In response to electrification, the Aisin Group is building a system to produce some 4.5 million electric units a year by 2025. The company has set a goal to improve electric mileage by 10% in electric vehicles and is looking ahead to working toward realizing a carbon-neutral society. We spoke with Ms. Okawa, Associate Officer in charge of the Power Train and Electrification Development of the Powertrain Company, the key figure in technology development and production of the “eAxle” traction system for battery electric vehicles (BEVs).
Left: Yasuhiko Tanaka, JSOL Corporation Right: Ms. Akemi Okawa, Aisin Corporation
The Powertrain Company’s Role, Vision, and Challenges Ahead
Mr. Tanaka:
I believe Aisin’s main challenge today is to figure out how to tackle carbon neutrality. Can you tell us about your company’s overall policy on carbon neutrality?
Ms. Okawa:
There is a movement toward carbon neutrality in society as a whole and the automobile industry in particular is said to be undergoing a once-in-a-century transformation. We are managing the company based on the two major pillars of responding to carbon neutrality and shifting to electrification.
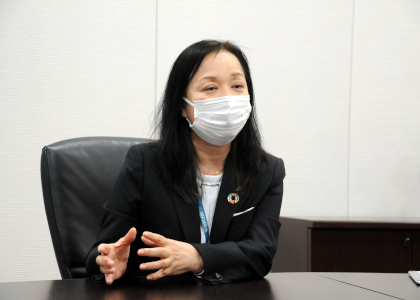
And this year, we established the EV Promotion Center to promote electrification. We restructured the company organization to enable top management to directly oversee the Center so that it is effectively managed and have just started to actively run its operations.
Mr. Tanaka:
Is the Power Train Company managed by the group of people who mainly manage Aisin Corporation and Aisin AW Co., Ltd.?
Ms. Okawa:
Yes. With the merger of Aisin Corporation and Aisin AW Co., Ltd. last year, we have become one big entity. We’ve brought together our workload so the merger hasn’t reduced what we need to do. Rather, we have more to do with the same headcount. Therefore, since the issues we need to tackle are still need to be addressed, we created a special promotion center and are using it to take leadership in putting our forces together and moving in the same direction to work on developing our products.
Mr. Tanaka:
We can see that you are serious.
Ms. Okawa:
Electrification is a major change, particularly for the Powertrain Company. Since the sale of powertrain-related products accounts for a little less than 60% of our entire business, how we maintain this current profit is an extremely important issue. Of course, we will continue our existing AT and CVT business for conventional vehicles, but the biggest issue now is how to successfully shift to electrification.
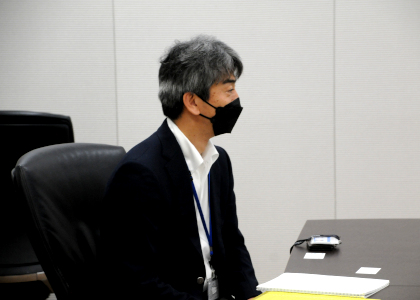
I see. Thank you very much.
You just mentioned that your powertrain products will become the center of your business. Now that Aisin has restructured its business organization and the powertrain business has become one company, can you tell us about the mission and direction of the Powertrain Company as it plays a central role in realizing carbon neutrality?
Ms. Okawa:
First, improving fuel and electric efficiency, including for Hybrids and BEV would be a direct approach to realizing carbon neutrality. In that sense, although we have been producing electrified products, as the President says, our immediate challenge is for the entire company to work together to aim for a 10% improvement in electric mileage by 2025.
The Key to Achieving Our Goal: eAxle and Optimization
Mr. Tanaka:
So, I suppose eAxle would be your main focus.
Ms. Okawa:
Yes, but making a 10% improvement in electric mileage only with eAxle would be difficult. One of the reasons is that eAxle is a system that has already exceeded 90% efficiency. Therefore, what we want to do is improve all of Aisin’s products such as cooperative regenerative braking systems, body products with variable aerodynamic drag, and cooling devices to realize a 10% improvement in electricity consumption with all products combined.
Mr. Tanaka:
I see. I read the Vice President’s presentation material and thought that your goals to produce some 4.5 million electrified units and improve electricity consumption by 10% by 2025 are a big challenge. Can you give us details on how you are planning to go about achieving such goals?
Ms. Okawa:
Our main focus would be the eAxle.
eAxle has to be developed by reducing loss with a target of 50% compared to the previous generation eAxle, or we will not achieve a 10% improvement in total vehicle electric mileage. I am in charge of motors, and of course, we will also work on improving the efficiency of the motor itself as a single unit. However, we want to think about the optimal design of the system as a triad, not just the motor but including the transaxle, and inverter, to determine the best way to operate the system. Then we need to look at the results of the entire vehicle, to see how the system will work in the vehicle, and to expand from there one by one by combining optimization of all aspects. I believe that by doing so we will gradually see improvement in electric mileage.
Mr. Tanaka:
Thermal and Loss are keywords that many JMAG users show interest in. We are working hard to improve the accuracy of thermal and loss to develop an optimal design that accounts for various elements, not only the magnetic and structural aspects. But like you said, it’s important to look at the overall system, not just one side of it. I guess we need to consider combining various aspects to reduce the overall consumption of electricity.
Ms. Okawa:
Yes, I agree. Of course, in reality, the balance between electricity consumption and cost is an inseparable issue in business. For example, depending on what gear ratio you specify in the design directly affects the operating point of the motor. This will also change the efficiency. Motor design is also greatly affected by how much of a maximum current the inverter is designed to tolerate and also for example, how much torque ripple the vehicle can tolerate. Therefore, I believe it is most important to consider where in the entire process the emphasis should be placed when optimizing the design. It’s a matter of striking the right balance.
Moving Toward Electrification by Organization Restructuring & Resource Training Reform
Mr. Tanaka:
Aisin has transformed into one group and is now shifting its business from gasoline engines to electric motors for BEVs. Even in a normal situation, organizational restructuring involving personnel shuffles and manufacturing processes seems like a tremendous change… If there are certain measures you are taking in terms of organization and resources to achieve your goals, can you give us concrete details?
Ms. Okawa:
Changes in the organization were made gradually over several years before the merger.
The motor department which we are in charge of, started out in the same department as the department that manufactured the drive unit, but we separated it because we wanted to focus on the exclusive and unique skills of the motor. Furthermore, we need to develop next-generation technology for motors with a view for the next 10 years, not just develop current technology, so we created a new independent department to lead the development of motors. This much change is required for the motor alone. In addition, Aisin AW, which handles the drive units started with conventional vehicles has taken the lead in creating a department to handle drive units for hybrids and is further reorganizing its operations for BEVs. Currently, departments focusing on BEVs have been established not only in the promotion center which I previously mentioned but there are also 2 departments within the company; the No.1 EV department and the No. 2 EV department. In this way, more and more of our resources are shifting to electrification and within electrification, shifting to motors and BEVs. Also, in our department, the number of people has nearly doubled in the past two to three years.
Mr. Tanaka:
I’m sure you have pride as an engineer and skills accumulated not in just 5 years or 10 years, but over many years. Even with such skills, you have to shift to BEVs. I believe a major reskilling would be required. Can you tell us how you raise motivation and your methods of reskilling?
Ms. Okawa:
Until last year, a mentor was assigned to train each new employee, but with the rapid increase of employees we were not able to keep up with OJT. So, we consulted with the company and decided to take the new employees away from the workplace for 3 months and put them in an intensive study session. They started out by learning the basics about motors and focus on gaining the know-how needed to create drawings, with the help of instructors from outside of Aisin. We provided a classroom away from their work desk so they can fully concentrate on their studies. Right now, classes, which started this July, are in session for our third group of students.
Mr. Tanaka:
I believe it would be difficult for trainees to maintain motivation, but from a business perspective, training is definitely important when you have to compete on a global scale.
Ms. Okawa:
Yes, JSOL has also provided a lot of assistance in our in-house training on magnetic field analysis. We have our employees run a magnetic field analysis using JMAG as part of our training program.
Mr. Tanaka:
We want to do as much as we can to create a user interface that can be used by non-experts as well as experts. So, we would appreciate it if you would continue to give us requests for JMAG.
Ms. Okawa:
Using the motor I was in charge of as an example, the initial design takes time because of the many design elements and some having contradicting items. For example, if you need to raise the torque higher, in terms of machine design, the torque capacity will increase if the rotation strength is increased. However, in a motor, if the rotation strength is increased, the torque is reduced. Therefore, we create a base with magnetic field analysis and when intensity is not established by running an intensity analysis seeing your Website, you seem to have links with other company CAE software, which we would like to try and be able to use.
Mr. Tanaka:
Thank you. I will take this back to my team for discussion.
Ms. Okawa:
Currently, the designers are running direct analysis on the basic parts of the motor. Therefore, the ideal tool would be one that is easy for the designer to use and one where they accurately know that they are making a mistake when creating the settings. In the past, when we looked at the results of an analysis and wondered if something was wrong, we would look for the cause and find that some of the numbers under several hierarchies were strange or analysis results were strange because we unintentionally entered the wrong numbers. So, I think one of the things we are looking for is for designers to be able to prevent errors in advance as well as being able to run an analysis at a certain level. Being easy to use is also important.
Mr. Tanaka:
We will do our best to accommodate your requests.
The Difficulties of the BEV Business
Mr. Tanaka:
As business moves towards BEVs, focusing on the eAxle, I assume that your sales channels and overall marketing strategy, in general, will change significantly in the future. Since you distribute your products not only to Toyota but to many other automobile manufacturers, I’m sure you will be confronting various global competitors. Do you feel that the share of parts supplied to automobile manufacturers will gradually change in the future?
Ms. Okawa:
Yes, I do.
We have been talking to automobile manufacturers focusing on AT (automatic transmission). We are currently talking to various automobile manufacturers about our eAxle product but many say that when BEVs become the mainstream, they will manufacture their own eAxles.
All aspects of AT, from investment to various technology are a distinct differentiation of technology cultivated within the former Aisin AW. AT was the heart and soul of technology that automobile manufacturers could not create, but now with eAxle down to being just the motor and gear, different kinds of industries including companies that are not your conventional automobile supplier have entered the market. In addition, now that automobile manufacturers don’t need to make engines, they need to do something and inevitably end up having to manufacture their own eAxle. Automobile manufacturers will be desperate to make eAxles which means we have to compete with their in-house products. We will face much more difficulties in terms of costs.
Mr. Tanaka:
Although we are only seeing from the JMAG perspective I can sense that various customers have started to engage in the BEV business all at once and are scrambling to compete for market share.
Ms. Okawa:
Our problem may be that analysis tools are so sophisticated that anyone can design a good motor (ha-ha).
The Indisputable Strengths of the Aisin Group Today
Mr. Tanaka:
For example, automobile manufacturers, parts manufacturers, and in some cases motor manufacturers are all competing with each other. For AISIN, what would be the strength or competitive advantage that you would gain over the competition in this context?
Ms. Okawa:
I think there are several things.
First of all, as we have been discussing, in order to improve analysis accuracy, I believe it is important to accumulate experience in verifying whether results and actual measurements match properly.
To determine the validity of high-precision analysis, measurements must be highly accurate. We have developed measurement technologies for vibration and heat for the powertrain system, and I think we can use them in analysis to further improve accuracy.
Also, with motors, even if we know the ideal way to create them, we still have the problem of actually creating such a motor and churning out 10,000 units a month. Motors, in particular, cannot be separated from production technology. From my experience, manufacturing plants have various production technology know-how and the idea is to make use of this know-how in the pursuit for low cost. I believe being able to make products faster and at a low cost is what differentiates us from others in production technology.
Mr. Tanaka:
In the end, how a product is created is important.
Ms. Okawa:
Yes.
Mr. Tanaka:
I understand. Thank you.
Expectations for Development in CAE Software
Mr. Tanaka:
Although it may not be much, we are doing what we can as a CAE vendor, to respond to the overall changes in the automotive manufacturing process. Can you tell us what you expect from CAE now and how you expect it to evolve in the future?
Ms. Okawa:
In this day and age, shorter product development time is common. We often refer to a “two-year development period” because the Chinese automobile manufacturers require shorter deliveries compared to the automobile manufacturers we have dealt with up until now. In order to respond to their expectations, there is no way we can keep up with their requests by creating three or four prototypes, taking accurate measurements, verifying the results, and solving the issues one by one. So, from now on I think there is a growing need for high-precision analysis and the need to determine which technologies to use without creating and evaluating prototypes.
I think we need to make good use of DX (digital transformation), which is talked about in the company these days, to try using the 3D models not only in design but also in the production plan and see if it works. I believe that we need to conduct activities to improve development efficiency by conducting such verification all the way through the process. There are some key areas where this is actually happening, so I believe what we need to do now is to connect and unify these processes.
Mr. Tanaka:
You definitely need accuracy and speed to realize a process without prototyping. We will try to meet your expectations as much as possible. Thank you for your valuable opinion.
Ms. Okawa:
I think the accuracy of torque in magnetic field analysis can be realized without prototypes, but we need to work on improving accuracy for thermal and NV (noise/vibration) analysis.
Mr. Tanaka:
We would like to make more effort in this area as well.
Ms. Okawa:
We look forward to it.
To All Engineers: The Importance of Gaining Design Skills & Sense
Mr. Tanaka:
Lastly, putting the business aspects aside, I would like to ask your opinion as an experienced engineer. Although slightly different from your business, we are also working as part of the Japanese manufacturing industry and doing what we can. Can you give a few words of encouragement for future engineers and how you think they should develop their skills in the future?
Ms. Okawa:
I also started out with analysis. Analysis provides answers, but as a designer, you need to develop an eye for being able to determine whether the answers are correct or not. I still think that actually seeing what you are working on and raw data helps develop intuition, design skills, and sense.
I mentioned “without prototypes” before but I believe it is important to actually see the actual object you are working on when you are first starting out, including the features and structures. I realize there are less opportunities to go to workplaces and job sites and be in actual contact with what you are working on because of Covid, but I think it is important to actively create the opportunity to actually touch and feel what you are working on.
We often ask this at the Scientific Analysis Engineering Department. “The analysis is good, but have you actually seen what you are analyzing?” I think this aspect is what is most important. It’s the same thing as asking us if we only looked at the units without seeing the entire car. (ha-ha)
Mr. Tanaka:
Thank you very much.
Aisin Corporation
Associate officer in charge of
Power Train and Electrification Development
Power Train Company
Associate Officer Akemi Okawa
・Interviewer
JSOL Corporation
JMAG Division
COO Yasuhiko Tanaka
* If you cannot access the video, please check here.

You need to sign in as a Regular JMAG Software User (paid user) or JMAG WEB MEMBER (free membership).
By registering as a JMAG WEB MEMBER, you can browse technical materials and other member-only contents for free.
If you are not registered, click the “Create an Account” button.
Create an Account Sign in
Recommended
- AISIN CORPORATION : Calculation Cost Reduction Method in Multi-Objective Optimization Using Machine Learning: Case Study on Actuator Development , JMAG Users Conference Proceedings , 2021
- AISIN SEIKI CO.,LTD : JMAG & GT-SUITE Link for EV Traction Motor 1D Thermal Analysis , JMAG Users Conference Proceedings , 2020
- AISIN SEIKI CO.,LTD : FET Switching Control of PAM Inverter Circuit and Motor Characteristics Optimization of PWM Inverter Circuit , JMAG Users Conference Proceedings , 2019
- AISIN SEIKI CO.,LTD : A Temperature Prediction Technique of Motors by the Combination Between Harmonic Loss Simulation by JMAG-Designer and Thermal Simulation by FloTHERM. , JMAG Users Conference Proceedings, 2018
- AISIN SEIKI CO.,LTD : Cooperation analysis of optimization and quality engineering by modeFRONTIER and JMAG , JMAG Users Conference Proceedings , 2016
- AISIN AW Co.,LTD. : Multi-objective optimization with wide-range shape parametric design space for IPM motor , JMAG Users Conference Proceedings , 2014
- AISIN SEIKI Co.,Ltd. : Introduction to magnetic field design support system using JMAG , JMAG Users Conference Proceedings , 2014
- AISIN AW Co.,LTD. : Magnet temperature analysis and prototype verification in permanent magnet synchronous motor , JMAG Users Conference Proceedings , 2013
- AISIN SEIKI CO.,LTD : Electromagnetic Field Analysis for Smart Key Antenna , JMAG Users Conference Proceedings , 2010