Overview
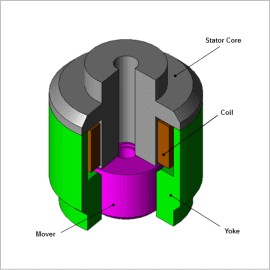
MATLAB/Simulink and JMAG can be linked directly when performing injector circuit control simulations. Taking into account eddy current effects as well, this allows injector characteristics to be reflected in more detail and allows evaluation of control systems that accurately model actual control systems.
In this example, an example of evaluating the difference in responsiveness of an injector when eddy currents are taken into account or not is presented.
Control Circuit
The 18-V DC power supply of the circuit energizes the coil via a switch controlled by MATLAB/Simulink.
The switch is controlled by hysteresis band control and maintains the current in a range around a reference current.
When current flows through the injector, the reference current is maintained until the plunger reaches its end position. After that the reference current is lowered to maintain the plunger at a specified position and finally the current value is returned to 0 after a certain time as shown in Fig. 2.
Fig. 1 shows the control circuit specifications, and Fig. 2 shows the control model.
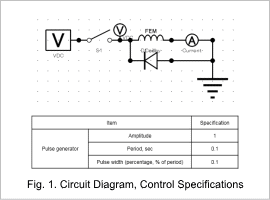
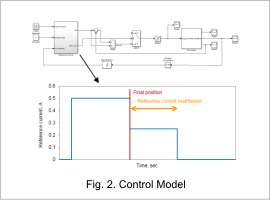
The Position of the Plunger and the Force Acting on the Plunger
Fig. 3 shows the plunger position and Fig. 4 shows the force acting on the plunger.
Looking at the position of the plunger in Fig. 3, it is seen that when taking into account eddy currents, it takes longer to reach the final position and return to the initial position.
This is because as seen from the force acting on the plunger in Fig. 4, when eddy currents are taken into account, the force generated on the plunger becomes smaller. The rate of change in force is also smaller. This phenomenon is caused by the generation of eddy currents which impede fluctuations of the magnetic field.
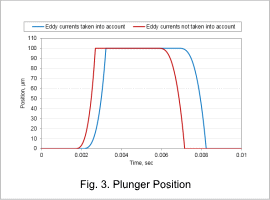
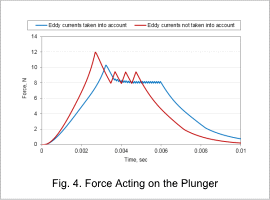
Effects on Coil Current Due to Eddy Currents
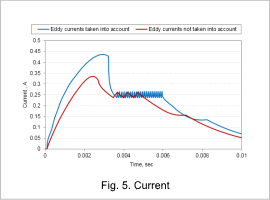
The model taking into account eddy currents has 30 % or more current flowing in the injector. That is, the power consumption increases.