Overview
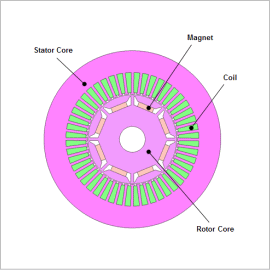
In this example, the optimum current phase that achieves high torque per each geometry is obtained, and the torque characteristics (1,000 r/min) and stress due to centrifugal force at high-speed rotation (10,000 r/min) obtained with that optimum phase are both taken as objective functions for a multi-objective genetic algorithm used to carry out the optimization of rotor geometry.
Optimization Conditions
Design variables in Fig. 1 are displayed in Table 1. 6 rotor shape design variables are selected. Magnet positions, magnet geometry, and flux barrier geometry that are considered to have a large influence on von Mises stress and torque are parameterized.
This time obtains geometry with high torque at 1,000 r/min and low von Mises stress within the rotor during rotations at 10,000 r/min. In accordance with this, 2 evaluation items shown in Table 1 are used and the performance of rotor geometry is evaluated.
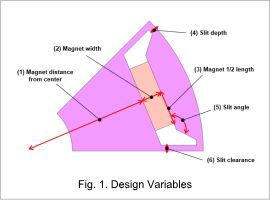
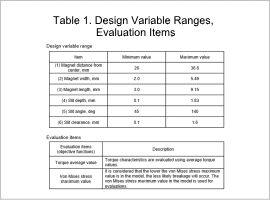
Optimization Results
Fig. 2 shows the result of multi-objective optimization using genetic algorithms with the maximum value of von Mises stress and average torque objective functions. Performance improvements can be confirmed from a comparison of all individuals from the initial and 10th generations. It can also be observed that von Mises stress and torque are in a trade-off relationship in the 10th generation.
The case with the lowest von Mises stress (1) and the case with the highest average torque (2) in the initial generation are emphasized. Cases A and B are 10th generation cases with the maximum average torque for approximately the same maximum von Mises stress as cases (1) and (2) respectively, and are shown in Table 2. While each have approximately the same maximum von Mises stress, it can be confirmed that average torque improves between (1) and A by 93 %, and by 16 % between (2) and B.
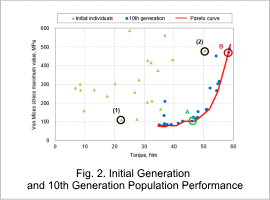
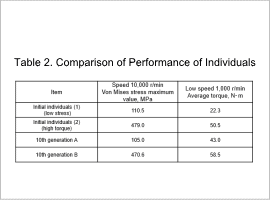
Selecting Rotor Phase
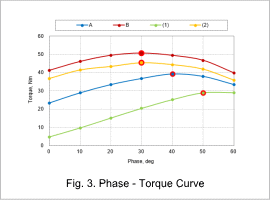
Rotor Interior Magnetic Flux Flow
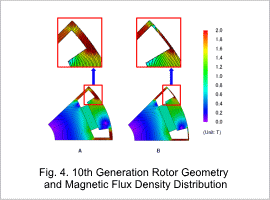
Von Mises Stress Distribution
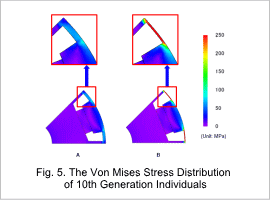