Virtual Prototyping in Developing Next Generation Heavy Equipment
644k Hybrid Tractor
https://www.deere.com/en/loaders/wheel-loaders/mid-size-wheel-loaders/
In this issue we’ll learn a little more about John Deere. John Deere has been aggressively pursuing electrification of their vehicles to increase productivity and reduce operating cost. Electrification projects range from adding small electrical motors to improve cabin comfort to creating a hybrid drive system by incorporating traction motors. There are many benefits to electrifying heavy machinery. Besides the obvious reduction in fuel consumption and improvement in ride quality, you can also improve tire life through active traction control in a hybrid tractor. As you would imagine, replacing tires on a wheel loader is a costly repair! And plans to continue development of electric machines. Tetsuo Ogawa recently sat down with Jim Shoemaker to learn more about what John Deere is doing and how they are using JMAG.
Electrification of Heavy equipment
Mr. Shoemaker
John Deere is moving into electrification and many of our new products now have electric drives. (See story on 644k Hybrid Tractor above, or add image/reference to newer model) We are also a company that is very much moving towards virtual prototyping so we are trying to remove as many vehicle prototype builds as we can. We would like to design it, simulate it, build the first mule (prototype), prove it and run it, all while reducing the number of prototypes. So we are simulating everything, mechanical, electrical, hydraulic, etc.
Mr. Shoemaker
We typically purchased motors from suppliers based on specifications and performance data. We would build a test rig and run it on a dynamometer to verify that it met the specifications needed for the application including thermal and structural performance. So we always had to physically verify that the machines we purchased met our requirements.
Mr. Shoemaker
Mostly we tried to find available machines from suppliers. We did calculations based on geometry to try to understand machine performance but it was all Maxwell’s equations used to estimate what we thought would meet our requirements.
Mr. Shoemaker
That’s true. Commercially available machines do not have the power or torque density we require in our applications. For example, think about how large a 500 Watt bench grinder motor might be at your home. We need a 500 Watt continuous duty motor to be about the size of your fist. Even a high performance servo motor is 2 or 3 times larger than motors on our products. John Deere requires much higher power and torque density from smaller machines. And the machines need to be sealed from water, dirt, fertilizer salts, and survive a lot of abuse. Our suppliers were not able to provide that with their catalog offerings.
High fidelity model in virtual prototyping
Mr. Shoemaker
SPEED gives us a great performance prediction quickly. I can predict that the motor would put out 100 KW of power but SPEED is not a really good tool for digging deep into the losses. SPEED may predict 93-96% efficiency and the mechanical guys will ask what coolant flow rate is needed to cool the motor. That efficiency range represents nearly a factor of 2 in terms of having to reject 4KW or 7KW of heat. So the mechanical guys think my modeling is no better than a guess. They could throw darts in the dark and get better results in their opinion. Machine output is still about 100kW either way, so that’s predicted pretty well, but how much heat I need to reject is where we are not sure. What is the exact efficiency, what is the torque ripple of that machine, how is it impacted by manufacturing tolerances, current or voltage tolerances, what can I expect out of the machine when these quantities are changed That’s where we need to get a much better understanding.
Mr. Shoemaker
The first motivation was to get better performance understanding in terms of torque ripple, dynamic response, etc. The second was to get better understanding of the losses and controllability like adding one more turn into the machine gets you a little less current but do you have the voltage headroom to maintain dynamic control The answers we got from SPEED were not as accurate as we needed. We still use SPEED for initial calculation to get a basic idea for sizing the motor and performance. I would always go there first before I start doing an evaluation of something just to get a feel for it.
Core loss and magnet loss
Impact of current harmonics (PWM) on loss and efficiency prediction
Frequency component of Joule loss
Mr. Shoemaker
I think it is as good as the other electromagnetic FEA packages, but I guess we don’t re-evaluate simulation tools very often because of the big time investment in learning a tool. To me JMAG is missing a multi-physics connectivity. (Editor’s Note, JMAG has recently added a Small Multi-Physics feature to do just that and we are planning to expand these capabilities) I want to be able to sit tight and run all analysis domains, like some of the other software packages do. I like the fact that we have the ear of JMAG. For example if I say I need a flux calculator, within a period of 3 months we have a flux calculator. I don’t have that with other FEA suppliers. We have to accept what they send out. If I have trouble with my bus bar calculation, I can send it to JMAG and say “here JMAG, show me how this works” and you will figure it out.
Mr. Shoemaker
Before simulation tools we would evaluate about 2 cases in 6 months. It is a lot of work to run machines on a dyno: providing adapter flange, shaft coupling, alignment, coolant, position sensor adaptation, configuring an inverter to properly operate an IPM machine and evaluate it through all its range, over temperature, saturation, short circuit, etc. Now I can evaluate about 50 in a week! We use SPEED to compare induction, IPM, and SR machines for an application and find a few worth investigating. We can compare single layers of magnets to dual layers of magnets, and multiple magnet angles and positions, and then select the cases that we want to do a deeper dive on.
Different rotor configuration study
Mr. Shoemaker
First week I do a cursory evaluation of multiple cases and the next week I probably take 2 of them and take a deeper look using FEA and then I come up with what I think is about what I want. Then I work with the controls and application trying to see if this really performs as I need it to.
Advanced design for control systems
John Deere is also developing custom controllers for their machines. This is done by a separate group within John Deere called John Deere Electronic Solutions (JDES). Jim’s group is responsible for the machine design and they have to communicate this design with the control team to allow them to simulate system performance. To do this, John Deere relies on JMAG-RT. JMAG RT allows Jim’s team to create a high fidelity machine model and send the information as a block that can be used in their HIL system.
Mr. Shoemaker
We are using it in a HIL system to characterize a controller for an IPM electric machine without putting the electric machine on the dynamometer. If we have accurate geometry and material data then we can accurately characterize the machine. We map the machine for maximum torque per amp, maximum efficiency, no load and full load conditions.
The other advantage with virtual tools is that you can run machines to the limits or past the limits without damaging hardware. You haven’t burned up a motor or an inverter.
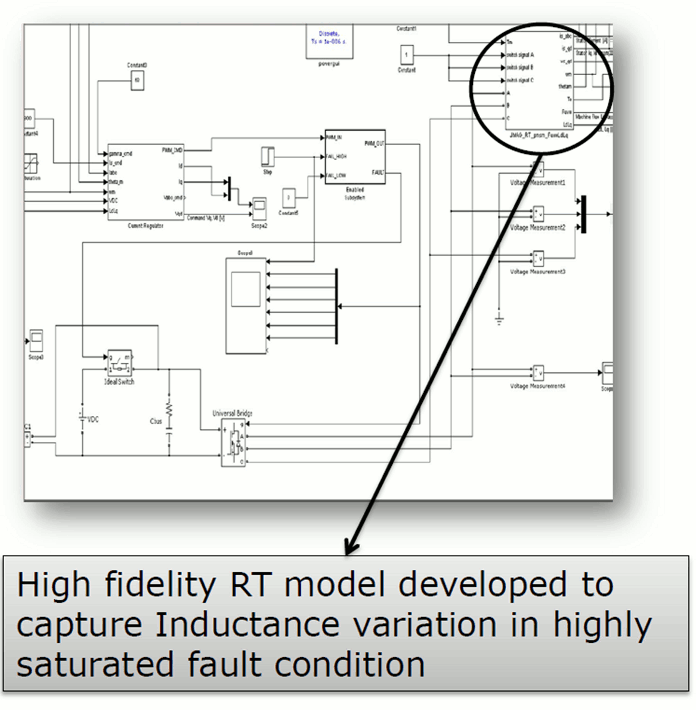
Integrated control simulation for fault mitigation
Advanced support and technical materials to accelerate the learning curve
Mr. Shoemaker
I think the support is superior to other FEA companies we have worked with. It’s still never of course what I want. I want you to anticipate my needs, read my thoughts and whenever I ask you for something get it the next day. But of course it takes time to do things and the support really is quite good.
Mr. Shoemaker
I always like tools like that. The output from the User’s Conference is also a good source. We go online and we read or download the files. It is always good to get other user experiences. Your tutorials online are very good too. They walk through most of the things everybody wants.
Mr. Shoemaker
It does. Either for someone new to JMAG altogether or just someone who wants to run a new tool or feature. We can run the example and have one that works which lets us identify any issues and confirm whether an issue is related to the tool integration or the problem set up.
Mr. Shoemaker
Absolutely. Virtual prototyping is absolutely cost effective.
Expectation to advanced modeling with multi-physics
Mr. Shoemaker
The big push for us right now is thermal modeling. I can very accurately calculate the torque and speed of an electric machine. I can sort of accurately calculate my losses. It’s not as good but it’s ok. I don’t have a clue how hot my motor will get. What power level can I run that motor to before I reach a 180o C hot spot in the center of the motor I don’t have a good idea and I can be off by a factor of 2 even using JMAG and anything else because we just don’t have a good tool that really predicts temperature that well. We are pretty good at predicting the performance, ok at losses but terrible at predicting thermal.
Mr. Shoemaker
I am not so sure that I know that answer. Again bringing in more data to predict thermal performance better, just like you have imported the JFE steels, you brought that database in, that’s not a feature in JMAG. It’s just a database of steels but without it you can’t get accurate results. The same thing is true for the thermal performance. You have tools that if you have a good estimate for all of the thermal impedances and capacitances you should be able to calculate performance, but we don’t know all those things. We are not very good at getting from copper to slot liner to steel to water jacket, or knowing how well the coolant couples to the heated surfaces.
Mr. Shoemaker
Yes. That’s our next threshold. We have some variable length motors and if we need more torque, we make the motor longer. We cool these motors by running oil into a jacket around the stator and also spray oil on the end turns. Once the motor gets about so long I can’t thermally cool the windings at the center of the lamination stack. My question would be where do I hit the limit And if change the oil temperature or flow rate, what is the possible length now If I put more oil on the end turns does it help or is there so much differential across the steel it doesn’t matter That’s where our next frontier is. Getting this differential of how fast the heat flows through the copper to the ends and how well heat is removed. I guess it is a multi-physics problem but that’s where I am at.
Mr. Shoemaker
Yes. Even if the tool is good if the material information is not provided, the user would not know where the materials saturate or how they behave. All those things that come into using the tool are what we are lacking in thermal.
Mr. Shoemaker
Yes. It is not a built-in knowledge-base for the tool now. It’s just best guesses or at least an approximation that works. It is also a part of the request to the JMAG team.
This has been a theme we have heard from many of our users. We need to incorporate knowledge into JMAG’s functionality. We have been working toward this, but additional feedback is always appreciated!
Interviewee
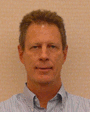
Jim Shoemaker
Technologies
Mgr Vehicle Electrification
Advanced Product Technology
John Deere
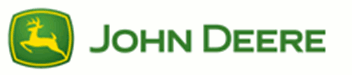
One John Deere Place
Moline, Illinois 61265
[JMAG Newsletter March, 2014]