Established as a venture company originating from the Nagaoka University of Technology to “help people and companies who have problems with motors”
Nagaoka Motor Development Co., Ltd. was established as a university-originated venture company based on the slogan “We want to help people and companies that have problems with motors.” They make use of their high technical skills in responding to customer requests such as providing prototypes of motors/drivers and analysis for developing new motor installed products, as well as for motors that run with greater energy savings and higher performance.
WE WANT TO PROVIDE THE CUSTOMERS “THE TECHNOLOGY THEY WANT” TO HELP WITH THE PROBLEMS THEY HAVE WITH MOTORS.
Mr. Sato:
We are primarily engaged in motor development outsourcing. We mostly receive requests for prototypes of drivers (ECU) that run motors, the motors themselves, and magnetic field analysis.
The design, analysis, and, prototyping of motors and motor design are conducted in-house, as well as the analysis, and, mounting of motor control programs that are written to microcontrollers. However, we outsource hardware such as power conversion circuits and control circuits used in drivers. The drivers are outsourced to a company established by senior members of a research laboratory (Ito Research Laboratory of the Nagaoka University of Technology). The senior members have received a doctorate in the research of circuit design and power supply control. When customers ask for not only the motor but also the driver to be manufactured together, we check and make suggestions on the driver requirements, and then ask the subcontractor to make the product.
I am primarily responsible for electromagnetic design and magnetic field analysis of motor prototypes. These days, although I mostly handle the PM motor, I also handle the SR motor and the synchronous reluctance motor. I believe, there have been more inquiries on synchronous reluctance motors and motors with Halbach-array magnets lately.
Mr. Sato:
As I mentioned earlier, we are basically focused on contracted development in a wide range of fields, from the design and prototyping to the driving of motors. We started the company because we want to help people and companies who are having problems with motors.
For those customers who don’t need high-level technology, what can be easily done is kept simple, and if difficult technology is needed, we work on improving such technology as required.
I think that “we need to have a core technology”, so we are currently refining our automatic design and control technologies for motors. Some of the refined technologies have been presented at academic societies and are open to the public.
IMPROVING TECHNOLOGY IN DESIGN AUTOMATION AND HIGH ACCURACY USING JMAG
Mr. Sato:
In design automation, I believe there is an AI-based approach and an approach that extends from optimization. I am currently working on the latter.
We calculate machine constant from motor specifications and try to obtain highly versatile dimensions and turns through trial and error.
Mr. Sato:
Hmm. I do think about which should have priority, but I believe it is necessary to proceed while balancing the control and the magnetic design of the motor. Many of our customers make strong demands for small sizes, but there is less demand for low vibration and low noise. This is not a matter of ignoring torque ripples, but since low vibration and low noise were considered low priority, we once went ahead with the design and prototyping only to find that the frequency was too high when we tried to control it.
It’s really difficult when the procedures change depending on where priorities are placed.
Mr. Sato:
Although a design that accounts for heat is yet to be established at our company, we are trying to actually create a model to see how accurately the heat can be accounted for at the design phase, using our own study.
BASED ON THE ASSUMPTION THAT “JMAG” IS USED
Mr. Sato:
Hmm. There was no specific cause that prompted me to use JMAG. The biggest reason is that I was already using it, but I’ve always felt that simulation software is essential for this job. When the company was first started, there was no budget for software, so we couldn’t introduce it immediately, but I thought we would do so eventually in the future. I wasn’t worried about using JMAG again because I had been using it during college and wouldn’t have problems with the operations.
In my work, I often meet people who use JMAG or people from companies who use JMAG. The second reason is that when we think about sharing information with such people, it’s better for us to have JMAG instead of other software. If our suppliers also use JMAG, it is better for us to use the same software to enable data exchange.
Mr. Sato:
As I previously mentioned, aside from customer requests, one of the things that we are currently working on is the development of a design automation method for motors. The method is classical. When motor specifications are input, the core dimensions and turns are calculated based on the magnetic circuit, and JMAG is used to check whether the obtained results are correct. I think the design procedure will change depending on the type and shape of the motor, but I believe we have established the design method of the SR motor and IPM motor with a general magnet arrangement to some extent.
The design methodology for SR motors is also summarized in the paper. The SR motor was not the main focus of my studies when I was a student, but SR motors often come up when I talk to customers. So, I decided to design SR motors as a learning experience. Doing some research, I found that the design methods were not easy to understand, so I decided to compile a design method. Just when I started this, a student from Professor Ito’s laboratory at the Nagaoka University of Technology, my alma mater, joined our team as an intern for about 3-4 months, so I asked him/her to work with us. While I worked on this, I was able to obtain the results for writing a paper, which was presented at the Technical Meeting on Rotating Machinery in January 2020.
Mr. Sato:
The ultimate goal was to create a base model to load into JMAG-Designer and JMAG-Express. The flow of determining dimensions was compiled by referring to reference books and papers and summarized in a flow chart. Originally, “The way SR motors should be designed” was written in various papers, and I summarized it all into a flow chart. So the content written in these papers is quite commonly known. The final design plan was validated using JMAG.
The fact that we were able to check validity with JMAG means that the design method is based on the assumption that JMAG software is used. In fact, this design method is not able to design that accurately using only the first calculation. It is a method that can design with high accuracy by analyzing several models using JMAG and reflecting the results.
DESIGN IS A SERIES OF REPETITIONS. SIMULATION IS PARTICULARLY GOOD FOR FACTOR ANALYSIS. FLEXIBLE RESPONSE FOR CUSTOMER MANUFACTURING PROCESS
Mr. Sato:
I think so. For example, when we were designing a synchronous reluctance motor, the paper that we had been referring to said that “doing this would control the torque ripple” or “doing that would increase the torque”, but it wasn’t as effective as we thought it would be even when we tried following the same procedure.
Magnetic flux density contours and magnetic flux lines are very useful in factor analysis when figuring out why results were not achieved. We can easily see that “correcting only a certain part will not necessarily increase the magnetic flux that contributes to the torque”. It was beneficial that we were able to reach a conclusion that the procedures in the reference material and papers were effective under the specified conditions, but were not for the case we were working on.
Mr. Sato:
Right now, we are satisfied with the comparison of the results analyzed by JMAG-Designer and the actual measurements, because the induced voltages and torques are almost the same. I think the problem would be with the evaluation of loss and efficiency. We all know that the evaluation of iron loss and mechanical loss is not because of the software. I think there is a limit to what software can do. This is because it is difficult to take measurements in the first place. At our company, there are very few instances where we have to place priority on efficiency, so I don’t think we need to be so sensitive about the difference between the analysis results and the actual equipment. On the contrary, I think the results match quite well.
Mr. Sato:
Although we run 3D analysis when required, we usually run 2D analysis unless the case involves a structure that requires a 3D analysis or our customers request one. We don’t handle that many cases that require 3D analysis to obtain results.
In our work, it is not always necessary to match the analysis results with the actual measurements, and it is OK as long as we create a prototype that meets the specifications in the end. Since we use JMAG when trying out simulation, for example, we would use a 2D analysis for a model that may incur problems with a 3D analysis. We may often just tell the customer that, “this is why the torque may decrease a little” and we hardly had any further problems. Therefore, in this sense, we don’t think it is necessary to use 3D for motors other than for the axial gap motor.
Mr. Sato:
Regarding SR motors, we haven’t received any requests that required that much. In the first place, many people are aware that SR motors have loud vibration noise and if they were concerned about this, I don’t think they would consider SR motors. Therefore, at the moment, I have never heard of customers making requests for a vibration noise analysis or a design that accounts for vibration noise.
MY THOUGHTS BASED ON MY EXPERIENCE AND USING JMAG SINCE COLLEGE
Mr. Sato:
I’ve been using JMAG since I was a student, so I’ve never really felt any difficulty using it. It was a learning experience, never a struggle.
The biggest challenge in using JMAG may have been learning the features and terminology. I managed by looking up the terms and calling the support desk for assistance. Of course, there were some things that I couldn’t understand even when I had help from the support desk. At that time, if it was a matter of marking or not marking a checkbox, I would see the difference for myself, depending on whether a checkbox was marked or not as well as changing conditions and seeing how that would affect the results. That’s how I learned from experience, but it would be nice to have a glossary.
Mr. Sato:
Yes, I read them often. Many times I look at cases in the application catalog to help me remember how to analyze methods that I used before.
Mr. Sato:
This may be different from what I want to challenge, but when I worked on the design automation I previously mentioned, I thought it would make creating the model simpler if the user-created tool was directly output to the JMAG Express setting file. It would be easier and time-saving to eliminate the need to enter dimensions and other data in JMAG-Express.
I also think it would be nice if we could start up JMAG-Designer without a license. For example, I feel it would be convenient to be able to just check the settings and display the results without executing the solver, for use in making proposals and explanations when on a business trip. Sort of like a viewer.
Your comments will be used as reference for future JMAG developments.
We look forward to continue working with you in the future.
Interviewee
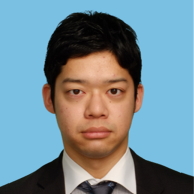
Ph.D. (engineering)
Representative Director
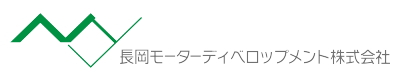
You need to sign in as a Regular JMAG Software User (paid user) or JMAG WEB MEMBER (free membership).
By registering as a JMAG WEB MEMBER, you can browse technical materials and other member-only contents for free.
If you are not registered, click the “Create an Account” button.
Create an Account Sign in