Comparing and Examining the Variability of Regulated DC Power Supplies via Simulation
Cosel Co., Ltd. is one of the leading market shareholders of high quality/miniaturized switching power source devices (regulated DC power sources), DC-DC converters, and noise filters for EMC. Cosel often manufactures their own specialized transformers vital to power supply modules by optimizing the geometry of cores and the structure of windings.
Masahiro Shima, Group Leader of the OS Design Dept. in charge of comparing and examining the variability of design specifications for DC-DC converters using magnetic field analysis simulations discusses why he decided to implement JMAG and how they are using it.
Satisfying the Demands for Small DC-DC Converters with a Higher Power Density
Mr. Shima
We handle regulated DC power supplies. The power produced by electric generation plants is distributed through utility poles to switchboards for residents and factories as an AC power source. A stabilized DC power supply is a device required to create voltage by converting the alternating power source to a direct current to use in electric circuits. Regulated DC power supplies can be separated into two large categories: unit type power supplies and on-board type power supplies. A unit type power supply is a type of power supply that can be added directly onto our customers products, such as industrial robots or vending machines. An on-board type power supply is a small power source that can be attached to our customers printed circuit boards, similar to other components. We also handle noise filters. Problems steaming from noise produced by devices or around devices is becoming more apparent as products get smaller and smaller. Noise filters are now an indispensable part of electric devices because of the malfunctions and reduction in communication speed cause by the noise.
Mr. Shima
Our customers require low-noise switching power sources with a high power density. However, heat becomes a problem as products are miniaturized. The losses inside of our products needs to be reduced to deal with the heat that is generated.
Increasing the reliability of our products with our technological strengths to reduce the heat generated internally as well as increasing the temperature range is vital to satisfying the needs of our customers.
Mr. Shima
In the OS Design Dept. were I work, we develop standard on-board type power supplies, examine new types of circuits, and create designs for smaller transformers. The on-board power supplies we are currently developing is a DC-DC converter. The Output power is 10 to 30 W. Designs are assigned to one of the engineers in each section. My responsibility as a group leader is to unify our engineers proceeding with the total development of the product while discussing the development with the design engineer in charge. The requirements for miniaturization and a high power density are requested by our customers. However, these products cannot be miniaturized without constantly worrying about costs unless the development is undertaken as a whole. My group is also responsible for developing transformers. We are especially focused on the miniaturization of transformers because transformers have the largest exterior dimensions of the products we handle. Transformers are one of the main sources of heat in DC-DC converters. The switching components also generate a large amount of heat requiring us to examine how to arrange the heat sources in a miniaturized product. Designs have to balance the power loss and heat dissipation because the losses will increase if the arrangement of the heat sources is too far apart to account for the dissipation of heat. Therefore, we optimize the arrangement of the heat sources by running a circuit and thermal simulation.。
Comparing and Examining the Variations of Products Using JMAG
Mr. Shima
We started looking into implementing 3D simulations to resolve quality control problems we were having with transformers. The inductance characteristics of transformers differs largely causing problems with the performance of the entire product. We had been using a 2D analysis software before implementing JMAG, but we couldn’t rely on the analysis because the depth of transformers is not uniform and 2D analysis software cannot analyze complex structures. We tried and benchmarked three types of 3D simulation analysis software. We chose JMAG because of the speed of the analysis and the results, such as the current distribution, could be visualized to make them easier to evaluate.
Mr. Shima
We use JMAG to evaluate the design specifications before building a prototype. We compare different designs before deciding on the geometry, but the characteristics often differed because of aspects or unexpected problems that cannot be fully judged using a sample prototype. Simulations can reproduce and visualize phenomena we hadn’t been able to fully capture allowing us to focus on the desired phenomena. Simulations are advantageous because we can comparatively evaluate the product to improve their designs without building a prototype.
Mr. Shima
When we first implemented JMAG, we examined what would happen to the characteristics of existing products if we changed their geometry. Now we use JMAG to examine the inductance and leakage inductance of transformers as well as the magnetic saturation when developing new products. The extent of our analyses has also increased since we first implemented JMAG. Our designs have improved because we can determine the geometry of the transformers while calculating he Joule loss for the entire design of our DC-DC converters.
Mr. Shima
We look at the variations after the design has been generally defined. There is a lot of trial and error used to determine the configuration of a product, but once the design is complete we put the product’s variability to the test. The standard flow of our development is: 1) determine the design through trial and error of the geometry and materials to satisfy the requirements at the design development stage; 2) examine the variations and quality of the product by trying to increase the yield ratio before beginning production; 3) rework the design to achieve the most robust product by refining the geometry based on the results from 2. We have to stop at a certain stage and consider the variations, otherwise, the time required for analysis would be overwhelming.
On-board Type Power Supplies from Cosel Co., Ltd.
(SU Series)
Product Developed by Masahiro Shima
(SU1R5 model)
Analysis Model
Mr. Shima
Cosel usually has a year to a year and a half to develop a product series, depending on the model. Conventionally, we would build 3 or 4 prototypes to finalize the geometry. Often multiple prototypes need to be made for transformers because of problems with the core and bobbin, but we only had to build a single prototype for models we have been developing recently. Even from a cost perspective, simulations are contributing greatly because 4 or 5 prototypes had been required for one series of on-board power supplies. Building the core for a single prototype, depending on the dimensions, can costs several 100 thousand yen. We just have to assemble the prototype once the design is complete. Although this is not too laborious, it still takes three weeks to a month to build a single prototype which means that our only option for reducing the time required is to decrease the number of prototypes. These are the greatest benefits in my opinion.
Magnetic Flux Density Distribution
Joule Loss Density Distribution
Sharing Design Knowledge and Establishing New Technology
Mr. Shima
We have a knowledge base that we use to register what we are developing at Cosel Co., Ltd and the methods used to resolve problems that occur with designs. Anyone requiring information at our company can browse design methods and problem countermeasures once the technological information is registered in the system. In addition, the engineers heading each division gather to present their findings. I have presented simulation analysis using JMAG several times. As far as I am aware, there are 5 or 6 other engineers that are currently using JMAG. Designers from other divisions often start using JMAG after seeing the contents and the analysis results I have used for my presentations registered in the knowledge base. Using JMAG is generally learned on the job, but many of our engineers start by coming to ask me about JMAG.
This is a little off the subject of computer aided engineering, but Cosel has a research technology department. They investigate new technologies that could be used in products developed in 5 or 10 years, such as new types of circuits, and then actively present their findings to academia.
Mr. Shima
Several examples of institutions we have partnered with for research are the University of Toyama, Toyama Prefectural University, Toyama National College of Technology, and the Toyama Industrial Technology Center. Usually, we go to the an educational or public institution with a challenging problem we have, and then work with them to find a solution. These institutions have access to simulation software we don’t currently have at our company to perform structural analysis that can evaluate vibrations and impacts.
Simulation Accuracy of the Design Tool JMAG
Mr. Shima
One of the greatest benefits is that the results from the prototype and simulation match. One of the largest hurdles is achieving the accuracy required of simulations, and not just in the field of magnetic field analysis. I have never had a large margin of error between the actual results and analysis results using JMAG. The results that we are after usually have less than a 10% difference, sometimes less than a 5% difference, depending on the product we are investigating. We reviewed several different software packages that we could potentially use, but we decided to implement JMAG because the results we obtained were the closest to the actual measurements taken from the prototype.
Mr. Shima
I started by trying to find the appropriate modeling for the physical aspects I wanted to obtain. The next thing I knew, I had gained enough modeling know-how to obtain highly accurate analysis results. It took between 3 and 6 months before we were actually using JMAG as a design tool. I am satisfied to a certain degree with the knowledge that I now have, although, that doesn’t mean I still don’t have a lot to learn. (Mr. Shima laughs)
Mr. Shima
As I said before, simulation technology is extremely vital to reducing the number of prototypes and improving the speed and efficiency of development under strict development schedules that demand a lot of trial and error to reach the final product. We are expanding the range we use JMAG, not just for electromagnetic field analysis, but also for other types of analysis. The chance for more and more companies that are not currently implementing simulation software to realize the benefits and impact simulations have from a prototype cost perspective will continue to grow.
Mr. Shima
I want to know the results and effectiveness of a product without having to build prototypes. For example, simulations allow me to examine whether the characteristics are improved or worsened by changing the geometry of a design. Being able to examine the variability is also important. I can calculate how much the characteristics differ from the variability that we predicted. Examining the geometry to account for the variability by creating a model is very difficult. Parametric analysis allows me to change the geometry and see what happens. I would like to see simulation analysis tools that are easier to use to compare products and examine their variations in the future.
Compact DC-DC Converters (DHS Series)
Interviewee
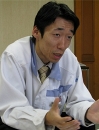
Group Leader
OS Design Dept.
Cosel Co., Ltd.
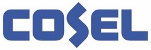
[JMAG Newsletter July, 2010]