解説:モデルベース開発
先回は開発現場において採用され始めている”モデルベース開発(MBD)”に対するJMAGの基本的な取り組み方についてご説明しました。
今回は7月13日にリリースした、JMAG-Designer Ver.10.5のMBD向け新機能についてご紹介させて頂きます。
新バージョンで目指したもの
JMAGは常にMBDを意識して開発しています。MBDのポイントはモデルの精度が高く挙動が本物に近く、且つ利用が容易なモデルであることです。現在、JMAGでは2つの取り組みを行っています。
- JMAG-RTを使ったMBD
- 熱設計、機械設計と磁気設計間におけるMBD
今回のNewsletterでは、1.の多数のプラントで構成されるMBDを意識しているJMAG-RTの新機能に焦点をあててご紹介します。
複数のECUを含むようなシステム開発では、各ECU間の論理整合性や同期速度などが評価されるので、モデル精度とモデルの処理速度、利用容易性が要求されます。こちらを意識しているソリューションがJMAG-RTとなります。センサトラブルや誤操作などあらゆる場面を想定して、システムが正常に動作し、異常処理を行えるかどうかを検証します。システムとしての関連性が完全に確立できているか、起こるべき挙動を実現出来るかを確認します。
モータモデルは鉄損を考慮
何度もご説明しているように、MBDはモデルの精度が重要となっています。PMモータは高効率・高出力で且つ小型軽量化の要求が高まっています。これを実現するために、モータの重量や外寸が大きくなるトルク増大よりも、高回転化して出力を稼ぐ方向に向かっています。これにより、損失における鉄損の比重が以前よりも大幅に増しています。
このような状況で高効率を実現するためには、モータの運転状態に応じて適切な制御を行う必要があります。ハイブリッド車のように、走行状態によってはモータがエンジンに連れまわされるだけの運転モード(高回転低負荷状態)では鉄損が大部分となるので、通常のモータでは使われないような領域での損失を如何に抑えるのかなど、モータ制御の難易度は高まっています。
JMAG-RTのPMモータモデルは材料非線形性や詳細形状の考慮によりモデルの高精度化を実現してきましたが、今回の機能向上で、鉄損特性をモデルに織り込みましたので、更にモデルの精度が向上しました。モータのモデル精度が更に向上したことにより、損失をモータに割り付けるのかインバータに割り付けるのかの判断が精度良く行えるようになり、システム全体の効率化に貢献することが可能になると考えています。
また、今回新しく追加された誘導機モデルでも鉄損特性は考慮されておりますので、線形モデルよりも高精度なシミュレーションを行って頂けます。
また、ビヘイビアモデルには磁石磁束やコイル銅損の温度依存性を考慮する入力端子を追加しました。Simulink側から動作温度を指定することで、モータ特性が変化しますので、システムとしての温度挙動を評価することができます。
JMAG-RTのPMモータモデルならびに誘導機モデルへの鉄損機能追加を担当したエンジニアの成田一行に開発の動機などを聞きました。
Q1.モータモデルに鉄損RT機能を追加した動機は?
A1.RTモデルを使ったシミュレーションで、特に鉄損の影響が大きい高回転域でトルクや電圧が合わないというお客様の御意見がきっかけです。また、モータの温度を推定するために,鉄損の情報も知りたいというご要望もありました。
Q2.今までのRTモデルには何故無かったのでしょうか。技術的に難しかったのでしょうか?
A2.従来から提唱されている並列型等価鉄損抵抗の考え方でモデリングしていますが、従来の並列型等価鉄損抵抗モデルでは、鉄損抵抗での損失の電流や回転数を変えた場合の挙動が、実機の測定結果やJMAGの過渡解析結果の傾向と合わない問題がありました。例えばオープンループの電圧入力でモータを駆動する場合、従来の並列型等価鉄損抵抗では電圧が一定のため、回転数によらず鉄損は一定になってしまいます。実際の永久磁石モータの鉄損を考えるとこれは不自然です。
これらの問題がうまく解決出来ないため実装を見送っていたのですが、JMAGで計算した鉄損の情報を最大限生かすことで、なんとか納得出来るモデリング手法を開発しリリースすることが出来ました。
Q3.実機試験を並行して、モデリング手法を検討されたそうですが、どの様なメリットがありましたか。
A3.例えば、グレードの異なる電磁鋼鈑でモータを作成し、鉄損の違いを実測しました。また、駆動制御方法による鉄損の違いなども評価しました。これらの結果により、鉄損がどの様な挙動を示すかが明確になり、鉄損をモデリングする上で非常に有用な情報が得られました。当然、今回開発したモデル化手法の妥当性を実測で確認できたのも大きいです。
Q4.製品としてまとめる上で苦労したことは?
A4.当たり前ですが、JMAGによる解析で普通に鉄損解析を行った場合に得られる鉄損値とRTモデルが出力するによって鉄損値が合うようにモデリングするのに苦労しました。JMAGのユーザーは要求が高いので、そこは頑張りました。
Q5.製品として出来上がり、実際に使ってみた感想を教えてください?
A5.MBDでの制御シミュレーションで、高回転域でのトルクが過大となったり、基底回転数が合わないといった問題が解消されると思います。また、モータの温度を推定するにも有用だと思いますので、是非ご利用ください。
Q6.今後、更に改善したいところはありますか?
A6.今回のリリースでコア鉄損を考慮するようになったので、モデル精度がかなり向上していると自負していますが、PWM変調や空間高調波による鉄損や磁石で発生する渦電流損は考慮出来ていませんので、今後の課題として改善していきたいと思っています。
誘導機モデル、SRモータモデルの追加
永久磁石モータだけが開発課題ではありません。世界では多くの誘導機が使われています。構造が堅牢で特別な制御をしなくても回すことが出来る、磁石も要らない等様々な強みを誘導機は持っています。勿論、誘導機も効率改善が期待されており、適切な制御を行うことで効率を改善出来ます。特にパワエレ用モータのコントロールマイコンも性能が上がりコストは下がっており、VVVFやベクトル制御により効率を改善するコストも下がっています。このような背景を受けて、JMAG-RTに誘導機モデルを追加しました。PMモータやステッピングモータモデルと同様、JMAGでの磁界解析からビヘイビアモデルを作成しているので、実際の材料特性や磁気回路形状が忠実に再現されます。
また、非磁石モータとして注目されているSRモータのモデルも追加されました。SRMの起源自体は古いのですが、インダクタンス変化が大きく非線形磁化特性が強いため、駆動制御が難しく、トルク変動も大きいため、主流とはなっていませんでした。
SRMの特徴自体には変わりはないのですが、近年の電磁界解析による磁気設計技術の向上と駆動制御技術の向上により、SRMの弱点をカバーしつつ、その能力を引き出せる可能性が出てきているため改めて脚光を浴び始めており、多くのモータ技術者が興味を持っています。JMAGは今回SRMのビヘイビアモデルも追加しました。JMAGの高精度な磁界解析能力により、インダクタンスの非線形性を精度よくモデル化しておりますので、SRM特有の激しい電流変化やトルク変動などを忠実に再現しますので、制御の詳細な検討に貢献することができます。
このように、ユーザーニーズに応えて、今後もモータモデルの精度向上やのバリエーションの拡大を行っていきますのでご期待下さい。
ExpressやテーブルデータからのRTモータモデル作成機能
インバータ設計者の視点からみると、モータはインダクタンスと抵抗と電源の回路に他ならず、スロット形状や磁石の配置は興味の外です。
しかし、RTモータモデルを生成するためには、モータ設計パラメータを決める能力が必要とされ、専門家以外では作ることさえ困難と思われがちです。その問題を解決するのが JMAG-Express です。
JMAG-Expressは簡便にモータモデルを作成して性能を確認することができるので、モータ設計の経験がない方でも簡単にモデルを作成でき、その結果をJMAG-RTモデルとして出力することが可能です。したがって、インバータ設計者の方でもRTモータモデルを簡単に作成できます。
また、インダクタンスやトルクなどの測定データからRTモータモデルを作成する機能もこの度追加しましたので、まさにデータテーブルによるモデル作成を行うことが出来ます。制御設計の評価の為に、モータパラメータを強制的に振るような、形状変更では実現が難しいモータモデルの作成が可能です。
これらの機能追加により、モータ設計者以外の方でもRTモータモデルを簡単に作れるようになりました。
RTモータモデルの価値を共有出来るJMAG-RT Viewer
ここまで、RTモータモデル自体の存在価値について説明してきましたが、お客様より使い勝手が悪いというご指摘もございました。従来のJMAG-RTは制御シミュレーションの速度向上の為に特殊な記述方法を取っていたため、RTモータモデルの性質を垣間見るには、制御シミュレータ上に置く必要があったためです。
この問題を改善するため、この度、RTモータモデル(rttファイル)の情報を見る事ができる JMAG-RT Viewer をご用意いたしました。JMAG-RT Viewerはモータの総合的な特性をよく示す効率マップ(T-N-η特性)やインダクタンスマップ(I-β-Ld/Lq)に加工してモータ特性を表示しますので、制御設計者がモータの特性を概観するのは勿論、モータ設計者自身がモータ特性を確認するのに非常に有用となります。
まとめ
今回はJMAG-RTの新機能を中心にご説明しました。今回の機能追加でJMAGのMBDでの活用範囲は更に広がり、システム開発により貢献できるようになったと自負しています。次回は連成解析機能によるMBDについてご紹介いたします。
dSPACEに聞く
現在、モータを含むパワーエレクトロニクス分野ではモデルベース開発(以下MBD)は本格化しているとはいえませんが、モータをコントロールする上位のECUはかなりの確率でMBDに組み込まれています。JMAGをお使いの皆様も今後はMBD環境に取り込まれていくことを避けることは出来ません。そこで、現在のMBDの最前線について教えていただくため、MBDが最も進んでいる自動車ECUの開発分野へ開発ツールを提供しているdSPACE Japan社技術部部長の宮野様にMBD開発現場の最前線について伺いました。
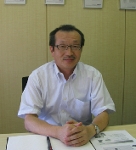
技術部部長
宮野 隆 氏
MBDの状況
先日の東日本大震災で自動車用マイコンの製造メーカが被災して自動車が生産出来なくなった様に、自動車はいまやコンピュータの塊といっても過言ではありません。
自動車はエンジン、変速機、パワーステアリング、ブレーキなどの機関ユニットそれぞれがECUを持っており、エアコンやナビゲーションシステムのような快適ユニットもそれぞれECUを持っており、それぞれが接続されています。それぞれのECUには制御プログラムが搭載されており、そのプログラム総量も膨大となります。ユニット単体での検証は当然として、システムレベルでの検証も必ず行われており、その確認量も膨大となります。
MBDにおけるVサイクル
MBDの最前線
dSPACEでは同じMBDでもモデルベースデザインとモデルベースデベロップメントには大きな違いがあると考えています。「MBデザイン」はいわゆるシミュレーションによる開発で、そこで閉じる場合が多い。一方、「MBディベロップメント」は作成したモデルを次工程で利用していく事が大きく異なります。ソースコード化されたプラントモデルやECU制御モデルが引き継がれていき、最終的には量産品まで繋がっていく。すなわち開発の全ての工程が網羅されるイメージです。dSPACEの製品はMBディベロップメントでお使いいただくために開発されています。MBDは、実機での確認が難しい航空機や兵器の開発にシミュレータの使用から端を発していますが、現在、最も多く使われているのはやはり自動車産業。日本よりも欧州の方が、MBDの導入は進んでいるように見えています。
制御系を設計する場合、制御されるプラント(制御対象)モデルに対して制御する制御器(コントローラ、ECU)モデルを作成、調整していきます。dSPACEが提供しているMBD環境は、ひとつめが制御器モデルを素早く実現する試作ECUである”RCP”です。RCPには小型スタンドアローンのMicroAutoboxや拡張性を持ったRapidProがあります。ふたつめはプラント(被制御対象。モータやアクチュエータ、センサ)を構成する”HILS”です。両者とも実時間にて実制御対象の制御や実時間にてECUの検証を行う事が出来ます。基本はRCPとHILによるリアルタイムシミュレーションで、上流工程で作成したECUの制御モデルから、ECUに載せるCコードで自動生成されるのがポイントです。
MicroAutoboxはECUを充分に再現できる計算能力を持っていますが、パワーエレクトロニクス関係のモデリングや画像認識など、非常にも算能力を必要とする場合はFPGAボードを用いて約10MHz/100(nsec)の制御周期を実現することも可能です(FPGAの基本クロックは100MHz)。
dSPACE HIL (Hardware-in-the-Loop) シミュレーション
MBDでECUと並んで重要なキーであるプラントモデルを磨き上げるのは各ユーザーになります。どの物理系をモデルに取り込み、捨てるかはユーザーの腕の見せ所となります。モデルの妥当性評価はVサイクルを廻すことで明確になります。モデルの精度が不十分な場合、次の工程が進んだ時に思ったようにシステムが動作しないなどの齟齬が出てきます。齟齬の原因がモデルによるものであれば、修正して改めてVサイクルをスタートさせる事になります。
自動車用ECUの場合、ソースコードの1/3はダイアグノーシス(故障診断)の為にあります。センサやECU間の断線やノイズ混入、プラント破損などの故障などの外乱によっても、システム全体として危険なモードに入らないように、制御システムが構築されているかを確認しなければなりません。この確認の為には、色々な故障モードに対して検証する必要が有り、システムが大きくなれば試験数は指数的に増大する為、HILを使った自動テストが効果的です。また当然実ECUをテストする為、リアルタイムでのプラントシミュレーションが必要です。
色々なレクチャーを受ける事で、MBDがECU及びプログラム開発に非常に有用であることは分かりましたが、どちらかというと、プラント設計者に近い筆者としては、相変わらずピンと来ないところがあったので、最後に次のような質問を宮野様にしてみました。
(JMAG)
MBDがECU及びプログラム開発に非常に有用であることは分かりましたが、JMAGユーザーはプラント設計に近く、MBDが導入されてもあまり影響がないように思います。MBD環境はプラント設計者にどの様なメリット、影響があるのでしょうか?
(dSPACE宮野様)
MBDによりプラントに対する要求がより具体化・詳細化します。例えば、”モータのトルク変動は◯.◯(N・m)以下に抑えなければならない”などという指示になります。要求が厳しくなるという面もありますが、システム全体の最適化を図る上での感度や優先順位が明確になるので、各担当が勝手に持っていたマージンなども審らかになるので、プラント設計者には逆に楽になる面もあるかもしれません。システム要求に合わせたコンポーネントの最適設計(オーバースペックの見直しなど)が可能です。
最後の答えで、やっと腑に落ちました。
プラント側と制御側のトレードオフを力関係や声の大小ではなく公平に行えるのであれば、技術者としては望むところと思います。MBDによる開発の効率化は、作業時間の短縮だけでなく情報や判断の共有の方に効果があるのかもしれないと強く思った取材でした。
連絡先: dSPACE Japan株式会社 営業部
TEL: 03-5798-5460
E-mail: info@dspace.jp
[JMAG Newsletter 2011年夏号より]