality assurance.
[JMAG Newsletter November, 2009]