Magnetization
JMAG can perform a magnetization analysis that reproduces magnetization distribution in a more realistic manner, allowing you to analyze the magnetization process in greater detail. Magnetic properties that define the magnetization distribution for the parts to be magnetized can be created as a material, referred to in JMAG as a “magnetization material.”
Furthermore, the material model calculated by the magnetization analysis can be added to the material database as a “User Magnetization” material.
Creating a Magnetization Material
Add properties of a magnetized material required for a magnetization analysis to the material database, and then use them. Define [Initial Magnetization Curve] which is the magnetic properties when applied an external magnetic field, [Magnetization Ratio] which defines the behavior of incomplete magnetization, and [Demagnetization Curve], and then perform modeling.
Importing the User’s Magnetization Material
After a magnetization analysis, the magnetization material that has been created is automatically added in the name of the study to the [User Magnetization] folder under [Permanent Magnet] in the material list. There is another method of doing this, however: A user magnetization material can also be added manually. Right-click [User Magnetization] and select the [Create New User Magnetized Material] to specify the calculated JCF file.
The calculated JCF file is then exported with the name “[input JCF file name] + _magnetized.jcf” to the folder where the magnetization analysis was run. If the magnetization analysis was run from JMAG-Designer, the [input JCF file name] is “Designer.jcf”, so the calculated JCF file name is “Designer_magnetized.jcf”. This JCF file is useful because it allows the same user magnetization material to be recreated in any computer.
JMAG Function Videos
* If you cannot access the video, please check here.
Temperature dependent material in thermal properties
In thermal analysis, material properties need to be specified are only three items, specific heat [J/kg/deg C], thermal conductivity [W/m/deg C], and density [Kg/m^3]. Specific Heat and Thermal Conductivity is set in the Thermal Properties tab of the Material Editor dialog box, and Density is set in the Mechanical Properties tab. All these material properties can be defined as the table value for Temperature Dependent and nonlinear properties can be taken into account. Temperature Dependency under Density is set to express a phase transformation such as density variations from metal’s crystal structure changes in high temperature.
In a coupled analysis between thermal and magnetic field, a model used in a magnetic field analysis is often used also in a thermal analysis as it is. Magnetic field analysis models, however, includes parts such as air regions that are not necessary in a heat conduction analysis, so they must be deleted. In such cases, just clearing the [Include This Material to Analysis] checkbox in the Material properties dialog box of the part makes it possible to delete the part. The part seems to be still exits in the model, but it is exempt from calculation, leading to the shorter calculation time.
Thermal Properties tab of the Material Editor dialog box
Mechanical Properties tab of the Material Editor dialog box
Temperature dependency table of thermal conductivity
Material properties screen
JMAG Function Videos
* If you cannot access the video, please check here.
Accounting for the Temperature Dependency of B-H Curves
Temperature dependent magnetic materials have to be used to improve the accuracy when running coupled thermal and magnetic field analyses that have large temperature variations. The temperature dependent magnetic materials that have been supported by user subroutines have been standardized.
These properties allow phenomena, especially in the magnetic saturation region, to be simulated more accurately than models using the conventional temperature dependent permeability. The accuracy has been vastly enhanced for analyses that have temperature variations over a wide-range caused by large currents, such as high-frequency induction heating.
However, the user needs to define these properties because the temperature dependent material properties are not part of the material database.
Temperature distributions after the quenching
JMAG Function Videos
* If you cannot access the video, please check here.
Detailed Iron Loss Calculation for Degradation
- Purpose
- Detailed iron loss calculation considering degradation due to punching
- Features
- BH characteristics can be modified by defining a “flux density – correction coefficient” table
- Affected ranges can be specified by selecting edges and faces
Image of degraded region
Specifying the degraded region (distorted region)
- Effects on torque output values, and increased loss from iron loss, etc., can be evaluated
Iron loss density distribution (left: without degradation; right: with degradation)
Torque comparison with and without production degradation
Iron loss comparison with and without production degradation
Table settings screen for “Magnetic Flux Density vs Correction Coefficient”
JMAG Function Videos
* If you cannot access the video, please check here.
Modelling Accounting For Stress
The effects that stress from shrink fitting and press fitting have on machine performance can be accounted for.
- The magnetic properties and iron loss properties of electromagnetic steel sheets with stress dependencies can be used.
Magnetic properties
Iron loss properties
Stress dependent material properties (35A360)
- Both compressive stress and tensile stress are supported.
- Magnetic flux density is divided into each direction component for stress, and then stress for each direction component is accounted for.
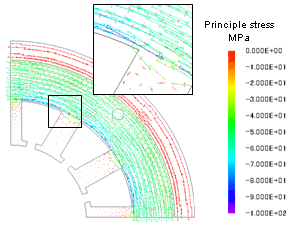
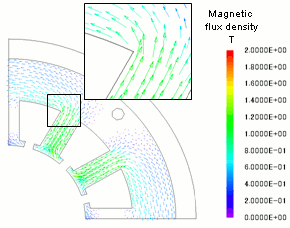
Losses by the tensor method: 3.3(W)
JMAG Function Videos
* If you cannot access the video, please check here.