Since its founding, IMS Co., Ltd. has continued to support advanced technology development of magnetic application products.
IMS Co., Ltd.’s main products are devices to magnetize permanent magnets and the whole process from design, development to manufacturing is all completed in-house. They handle magnetizing yokes (jig used in magnetization) required to create magnets as well as special power supplies. In addition, they also manufacture magnetic field measuring devices that are needed for testing quality and checking what kind of magnetic field is emitted by the magnetized magnet.
The world’s one of a kind measuring device holds promises for synergy with simulation
Our focus is on “magnetization”. Our main product are devices to magnetize permanent magnets. We handle magnetizing yokes (jig used in magnetization) required to create magnets, as well as special power supplies. We also provide automated equipment to reduce workloads in response to user requests.
And one more thing, of course, after magnetization occurs a magnet is created. So, we manufacture magnetic field measuring devices that are needed for testing quality and checking what kind of magnetic field is emitted by the magnet.
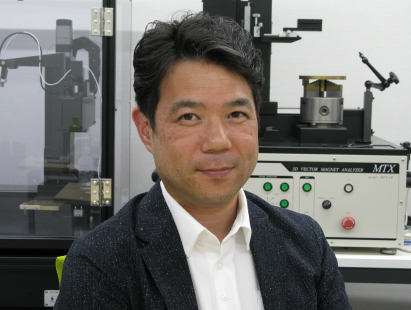
Mr. Yoshino:
Instead of gaining an advantage in cost competition, we want to be a company that makes use of this extremely niche field, and aim to derive value in technology competition.
In fact, in product development, we make sure to only include the unique or the best products to our product line. Our products are created completely in-house from development, design, through to manufacturing by a small but elite product development team that works day to day, making various efforts. We outsource work pieces such as sheet metals, machines and resin, but everything else including board design and software development is conducted within the company.
Mr. Yoshino:
The high accuracy measuring device, the MTX. It can measure 3D magnetic vector distribution. There are similar products, but the sensor is different and the MTX is equipped with the “Magnetic Sensor Automatic Positioning Function” and the “Angle Correction Function”, both of which are patented technology. The MTX is a highly accurate measuring device that competitors cannot match.
You can see the magnetic fields near the magnet by checking the 3D magnetic vector distribution. In other words, you can check whether the 3D magnetic vector distribution obtained from the simulation matches the actual measurements. Only the MTX can do this.
This type of measuring device is essential for checking whether magnetization conditions and simulation results are the same as well as evaluating the actual motor.
Also, in recent years, there are increasingly more position detecting devices that use magnetism such as in car steering and gear shifts. Not only the magnetic strength but the direction becomes important as these devices use magnetic vectors. This is why demand for the MTX has grown drastically in the past 10 years and we receive inquiries from various entities.
Mr. Yoshino:
Yes. If the simulation doesn’t match the measurements of the actual machine, we consider the actual machine to be correct. The reason why analysis doesn’t match is because a physical phenomenon or material property is missing. So, by looking into what to fix in order to obtain results closer to the actual machine, as well as analyzing and verifying the causes, we are able to accumulate simulation know-how. Our strengths lie in being able to make modifications that enable obtaining analysis results that are close to the measurements of actual machines by gradually raising the level of simulation accuracy.
3D magnetic field mapper MTX Ver. 6
* If you cannot access the video, please check here.
Passing on experience-based technology, and finding new ideas
Mr. Yoshino:
Magnetization is a dangerous process that involves applying high currents in a short time and generating high magnetic fields. We have learned that this work involves such dangers from our predecessors through their experience. Like traditional performing Japanese arts, there are no numbers or equations. We simply succeeded what our predecessors learned from experience. In other words, our know-how was merely based on “for this, we can probably do this” sort of trial and error experience. I learned about magnetizing yoke from making a lot of mistakes.
Quantifying this experience with the power of science is a great benefit. Simulation confirmed that what we thought was the “better way” is actually “the right way”. We were able to quantify that our experience is “correct” and pass it down to younger generations.
It is extremely difficult to teach magnetizing yoke design. For example, in the past, when asked about the number of turns for a coil, “why is it 3 turns instead of 2?” or “why can’t it be 4 turns?”, all we could do was take a quick look and say “let’s do 3 turns because 2 turns seem too weak” based on experience. But now, we can analyze the results using 2 turns, 3 turns, 4 turns and decide which is the best by comparing numerical values. It is definitely easier to explain now.
Of course, we can take 3D measurements because we have the MTX. Until now, we were also using the 3D measurement data of magnetizing yoke as reference for designing the next yoke. This only accumulates personal experience while on the other hand, compiling simulation data enables us to share experience to a great advantage. Also, once you get used to simulation, you can create new shapes from trial and error. Working with simulation may be more efficient and helps gain experience. The biggest difference is that back when I started, I had to actually create to gain experience, whereas now, experience can be gained by running an analysis.
Comparison of analysis results and actual measurement (radial direction component/3-axis combined value/vector)
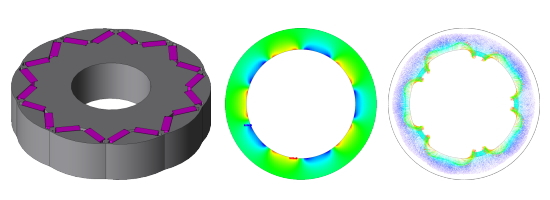
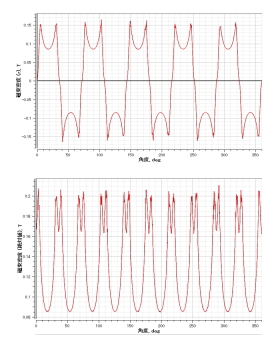
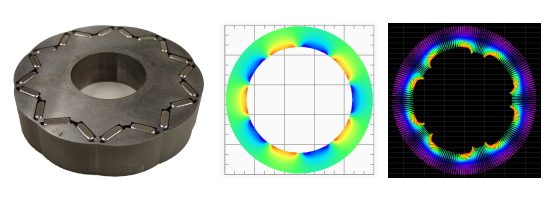
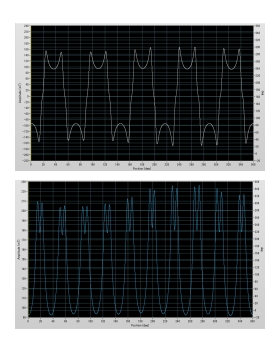
Improved from current product
Mr. Yoshino:
The disadvantage would be becoming a person that can’t create anything without analysis. In addition, I’m afraid that we would assume that all analyses are right.
The results of a simulation analysis would come out all wrong unless correct values are input at the beginning. An experienced person may realize that a certain analysis result is not right, but I often see cases where less experienced people can’t see that and let it go. There were times when we took the analysis result for granted and convinced a client into giving us a job, but when we tried to magnetize, it didn’t work. When we looked back on what may have caused the problem, we found that the values that were input were incorrect. If you don’t have the experience, you just don’t notice that there is something wrong with an analysis result, in the same way as an experienced person.
Having an analysis function boosts confidence in younger people. If magnetization doesn’t work in a design that they created, they would feel responsible. I think it helps to be able to run an analysis to check that your design works. Running an analysis and seeing that it turned out OK helps encourage further development. Also when you have an idea, having analysis prove that it will work is an incentive to try to create magnetizing yokes. Until now, we were not able to make actual prototypes even when we came up with an idea because of the costs.
Mr. Yoshino:
In the past when experience used to count, we made 10 types or even 20 types of magnetizing yokes and selected the best one for mass production. This however, could be done because those yokes were small and we were able to make them for a few tens of thousands of yen.
But now, small motors are mostly made overseas and the motors made in Japan are all expensive. Servo motors, traction motors used in cars and high performance motors for robots are large and a single magnetizing yoke may cost from hundreds of thousands of yen to several million yen. Making several prototypes is just not possible anymore, not at this cost. You only have one shot, so we need to make various patterns with analysis and offer the best one. It has been a great step forward for the marketing group to be able to show the results of our studies.
Overcoming difficulties and taking on new challenges
The support staff patiently helped us from the beginning to create a magnetizing yoke model all the way through to generating the magnetic field. Creating a 2D model didn’t take time, but we were not satisfied with magnetization analysis in 2D and had to try a 3D transient analysis. Trying to match the results of this 3D transient analysis and the actual machine was a tough challenge. We couldn’t match the calculation of the current value connected to the magnetization power source and repeated the process of running various experiments and evaluating them. In the end we were able to establish our own analysis method and all our efforts were worth it.
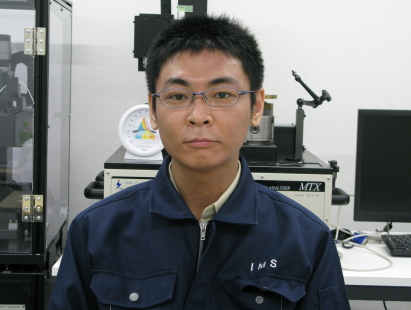
Mr. Iwase:
Well, we made various inquiries and the support staff gave us answers in detail. We also look at the technical reference documents from time to time. We use it as reference and when that doesn’t help, we try to find answers on our own. When that doesn’t work, we consult with the support staff and change the way we are going about it and keep repeating this process.
Mr. Yoshino:
Magnetization is a field that is worked on in extreme conditions. JMAG has 2 or less tesla of material data, but in actual situations there are 8 tesla or even 10 tesla units of data and we are not sure whether to use linear property in the measurement range. The eddy current not matching is also an issue.
A magnetic field exactly the same as the analysis was obtained when placing a magnetic measuring device where the magnet enters and measuring the actual strength of magnetic field. However, the magnet did not saturate even though it should have at that level of magnetic field strength. The only reason we could think of was that an eddy current occurred in the magnet creating a demagnetization field that shielded magnetization of the magnetic field. To confirm this, we experimented by taking measures to prevent any eddy current from occurring in the magnet and it magnetized successfully. In other words, experiment results show that the eddy current was the cause of the problem but the same situation cannot be reproduced in an analysis. We intend to continue to follow up on this, but we also feel that it is important to acknowledge that there is a gap between measurements in an actual machine and simulation results. We need to leave it at that since we can’t spend too much time on it and need to focus on securing constant profits.
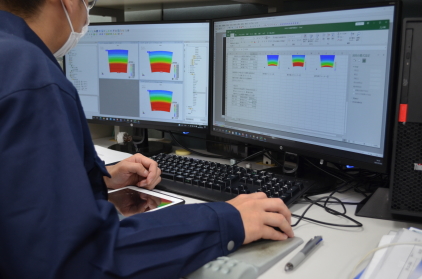
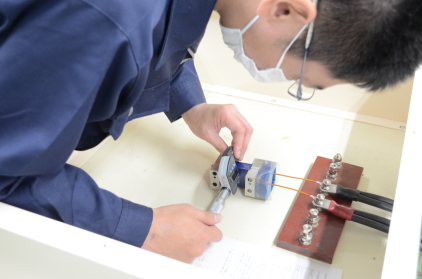
Changing the subject, how do you educate your employees on JMAG?
Mr. Yoshino, Mr. Iwase:
We have an in-house tutorial that we made which is used together with OJT.
Mr. Yoshino:
JMAG has too many functions to remember. (Ha ha!) Even now when we become anxious and are not sure if the number of turns and resistance values of the coil is the same as the number of turns that is input in the circuit or if it is for a full model, we use a model that enables quick and easy calculation and check it out by running both a full model and partial model analysis.
Mr. Yoshino:
We are right in the midst of trying to solve the issue of the magnetizing yoke breaking. Due to its specifications, a magnetizing yoke inevitably breaks, but we don’t want it to break easily.
A tremendous magnetic field is created causing massive currents to flow and several hundred newtons of instantaneous force hits the wire. Resin material is molded around the wire to control displacement/deformation and we want to quantify the data on the preferred thickness of the resin instead of using a rule of thumb. Since it is difficult to measure instantaneous Lorentz force, we want to analyze the Lorentz force with JMAG and evaluate whether the resin will break or not by replicating the same force in an experiment.
We also want to use thermal analysis, although this may be difficult, using only JMAG. The temperature of the magnetizing yoke goes up in dozens of degrees instantaneously as if running a heat cycle test. If this causes the resin to deteriorate and the electric wire moves, the insulation breaks down. We want to create a magnetizing yoke that doesn’t break and hope to make use of JMAG in the process.
Taking on such new challenges is what makes our company one of the best.
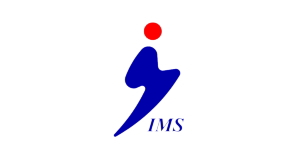
Design, manufacturing and sales of various production machines
Design, manufacturing and sales of various measurement devices and testing equipment
Other design and manufacturing of various devices according to user needs
You need to sign in as a Regular JMAG Software User (paid user) or JMAG WEB MEMBER (free membership).
By registering as a JMAG WEB MEMBER, you can browse technical materials and other member-only contents for free.
If you are not registered, click the “Create an Account” button.
Create an Account Sign in