Having celebrated its centennial in 2012, Yanmar established a new brand statement in 2016,: “A SUSTAINABLE FUTURE,-New Value Through Technology “. Based on the concept of “realizing a sustainable resource recycling society that leads to the future” the company continues to make technological advances looking ahead to the next 100 years.
A project team was organized, calling on experts of various fields from The Powertrain Center and the Research & Development Center to take on the challenge of riding on the new trend of “electrification”. We asked about the emphasis on vibration and noise, as well as the efforts made by the team in research and development.
TAKING ON THE CHALLENGE OF THE NEW TREND, ELECTRIFICATION, TO SOLVE CUSTOMERS’ PROBLEMS
Mr. Piao:
Our company was founded in 1912. As of the end of March 2021, sales were ¥782.3 billion on a consolidated basis and the number of employees is more than 20,000. The Yanmar Group’s business fields are very broad ranged expanding across land, sea and the cities. I think Yanmar is best known for its engine business and agricultural machinery business. We are also engaged in construction equipment, energy systems, marine and components business, such as transmissions.
In August 2016 Yanmar created a new brand statement as part of their corporate philosophy entitled “A SUSTAINABLE FUTURE- New Value Through Technology.” I joined the company because I was attracted to this corporate spirit. I believe realizing a sustainable resource recycling society that leads to the future is a very good concept. Based on this philosophy, we are making technological advances in anticipation for the next generation in the next 100 years.
Mr. Piao:
Yanmar has been expanding its business by manufacturing industrial machinery with engines, focusing on the manufacturing of excellent engines. Our final objective is not to sell the engines; our mission is to solve the problems of our customers. This mission has not changed since the company was established. Due to global environmental issues, emission control regulations have become more stringent and we anticipate that it will become difficult for customers to continue to use conventional engines as they do now. In addition, we also advocate the reduction of greenhouse gases. To solve these problems, we are working to develop a variety of technologies, including the use of clean energy. One of these is electrification and hybridization.
Mr. Hara:
I work in Technology Group 3 of the Powertrain Center at the Innovation & Technology Division. I am mainly in charge of the trial prototype design and evaluation of motors for electric hybrid work machines.
Mr. Kimura:
I also work at the same Technology Group 3 of the Powertrain Center as Mr. Hara. My work is pretty much the same as Mr. Hara and I am in charge of motor design.
Mr. Piao:
I also work at the Powertrain Center, but not on motor design. I work on running the motor and am in charge of the overall power electronics including motor control.
Mr. Abe:
I work at the Dynamics Group of the Fundamental Technology Research Center for the Research & Development Center at the Innovation & Technology Division. I mainly run analysis and experiments on vibration and noise. I am currently in charge of analyzing the electromagnetic force of the motor and measuring vibration.
Mr. Mizota:
I am also a member of the Dynamics Group of the Fundamental Technology Research Center for the Research & Development. The department is in charge of addressing issues related to vibration, noise, and thermal fluids for all Yanmar products. I have been in charge of such general analysis and experiments ever since I joined the company.
Mr. Hara:
Both are core centers in the Yanmar Group’s R & D activities. The Research & Development Center is engaged in R & D related to fundamental technologies, production technologies, quality analysis, and biotechnology related to all of Yanmar’s products and services. On the other hand, the Powertrain Center’s main focus is on the advanced development of electrification and hybridization in Yanmar’s future products.
JMAG IS EASY-TO-USE AND HAS GREAT RESOURCES
Mr. Hara:
I was told that JMAG was first introduced in 2010. It was mainly used for heat treatment analysis of engine components and in 2015, we made a presentation titled “Analytical Predictions for Residual Stress in Crankshaft Subjected to Induction Hardening” at the JMAG Users Conference. From around 2016, we started full-scale motor analysis and phased in analysis modules such as for magnetic field (DP) and vibration (DS). The reason we chose JMAG for motor analysis is simple. I was using it in my previous job. I chose JMAG without hesitation. Among the staff here today, I have used JMAG for 13 years, Mr. Kimura has 5 years of experience and Mr. Abe and Mr. Mizota have known JMAG for less than a year.
Mr. Hara:
That’s right. Since I’ve been working with JMAG as a student, it would be 15 years now. When I first switched from JMAG-Studio to JMAG-Designer, it felt strange and unfamiliar, but once I got used to JMAG-Designer, it’s not easy to go back to the previous application.
Mr. Hara:
For example, mesh generation. Since JMAG-Designer has an auto-mesh function, it automatically generates a mesh by assumption with only a few parameters having been set. On the other hand, with JMAG-Studio, I think we had to examine the analysis results to consider which mesh would best suit the objectives. I recall running trial and error for mesh generation.
Mr. Mizota:
I used auto-mesh in structural calculations, and we were able to generate mesh with considerable accuracy. Compared with results obtained by running structural calculations with other solvers, the results obtained with JMAG were almost the same, without detailed settings. I had the impression that accurate results are obtained with little operation.
Mr. Hara:
It may be that I’ve never felt JMAG is difficult to use because I’m used to it. Please ask the others what they think.
Mr. Kimura:
First of all, JMAG is easy to use. I had the opportunity of teaching people who use it for the first time in other departments, and I think it’s easy to use for on-the-job training because the operation is easy. Other than being user friendly, it is multifunctional. The versatility in being able to complete multiple tasks within JMAG alone is a great advantage.
There are two problems, or more like requests that we have. First, I feel that the materials database is getting old. In particular, some magnets listed in the JMAG library have already been discontinued and others listed in manufacturer catalogues are not available. It didn’t feel that inconvenient a little while ago, but I’ve been noticing this since this year.
The other is the control circuit which can be created in JMAG. I would appreciate if it could be assembled in a block-diagram. Of course, if you could write python codes yourself, you would have the control you wanted, but that would be a bit of a challenge… I think the usability will change just by having a block with differential and integral.
Mr. Abe:
It’s been about a year and I’m gradually getting used to it. In general, analysis software is usually in English and in such environment, I think that Japanese-made software like JMAG is quite valuable.
Mr. Mizota:
I think the interface is also easy to see. Each setting has a tree structure that makes it easy to see the set of flows, making it easy to operate without hesitation.
Mr. Kimura:
At first, Mr. Hara taught me how to use it. I also looked at the application notes and tried various things in my own way. I think the tutorial is user friendly. I just mentioned that I taught people how to use it, but there was limited time back then and I didn’t have time to prepare. However, the sessions went well because the tutorial was easy to understand and that was a great help.
Mr. Kimura:
I have pretty much only been using JMAG in the last few years. Before working on motors I used a completely different software, such as EMC Studio. Now I use JMAG almost every day.
Mr. Abe:
I joined the company in April of last year and have been using JMAG since July. What I think is good about JMAG is the abundance of material such as the application notes. I studied with the self-leaning system and was able to grasp the points for setting various analysis described in the explanation.
AIMING FOR LEADING TECHNOLOGY IN VIBRATION PREDICTION OF MOTOR DEVELOPMENT
Mr. Hara:
JMAG is mainly used to predict performance when designing motors. For example, the output; we check the calculation of maximum torque and fluctuation of torque such as torque ripple. We also use thermal analysis and structural analysis modules to predict temperature during operation and evaluate rotor strength.
Mr. Mizota:
As I mentioned in the presentation, I believe that when the wave of electrification arrives, the main component of the powertrain will shift from the engine to the motor. With this shift, I think that the distinct high frequency sound, a characteristic of the motor which was originally masked by the engine sound, will become conspicuous. I think automobile companies are already making efforts to reduce motor vibration and noise. I believe this is because low vibration and low noise become added values for the product. We have started this initiative on electrification, with an eye to the future.
Mr. Mizota:
That’s right. Low vibration and low noise will also become one of our objectives in engine development. I feel that our know-how and knowledge on low vibration and low noise accumulated from the development of engines can be used in the development of motors. However, there is a great difference in the vibration mechanism of the engine and motor, particularly at the exciting force. The exciting force of the motor is mainly caused by electromagnetic force, but I believe we still have a lot more to learn here.
Mr. Mizota:
Thank you. The analysis presented at the JMAG Users Conference only shows that we are at the level of being able to create a basic model for a certain motor, so it is as if we have just reached the starting line and will now begin to build up on our achievements.
Mr. Mizota:
The major objective is front loading the vibration noise design of the motor. To achieve this, we began working on constructing a model that can predict the vibration response with a motor prototype that we created in the past.
In reference to my mentioning “predicting the vibration response of the motor”, in doing so, it is important to model both the exiting force and the transmission system. In the initiatives presented at the JMAG Users Conference, we worked with Mr. Miwa of JSOL, taking on different responsibilities to construct a model of the exciting force and a model of the transmission system.
In modeling the transmission system, I acquired the natural frequencies and eigenmodes of the motor experimentally, and asked Mr. Miwa of JSOL to use PSL (Power Simulation License) to run optimization calculation. The motor we worked on uses a split core, joined by intermittent welding, making it difficult to accurately predict the rigidity. However, the rigidity (physical property value in structural analysis) was identified from the experimental values by running optimization calculation.
In modeling the exciting force, Mr. Piao was in charge of building a motor control model in Simulink. In addition, Mr. Hara worked on constructing the behavior model for the motor with JMAG-RT. Mr. Abe was also in charge of JMAG’s electromagnetic field analysis using a current waveform created by coupling a Simulink control model with a JMAG-RT behavior model.
Mr. Mizota:
That’s right. Since I initially specialized in vibration and noise, I was relatively good at modeling the transmission system, but I had little knowledge about electrical systems. So, we have all worked on building the model together by getting assistance from throughout the division to make up for areas in which we lack technical knowledge.
Mr. Piao:
I can’t say that it was a success, but I think the results were good. I think it was extremely beneficial that the software is flexible and is linked to various platforms. I have never used JMAG myself, but I was able to try out various ideas immediately by using the JMAG-RT model. I was quite pleased with that. Using JMAG as a common language may have helped us work together as a team.
Mr. Hara:
The team also worked together to obtain accurate data when measuring in the actual machine. Mr. Kimura, and Mr. Piao and I are the experts at driving the motor, and Mr. Mizota and Mr. Abe specialize in measuring vibration and eigenvalue.
By the way, when we built a temperature prediction model for a motor in the past, we worked in the same way, I worked on magnetic field analysis and driving the motor, while Mr. Mizota handled the thermal fluid analysis and temperature measurement. The results of the study were reported at the 2019 IEE-Japan Industry Applications Society Conference (*1)
(*1) Source: [D] from the National Convention record I.E.E. Japan, Industry Applications Society
“3-47 Study on Temperature Prediction of Coils in Permanent Magnet Synchronous Motor in an Unsteady State by Thermal Fluid Analysis ” by Toru Mizota, Takeshi Hara, Masaaki Konoto (2019) at the Industrial Applications Conference of the Institute of Electrical Engineers.
Mr. Mizota:
We received considerable cooperation from Mr. Miwa in PSL calculation. I was told that the key to running optimization is how the constraint conditions are set. It seems that the results may deviate without setting appropriate constraints or objective functions.
Mr. Mizota:
Calculations using general physical properties show that natural frequencies deviate by about 20%, and at first the calculations and experiments did not match at all. After discussing this issue with Mr. Miwa, optimization calculation using PSL was focused on only the physical properties of the stator core. I learned a lot about the modeling of the transmission system in this way.
Mr. Mizota:
Yes. The knowledge of modeling of motors has been accumulated through actual experience and we would like to continue to do so through repeated experience. The experience we gained here will most certainly be useful in the future.
Fig.1: Taking measurements
Fig.2: Calculation method
Fig. 3: Calculation results of vibration acceleration
(Figures 1 to 3) Source: from JMAG Users Conference Proceedings
Toru Mizota, “Vibration Prediction of Permanent Magnet Synchronous Motor by Aid of JMAG” (JMAG Users Conference, 2021 in Japan)
OPEN COMMUNICATION FACILITATES IN-HOUSE TRAINING
Mr. Hara:
We don’t have a training system yet. When someone starts using JMAG, we have them use the tutorial for self-learning and have them ask questions when they don’t understand. Right now, this is sufficient enough because there aren’t that many people learning JMAG, but I think we will need to prepare some sort of simple training material in addition to the tutorial.
Mr. Hara:
I recall having difficulties when I started creating the motor analysis environment. First, after disassembling, investigating and modeling the purchased motor, we spent about a year on verifying the accuracy of the magnetic field analysis results and actual measurements. At that time, there were only a few people and I didn’t have experience working with JMAG at Yanmar yet, so I remember it being tough. Results showed that predictions could be made with a certain degree of accuracy and we were able to implement the software for full-scale use. We are grateful to Mr. Narita and your company for the guidance provided since then.
Mr. Hara:
Meetings are held regularly or irregularly depending on the situation. For example, with motor design, the members involved will get together each time the results of magnetic field analysis and examination are obtained to exchange information and proceed to the next step.
Mr. Kimura:
In that sense, I think it is an open environment. Maybe it is working out because it is a small team, but it is easy to communicate.
Mr. Hara:
Although this is not about communication, I believe that managing the model will become important to facilitate information exchange. Right now there is a trend to create a system that allows for collective management of models held within the company to be used for development, starting with the control system. We are hoping to also incorporate models for motors made by JMAG and JMAG-RT into this system.
TOGETHER WITH JMAG, WE WILL CONTINUE TO TAKE ON CHALLENGES
Mr. Mizota:
Our ultimate objective is to design low-vibration, low-noise motors, so I would like to apply the flow built in the analysis case presented at the JMAG Users Conference 2021 to actual designs.
Mr. Mizota:
That’s right. In the structural design, we hope that the vibration response at a certain point can be used as an objective function, and the dimensions of the structure, etc., can be narrowed down within the scope of the constraints. We’ve heard that there are various types of control, and assume that differences in vibration responses due to differences in control methods can also be checked in JMAG models.
Mr. Kimura:
For example, the amount of heat generated by the motor’s copper loss increases with temperature, and I would appreciate it if there is a function in thermal analysis that can appropriately reproduce it. Currently, there is a method to use user subroutines or a method to couple with magnetic field analysis, but the former is complicated to set up subroutines, and the latter requires analysis time. It would be nice to have a function that can reproduce the increase in heat generation due to temperature rise when accuracy is not needed.
Mr. Piao:
We sometimes download the JMAG-RT model from the library on the JMAG website to check the operation of the motor control, etc. In doing so, we sometimes incur problems because the necessary parameter information is not available. We would appreciate your disclosing parameters more in detail.
I would also like to be able to use JMAG-RT models in PLECS. I think it is compatible with PSIM, but since I’m sure there are also many PLECS users, I would like this to be realized.
Mr. Piao:
I think there is a lot of information on seminars. Since many are catered for motor designers I would like to participate if there are seminars with perspectives on motor control.
Mr. Mizota:
I often study with the application notes and would also like to participate in a seminar.
It was a great opportunity to speak to you people who are in the midst of riding a new trend and facing new challenges. Thank you.
Interviewees
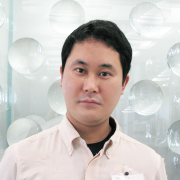
Powertrain Center
Technology Group 3
Mr. Takeshi Hara
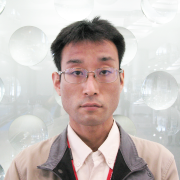
Powertrain Center
Technology Group 3
Yuto Kimura
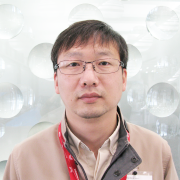
Powertrain Center
Technology Group 3
Mr. Qingyun Piao
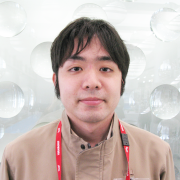
Research & Development Center
Fundamental Technology Research Center
Dynamics Group
Tomohiro Abe
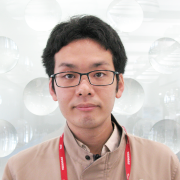
Research & Development Center
Fundamental Technology Research Center
Dynamics Group
Toru Mizota
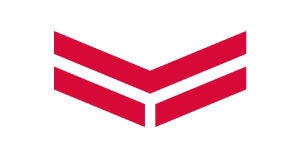
Business Domains:
- Agricultural machinery and facilities (tractors, combines, rice transplanters, tillers and more)
- Construction equipment (mini excavators, portable generators, light towers)
- Energy systems (micro-cogeneration systems, gas heat pumps and more)
- Industrial engines (compact diesel engines for industry)
- Large engines (marine power generation/propulsion diesel engines and more)
- Marine (small to medium sized marine diesel engines, pleasure boats and more)
- Components (hydraulic parts, transmissions and more)
Research & Development, manufacturing and sales
You need to sign in as a Regular JMAG Software User (paid user) or JMAG WEB MEMBER (free membership).
By registering as a JMAG WEB MEMBER, you can browse technical materials and other member-only contents for free.
If you are not registered, click the “Create an Account” button.
Create an Account Sign in