概要

このような高度な要求を満たす設計案を見つけるためには、形状寸法だけでなく、巻線設計も含めた最適化が必要となります。
整数値となる巻数や、規格サイズがある素線径を設計変数に含める場合には離散最適化が有効です。積層鋼板の積厚についても板厚を考慮した最適化が可能となります。これらの変数を連続値として最適化した場合は、最適化計算後に値を設計可能な値に丸めるなど修正して再計算する必要があります。その際、修正により結果が変わってしまい制約条件を満たさなくなってしまうなどの問題が発生します。離散最適化を用いることで目的関数や制約条件を正確に評価した最適化計算を行うことができます。
ここでは、複数の動作点の平均効率の最大化、コストダウンのための体積最小化を目的関数としてIPMモータの形状と巻数の最適化を行った事例を紹介します。
最適化条件
表1に設計変数、表2に目的関数、表3に制約条件、図1に寸法変数を示します。
平均効率は下記の5個の動作点の効率を平均して求めます。
– 1,000 (r/min)、20 (Nm)
– 1,000 (r/min)、300 (Nm)
– 3,000 (r/min)、300 (Nm)
– 4,000 (r/min)、100 (Nm)
– 9,000 (r/min)、20 (Nm)
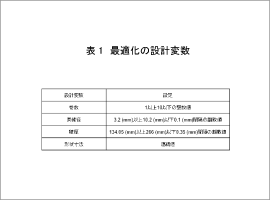
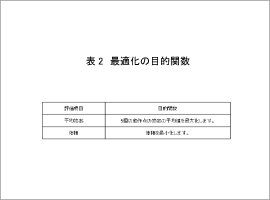
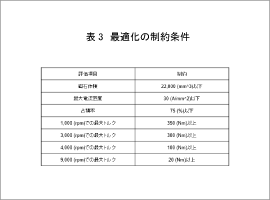
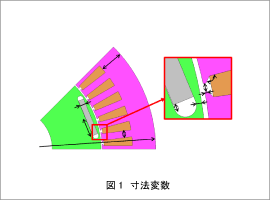
最適化結果
図2に最適化計算で得られた実行可能解の目的関数の分布図、図3に実行可能解の巻数と素線径の分布を示します。比較のために、全ての設計変数を連続値として最適化した場合の結果もプロットしています。図4にパレート解の制約関数の分布、図5に丸め処理によるパレート解の目的関数の変化を示します。連続最適化で得られたパレート解に対して、巻数、素線径、積厚を離散制約を満たすように四捨五入により丸めて再計算した結果も併せてプロットしています。丸め処理によるパレートフロントの変化の例を橙矢印で示しています。図6と表4に初期設計案と離散最適化のパレート解から一つ選んだ設計案の形状と効率マップを示します。
図2、図3より、連続最適化の方がパレートフロントが良化方向に進んでおり、離散最適化の結果は指定通りの離散値に分布していることが分かります。
図4より、丸め処理により制約条件を破ってしまう設計案が多数あります。
図5より、特に高効率側でパレートフロントが後退しており、連続最適化では過大評価が起こっていたことが分かります。また、多くの解が丸め処理により制約条件を満たさなくなってしまったため、得られた実行可能解の数は離散最適化より大幅に少なくなっています。
図6、表4より、最適化により初期設計案より小型かつ平均効率が高い設計案が得られたことが分かります。
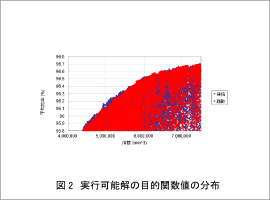
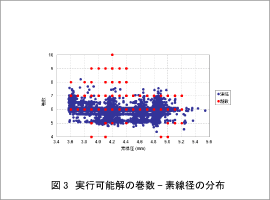
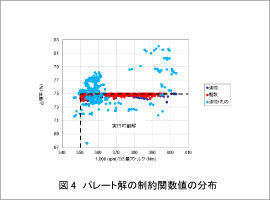
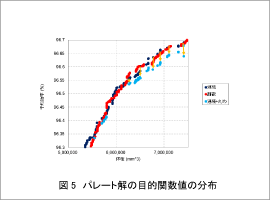
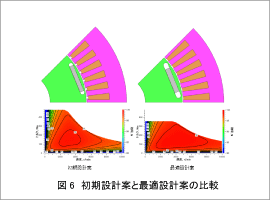
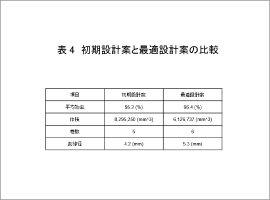