*Please prepare a license ID and password for the license administrator.
*It is different from the service for JMAG WEB MEMBER (free membership). Please be careful.
Overview
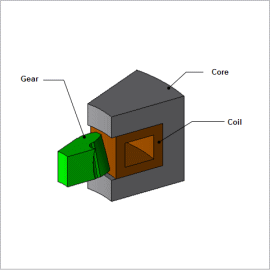
Since gears are products that demand mechanical intensity, high frequency induction hardening is run for surface heat treatment. Since induction hardening can rapidly heat only the surface of the gear in a short amount of time, the hardness of the surface is continually increased while retaining the toughness inside. On the other hand, the surface of the gear is exposed to high temperatures in the heating process prior to induction hardening; therefore, there is a possibility of thermal expansion.
This document introduces evaluates how heating ranges change depending on the deformation amount at high temperatures and deformation during heating, with heat generation analysis in JMAG and linking of heat transfer / deformation analysis in Abaqus.
This document introduces evaluates how heating ranges change depending on the deformation amount at high temperatures and deformation during heating, with heat generation analysis in JMAG and linking of heat transfer / deformation analysis in Abaqus.
Deformation Amount
The contour plot of the Z component of displacement is displayed in Fig.1, and the contour plot of the absolute value of displacement is displayed in Fig.2.
With the rise in temperature, deformation where the tip of the helical gear is open up and down the Z-axis direction has occurred, and deformation expanding in the circumferential direction can be confirmed.
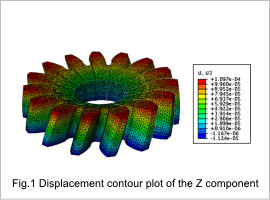
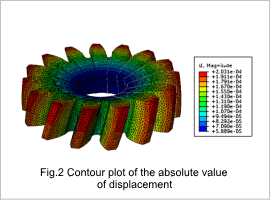
Temperature Distribution
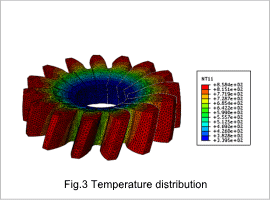
The temperature distribution at the end of the heating process is displayed in Fig.3. Eddy current is flowing at the gear tip part close to the heating coil, and the process of temperature rise can be confirmed.
Time History of Temperature
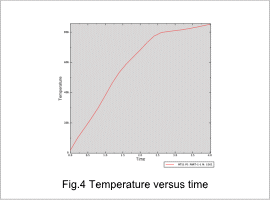
The process in which temperature is rising in the center part of the top edge of the gear tip is displayed in Fig.4. After temperature has exceeded the Curie point, the process in which the speed of the temperature rise is decreasing can be confirmed.
Stress Distribution
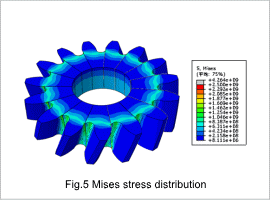
Mises stress distribution at the end of the heating process is displayed in Fig.5. The process in which stress is concentrated at the gear bottom due to temperature increase / thermal expansion at the gear tip of the helical gear can be confirmed.