Using Simulation to Support Automobile Evolution
– JMAG, the de facto tool that anticipates the widespread use of electrical devices –
Automobiles have been made more environmentally friendly by taking advantage of electricity from cars that consume fossil fuels. These days, cars are undergoing further evolution. A key to these is held by the category of new technologies known as electric devices, with the core part being the motor. Processes have been established to make simulation technology more versatile for more effective development. Mazda is gradually and reliably making preparations for the future by creating scenarios for the evolution of its own cars. JMAG also plays an important role in the area of cutting-edge innovation.
The Building-Block Strategy and SKYACTIV TECHNOLOGY. Mazda’s View of the Future
Mr. Yonemori
Innovation means “to make something for the first time,” and our section is truly involved with activities that create new technologies, not based on anything from the past. For example, we very freely think of ideas that may be possible in the future, like how motors could change if a combination of materials that has not been thought of until now allowed a new magnet to be invented that would produce several times the magnetic properties at a fraction of the cost, and then we investigate how overall systems would be structured as groups of technologies to support these becoming reality. I like to say, “Use your own ability to carve out your own future, and then go and get it.”
Mr. Yonemori
Before I tell you about that, you need to understand the cars that Mazda is working on making now.
Mazda came up with the “Sustainable Zoom-Zoom” vision in March, 2007. This proclaims Mazda’s commitment to making a sustainable future a reality in which cars, people, and the earth can continue to coexist happily. Based on that, in June, 2008, the “plan to raise the average fuel economy of Mazda vehicles sold worldwide by 30% compared with 2008 levels by 2015” was drawn up. Our strategy for making this a reality is what we call the “Building-Block Strategy.”
In recent years, hybrid cars, electric cars, and other cars incorporating new electric devices have appeared on the market, and these vehicles’ performance can be said to be the combined power of the electric devices and previous technologies related to the engine, transmission, body, chassis, etc. Sometimes the media seems to rather hastily talk as though a complete shift to hybrid and electric cars is a foregone conclusion.
At Mazda, though, we expect that the proportion and role taken by the internal combustion engine in automobile powertrains will still be as big in 2020 as it has been in the past. The areas where there is a combination of internal combustion engines and electric devices will be expanded, so we don’t think there is only value in electric devices. This is why we have adopted the “Building-Block Strategy,” which emphasizes improvements in the “base technologies” responsible for cars’ basic performance, while also incrementally combining electric devices such as regenerative braking and hybrid systems.
Fig. 1 Building-Block Strategy
Mr. Yonemori
That’s right. When you improve the efficiency of the base internal combustion engine, the balance of the electric devices added to it when making a hybrid necessarily changes. By striking the right balance, we’re trying to make cars that provide both the pleasure of driving that Mazda is known for and excellent environmental performance.
Our name for all of the innovative next-generation technologies we are researching and developing to make this happen is “SKYACTIV TECHNOLOGY.” Going back to the fall of 2010, when the new Demio was put on the market including the “SKYACTIV-G,” the world’s first mass-produced engine to reach a compression ratio of 14.0, we’ve gotten positive attention with our 2012 introduction of the CX-5 and Atenza with full SKYACTIV integration.
Although complete devotion to hybrid- and electric-car scenarios is becoming the norm, we’ve used our own strengths to show that there is still room for improvement in internal combustion engines. This is just my own opinion, but I think it can at least raise questions about development trends in the automobile industry.
JMAG: Supporting MBD, the New Current in Development
Mr. Yonemori
I can’t give many specifics, but I’m mainly involved with research on wide-range drive motors for cars and functional integration systems. It’s OK to move forward with investigations of various topics in a very free way because we cannot see the future shape of the things we are looking at, but we also have to have a kind of “basic premise.”
In automobile development, all of the related engineers (this crosses company barriers, so the idea is that these are people who are experts in each field) pile up an unbelievable amount of debate and trial-and-error while forming the essence, or concept, of a new car model. Before building a prototype, the better ability you have to accurately preview the final product, the more quickly and efficiently you are able to pick out any problem areas, and then fix them before they can spread any further. That’s where CAE comes in and helps make it possible to some degree to get a clearer image. Recently, the development process called MBD (Model Based Development) has been implemented, and simulation is also rapidly becoming the mainstream.
MBD is one methodology for pursuing limit design for customers. Cars from recent years, for example the representative hybrids, have a nonlinear power plant with an internal combustion engine, motor, and brakes that work together in a complicated way. At times, ON/OFF operations are discontinuous, and managing torque smoothly with overall coordination is actually an extremely advanced ability. In addition, all of the many performance indices have to be met, including “high performance,” “small size / lightweight,” “low cost,” “controllability,” “extremely quiet / low vibration,” and “high quality / long life / heat resistance.” Because of all this, if you can become expert in getting an accurate grasp of behavior models that express the dynamic properties of different systems in advance, you can more quickly get that much closer to drawing out a machine’s potential, and come that much closer to the system your customers are looking for.
Fig. 2 Concept design
Fig. 3 Unit development
Mr. Yonemori
Refined dynamics is one of the important indices for cars, but it is not enough to simply have a lot of torque with low variation. For the way torque is produced, we have many years of experience that tell us that “this kind of torque production feels better,” and our research aims at making that happen. For example, people who have ridden a motorcycle will understand that the “thump thump thump” of the torque undulations in a V engine feels really exciting, while a single-cylinder engine makes a sort of gratifying “tap tap tap” sound, and each has its own particular merit. In the car world, the ideal would be to be able to know the sensory relationship between the accelerator and brake pedals and torque (acceleration / deceleration g-forces) production, or between steering angle and turning g-forces. If you can even just have complete knowledge of the internal variation components unique to the electrical field, and if it has excellent operability, then you can get to the ideal by the shortest route.
Mr. Yonemori
I’m preparing my own report on our use of JMAG-RT in MBD for electric-drive vehicles.
In analysis of electric-drive vehicle motor drive systems, it is usual to narrow down to easily-calculated ideal conditions and discuss their relative merits and demerits in terms of representative properties like maximum motor performance. But this is limited to only one of the object’s properties. Actual motors are affected by variations in the battery voltage and overheating of internal parts, so that even if they come from the same design drawing, each motor has its own individual character, to put it a bit strongly. Also, in JMAG itself, it is not possible to rigorously express the interactions between the operating environment, changes in efficiency, and others with the motor connected to its surrounding systems. So, with our goal of a “limit design for a dynamic system,” we used JMAG-RT to build a high-speed calculation environment that can get an overall view of the interactions and trade-offs within a system all at once.
Fig. 4 MDMDS system
Kei Yonemori, Technical Research Center, Mazda Motor Corporation
“A Case Example of JMAG-RT Application in an Electrical Automotive MBD”
Excerpted from presentation materials from JMAG Users Conference 2011
Mr. Yonemori
Detailed desktop test reports for all designs are now created automatically, and we can get complete knowledge of limit-design cases in which existing technologies are used to their maximum potential with full automation. For example, with an original design whose properties we have already obtained, we will apply an algorithm from game theory to attempt to improve its properties even further, and let the computers run a huge, 24-hour nonstop trial-and-error session on it. Further, we can add in experiment-design algorithms, make clear which factors are in high correlation using the least number of studies, and run various simulations focusing on the factors with the highest contribution to motor properties. Even further, we try making use of genetic algorithms to try out mutation-like combinations that would not normally be thought of, to see if they lead to technological breakthroughs.
Our attempts to improve the dynamic limits of the system’s performance include (multiple) visualizations of heat behavior inside the system, visualizations of the relationship with battery voltage reductions during full acceleration, and use of computers to find patterns of shared aspects in groups of superior designs. We’re involved in a wide variety of efforts, but we actually keep a basic policy of complete automation for the calculation itself because we don’t want to place too much emphasis on manpower. Even the most powerful computer in the world can’t look analytically at sets of calculation results or apply good ideas from outside the model space. Our slogan for these efforts is, “Let engineers do what only humans can do, and leave large-scale operations up to the machines.”
JMAG: Becoming a “Common Language” for Motor Development in the Automotive World
Mr. Yonemori
My research center implemented JMAG in 2006, and I’ve gradually used it more and more since then. Not only the center, but also the development and design departments use it.
We chose it because it’s the de facto standard for electromagnetic field analysis simulation software in Japan. Like in MBD, the job of an engineer is not done when the calculation results are received. In fact, that’s where the discussion begins. The major goal is to share those results with other departments and with development specialists at collaborating companies, and quickly improve research and development efficiency before moving on to actual machine production, where improvisation will not work.
That being the case, if people are speaking a different language, work efficiency cannot be improved. I think that its being the de facto has a profound meaning in today’s development environment. For analysis of motors for electric-drive vehicles in particular, electric manufacturers also use JMAG, so it doesn’t make sense to use a solution other than JMAG, and changing between tools would require work that is not directly connected to (is not necessary for) car makers’ basic work.
Mr. Yonemori
As for Japanese permanent magnet motors, I know that the best authorized knowledge from the specialized field is already included, so I have no problems there. Also, the staff has responded very generously even to proposals for utilization from my company, so when we have had problems, I don’t remember there ever being any delays since the time we implemented it. It’s also very helpful that new features are developed in response to requests from the places that are using JMAG.
Because of this, even departments within my company that would not have been expected to do so have started to use JMAG, and it is coming to play an even bigger role as a “common language.”
Mr. Yonemori
I think there are a lot of different reasons why JMAG has become the de facto in Japan and is used as a common language among Japanese automakers. I’ve heard that in the beginning, a lot of hard work went into turning research results from university into a reality with this package.
In any case, I personally am willing to say that JMAG can be used as one yardstick for determining a motor’s evolution or its suitability, and that JMAG-RT can be used to provide a lot of technical proposals with dynamic models. I’m not just trying to stick up for JSOL, but having a common language is really very useful.
A Tool for Making Beautiful Automotive Electric Devices
Mr. Yonemori
If you compare CAE results and actual prototypes, you can get really excellent analysis results for each individual analysis topic. But personally, I would like to be able to get more advanced multiphysics analysis results.
First would be to “investigate from different angles” (not available up to now), which would show, by confidence interval, what kind of effect inconsistencies between design drawing data (with manufacturing tolerance) and the actual machine would have on properties such as power and torque. Secondly, JMAG is motor electromagnetic field analysis software, but it would be nice if it could coordinate more with other FEM solution tools, such as those for thermo-hydrodynamics, to expand its range. Thirdly, I wonder if it could be made possible to create direct, coordinated processes from research simulation to production simulation by passing virtual simulation data to departments in charge of production processes, where the experts in manufacturing are.
The ultimate ideal would be that, within the high-speed cycle of research and development, the experts from each field would push each other to have enthusiastic debates about refining design drawings from their own standpoints. To achieve this, designs have to be sent out in a form that is polished up the way designers want it to be, and received by the manufacturing department where later processing can be done. (This in itself is not bad as a general idea.) However, when a production line is actually created, you don’t want any places where you later realize, “we should have done it this way,” for example at the level of it being difficult to change a die.
Mr. Yonemori
Automobile development already looks at what feels good to people from an engineering perspective, and now is the time to actually incorporate that into designs. Simulation of the changes that result from different materials and others, with free use of 3D CAD, is progressing on the one hand. But now we have arrived at a time when we have to think about directly connecting simulation results with actual production systems and incorporating that kind of data into overall design technologies, with JMAG being one part of that.
Specifically, I’d like to see not only motors but everything up to and including inverters fall within JMAG’s application range. That’s because in today’s world of automobile drive, there are no more motors that don’t have inverters. (Batteries fall within the realm of chemical reactions, so JMAG doesn’t have to keep up with them.) I’d also like it to move more into total system control. Accounting for heat is an absolutely necessary function. There’s no fixed pattern for how JMAG should deal with cooling systems or car bodies in expanding its functionality, and I’m sure it’s an area of great concern for JSOL, but I just wanted to bring up my own hopes.
Mr. Yonemori
I mentioned some of my own wishes, but I don’t think JMAG’s role as an indispensable research and development tool will change at all. Cars will continue to evolve to meet customers’ wishes, and it’s easy to imagine that the relative importance of different functions and parts will constantly change within the process of forms becoming more diverse and then being narrowed down over and over. What the future holds is always fluid and fundamentally uncertain. Also, it’s not like things are necessarily made more secure just be becoming more high-tech. This is exactly why the importance of getting a clear image of more visions of the future becomes more and more important, and simulation will play a larger and larger role as it becomes more advanced and more accurate.
There are many different electric devices, from the traditional rotating machines used in auto development such as starters and alternators to today’s traction motors and electric superchargers, and even injectors and so on beyond rotating machines, so that even though cars have a development history of a hundred years, progress has never stopped. Just like with the internal combustion engine, innovations are being made by engineers’ ceaseless hard work and imagination, and there is still room for more progress.
If today’s engines are likened to “works of art” created with a master craftsman’s many cutting tools, electric devices, with their short history of refinement, are more at the level of rough-hewn pieces made by cutting up a tree with a chainsaw. I realize that this is of course only my own opinion, but I haven’t yet seen or produced any motor that was so beautiful it made me feel like sighing.
I think that fully drawing out the hidden potential of electromagnetic materials like iron, copper, and magnets is like eliminating “wasteful things” that interrupt airflow through streamlining or propellers on an airplane. I hope that JMAG will continue to be sharpened as a tool that will allow progress toward products with their functions refined into beautiful forms. We should work together to apply ourselves to a “The SKY is the Limit” development spirit, and move toward a future where we can fulfill all of our customers’ wishes.
We always do our best to grapple with customers’ requests and problems, but we sometimes worry, “is JMAG truly useful for our customers?”
For this reason, we are extremely glad to be shown a customer’s estimation in tangible form such as this Certificate of Appreciation. We would like to use this space to express our gratitude. Thank you very much.
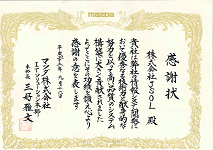
Interviewee
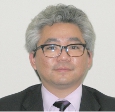
Mazda Motor Corporation
Innovative Research Planning Field
Innovative Research Team and Advanced Vehicle System Research Field
Integrated Vehicle Control Research Senior Technical Specialist
Mr. Kei Yonemori
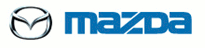
We are the only company in the world with 40 years of experience in mass production and development of rotary-engine cars. Our brand reputation is particularly high in European countries such as Germany and England, as well as in Australia, and the Mazda 3 (Axela) was the top-selling model by car model in Australia in 2011 and 2012.
Our current company catchphrase is “Zoom-Zoom.”
[JMAG Newsletter July, 2013]