Overview
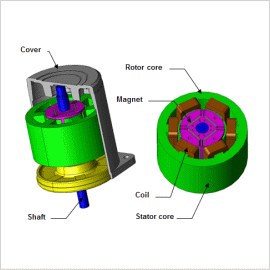
In order to carry out an accurate thermal design, it is necessary to first correctly understand the heat generation amount and location, so it would be advantageous to calculate the losses in a magnetic field analysis simulation using the finite element method, and from there to carry out a thermal analysis using the resulting loss distribution.
In this example, how to evaluate a motor’s temperature distribution by creating a thermal analysis model that can investigate the loss analysis and temperature distribution in order to obtain the motor’s total loss distribution, and then analyzing the elevated temperature process.
Loss
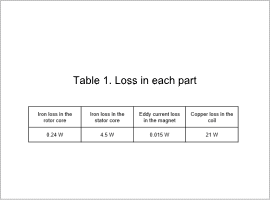
The loss in the coil is relatively large, and it is expected to be the main source of heat.
Temperature Distribution at Steady State
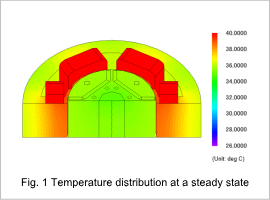
The result shows that the temperature is transferred from the coil to the surrounding parts.
Temperature Variation
The points where the temperature is measured in each part and the temperature changes when a 2 A current is applied are shown in Fig. 2 and Fig. 3.
Fig. 3 shows that the temperature in each part reaches a steady state.
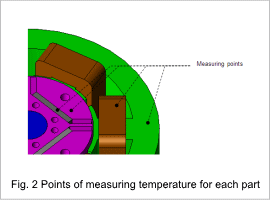
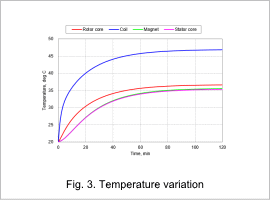
Consecutive Operating Time and Average Torque with Various Currents
The current was set at three times the rated value to increase the average torque to 1.0 Nm or above. The average torque and temperature variations in the coil are shown in Table 2 and Fig. 4 (see Fig. 2 for the points of measurement).
Although increasing the current produces a higher torque, at a motor drive time of 20 min the coil’s temperature exceeds the upper temperature limit of 180 deg C.
By carrying out a magnetic field-thermal coupled analysis in this way, it is possible to evaluate the motor’s properties and constraints with more detail.
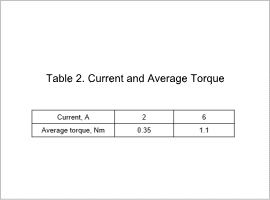
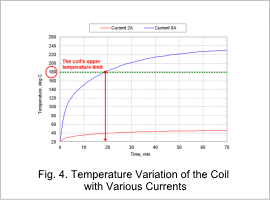