Evaluation and Selection of Electrical Steels using Simulation
The world’s leading manufacturer in the field of electrical steels, Tempel Steel. Tempel Steel has continued to provide electrical steels used in a variety of electrical devices such as motors for all applications including vehicles, generators, and transformers. JSOL’s electromagnetic field analysis software “JMAG” is used in their development.
We interviewed Mr. Charles R. Frontczak and heard how JMAG is used to select appropriate electrical steels on a cost-benefit basis. This report also includes content from the presentation he gave at the JMAG Users Conference 2012.
Mr. C.R.Frontczak:
Tempel steel is a 65 year old company and is still privately held. It deals primarily with precision electrical steel stamping for motor/generator and transformer industry. We also perform laser-cutting, deburring, recoating as well as die-casting and welding operations. We utilize the engineering know how experience along with precision tooling and presses that range from 10 to 550 Tons. Progressive as well as blank-and-notch dies are designed, built and maintained by Tempel Steel. We are also a trusted name when it comes to electrical steel performance data. Headquartered in Chicago, Illinois we have a global footprint with operations in Canada, Mexico, China and India.
Mr. C.R.Frontczak:
I work within the Marketing Technical Services (MTS) group as the electro-magnetic (EM) design engineer for electro-magnetic devices (i.e. motors, generators, transformers, ignition coils, etc.). More specifically, I show our customers how their designs perform through simulation with different types of electrical steel grades using the JMAG software. Cost reductions and improved efficiencies usually drive our customer’s requests.
Mr. C.R.Frontczak:
The initial trigger was to fill a need that was recognized by Tempel Steel, which was to have an EM engineer helping their customers make an economical decision in choosing their designs and materials. We needed an FEA tool to accurately capture the losses and predict the performance quickly and efficiently.
JMAG fits our need with being flexible and accurate with a quick turn-around time.
Mr. C.R.Frontczak:
I value JMAG from its easy interface, to the parametric case studies that I create in solving customer scenarios. For example, I set-up different lamination stack lengths and adjust the other parameters such as steel materials, copper and or aluminum turns and resistance to determine flux densities and iron losses. This enables me to improve efficiencies and reduce materials to cut costs.
Flux Density of IPM motor
Mr. C.R.Frontczak:
I can setup a JMAG model within 3-4 hours and usually have a rough answer that same day. Then by tweaking the mesh tighter and setting-up the parametric case studiesc I can send the model to a batch queue, let it run over night and have my answers the next morning. Without JMAG, I would be required to set-up the magnetic circuit on paper or use a homemade spreadsheet program to calculate the flux densities. Then I would calculate the performance characteristics based on the flux values and determine the power loss and thereby efficiency. However, JMAG provides a wealth of data that I can dig into to analyze the model. Additionally, Tempel Steel has the ability to fully test all electrical steel properties with a wide range of inductions and frequencies. This data allows me to input accurate steel curves which enables the FEA analysis to become more powerful.
Mr. C.R.Frontczak:
Yes. I still do some things as “Old School”. Example is when I assign FEM coils in my model; I link one coil group at a time to my circuit of individual FEM coils. This way the coils are not bunched together, and I can change their values during multiple studies. In doing this however, I would like a numbering and color coding sequence to take place as to avoid assigning FEM coils to duplicate geometry. I indicated this idea to the people at JMAG and they were very interested in making this change. In fact, my experience has been that they are very willing to adapt their software to customer input.
Mr. C.R.Frontczak:
Our customers are always looking to improve efficiency and reduce costs. Therefore, they look to us to help them in their efforts. Electrical steel pricing will remain volatile, so it’s imperative to have an FEA tool such as JMAG to look at performance behaviors as steel materials may change due to pricing pressures.
Mr. C.R.Frontczak:
Well, I do appreciate the on-going technical support, and the organization is always interested in improving their software. In fact, since I purchased JMAG 2 years ago I’ve seen updates every 6 months. I’m glad I did my initial research on Finite Element software and chose JMAG. It has made my job easier and fun to be able to work on so many different designs and to have detailed results and images to share with our customers.
Interviewer: Dheeraj Bobba, Powersys Solutions
Presentations of JMAG Users Conference 2012
Evaluation of Different Electrical Steels and Iron Loss evaluation of inter-locks vs welds vs bonded lamination cores in IPM Hybrid Motor using JMAG
This presentation focuses on electrical steel grade selection for Hybrid I.P.M. Electric Motors. Choosing the proper steel is the foundation of any good electro-magnetic machine. In most cases, there is insufficient data available for accurate properties of steel characteristics, especially high frequencies. Tempel Steel has developed methods, including Epstein and ring tests that generate a comprehensive range of core loss, permeability and magnetizing force data as functions of both frequency and induction. The use of this data input in JMAG allows the user to make educated decisions and places numerical values for each case study.
Additionally, it has added the iron loss differences between three methods of securing lamination stacks. These three methods are inter-locking, welding, and bonding.
Iron loss density of the interlocked model
Cited verse JMAG Users Conference 2012
Presentations, Tempel Steel Company Mr. Charles R. Frontczak,“Evaluation of Different Electrical Steels and Iron Loss evaluation of inter-locks vs welds vs bonded lamination cores in IPM Hybrid Motor using JMAG”
Interviewee
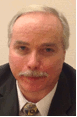
Sr. Electric Motor Design Engineer,
Tempel Steel
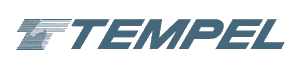
Tempel Steel Campany
5500 North Wolcott Avenue Chicago, IL. 60640
Tel: +773-250-8000
https://www.tempel.com/en/
[JMAG Newsletter March, 2013]