創業以来「着磁のスペシャリスト」として、磁気応用製品の先端技術開発を支え続けています。
株式会社アイエムエスは、主に永久磁石を磁化するための装置を開発から設計、製作まで手掛けられており、マグネットを作るために必要な着磁ヨーク(着磁するための治具)や特殊な電源を扱っています。また、着磁したマグネットがどう磁界を発しているのか、品質の検査に必要な磁界の測定器も製作されています。
世界で唯一の測定器だからこそ、シミュレーションとの相乗効果が期待できる。
弊社のこだわりといえば“着磁”です。主に永久磁石を磁化するための装置を手掛けており、マグネットを作るために必要な着磁ヨーク(着磁するための治具)や特殊な電源を扱っています。あとはご要望によって省力化するための自動機を手掛けさせていただくこともあります。
それともう一つ、当然ながら着磁した後にはマグネットができ上がるので、そのマグネットがどういった磁界を発しているのか、品質の検査に必要な磁界の測定器も製作しています。
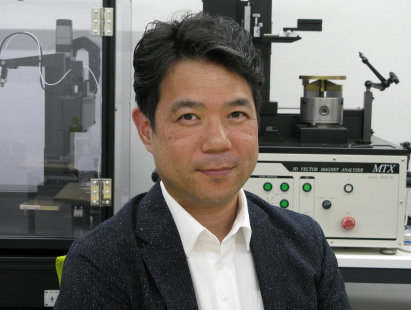
吉野氏:
非常にニッチな業界であることを活かし、価格競争ではなく、技術競争に価値を見出す企業でありたいということです。
事実、オンリーワンかナンバーワンの製品でないとラインナップには加えないというこだわりを持って製品開発に取り組んでいます。少数精鋭部隊ながらも、日々様々な努力をし、開発から設計、製作までのすべてを自社で行っています。さすがに板金や機械、樹脂などの加工品は外注していますが、それ以外は全て自社でまかなっており、基板設計やソフトウェアの制作も社内で行っています。
吉野氏:
世界で唯一の測定器、MTXです。3次元の磁気ベクトル分布を測定することができます。似たような製品はありますが、センサ自体が異なることと、弊社独自の「磁気センサ自動位置決め機能」や「角度補正機能」の特許技術を加味しているので、他社では作れないレベルの高精度な測定器になります。
具体的には、マグネットの近接磁界がどのようになっているのかを3次元の磁気ベクトル分布で見ることができます。つまり、シミュレーションで得られた3次元の磁気ベクトル分布が実測と合っているかどうかを確かめられるのです。そんな測定器はMTXしかありません。
モータの実機評価に加えて、着磁状態がシミュレーション結果と合致しているかを確認するためにはこういった測定器が必要となります。
また、最近は自動車のステアリングやシフトレバーのように、磁気で位置を検出するものが増えています。それらは磁気ベクトルを利用しているため、磁気の強さだけではなく方向まで重要になります。そのお陰もあり、この十年くらい急激に需要が伸びており、様々なところからお引き合いをいただいています。
吉野氏:
そうですね。シミュレーションが実機と合わない場合、実機を正と考えます。解析が合わない理由は、シミュレーションで物理現象を見逃しているか材料特性を見逃しているか。では、どこを直せば実機と近くなるのか、要因を分析、検証することで、シミュレーションのノウハウを蓄積していくことができます。シミュレーションの精度を少しずつ上げながら、より実機に近い解析ができるように改良できるというのは、弊社の強みでもあります。
3次元磁界ベクトル分布測定装置 MTX Ver.6
※動画にアクセスできない場合はこちらをご確認ください。
経験に基づいた技術を伝承する。そして、新しいアイディアへ。
吉野氏:
着磁の世界は短時間のうちに高電流を流して高磁界を発生させるので、とても危険な作業です。そのような危険を伴うことも、先代の頃から全て経験で行ってきました。日本の伝統芸能と同じく、特に数式や数字があるわけでもなく、先輩の経験を受け継いで作ってきました。つまり、弊社のノウハウは「これだったらこういう風にすればできそうだ」という経験則でしかなかった。私が着磁ヨークを学んだのも、色々失敗しながら自分で覚えていくという経験によるものです。
その経験を科学の力で数値化してくれるというのは、大変メリットが大きいです。私たちが経験で「こういう風にした方がいい」としてきたものが、シミュレーションによって「正解だった」ということが確認できました。経験の正しさをちゃんと数値化し、若い世代に伝えることができたのです。
着磁ヨークの設計を教えるのはとても難しく、例えばコイルの巻き数にしても「何で2ターンじゃなくて3ターンなんですか?」とか「4ターンじゃダメなんですか?」とか聞かれても、昔は経験からぱっと見て「これ2ターンじゃ弱いから3ターンにしよう」みたいな感じで具体的には答えられなくて。それが今は、シミュレーションで2ターンの場合と3ターンの場合と4ターンの場合を解析して、どれがベストかというのを数値で確認することができます。とても伝えやすくなっていっていると思います。
もちろん、MTXを持っていますから3次元での測定はできます。今まで作った着磁ヨークの3次元測定データを次のヨークの肥やしにするという作業もしていました。しかし、それは個人のノウハウにしかならないので、シミュレーションのデータを蓄積して残せるというのは大きなメリットになるのです。また、その中で使い慣れてくると、自分でも色々試行錯誤しながら新しい形のものを作って、それが今までの形よりも効率がいいとか経験を積むきっかけにもなってくれています。私の時代は作らなければ経験にならなかったのが、今は解析を回せば経験になってくるというところが圧倒的に違います。
解析結果と実測の比較(径方向成分・3軸合成値・ベクトル)
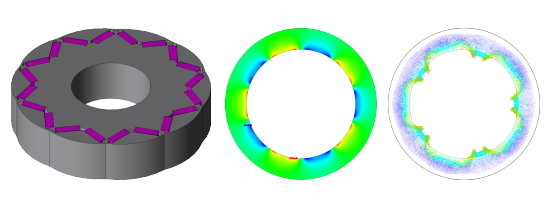
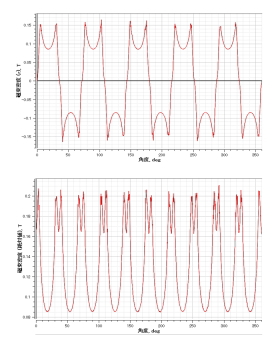
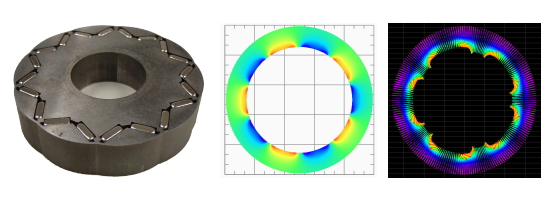
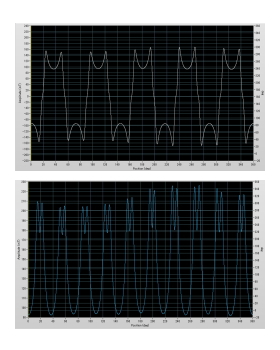
現行品からの改善案件
吉野氏:
解析がないと物が作れない人になってしまうのはデメリットです。それが怖いのは、解析がすべて正しいと思ってしまうことです。
シミュレーション解析だって入力の値を間違えれば、異なった結果になります。経験が豊富な人であれば、「この解析結果はおかしいだろう」とわかるところも、それが分からなくてスルーされてしまう場面はよく目にします。解析結果を鵜呑みにして「これなら着磁できる」とお客様にPRしてお仕事を頂き、いざ作ってみたら全然できないみたいなこともありました。何が原因なのか振り返ると、解析の入力値がそもそも間違っていたのですよね。経験のある人が見れば「これはありえないでしょ」という明らかな結果でも、やはり経験がないとそこには気付けないのです。
その中でも解析があることが若い人にとっては自信になっています。自分が設計したものがいざ着磁が入らなかったら相当の負担を感じますから。解析を回したら大丈夫だったという事実が、後押し的な意味合いで助かっていると思います。また、新しいものをひらめいた時にも解析でそれが証明されると「一回作ってみようか」ということにつながっています。今までは、コスト面でのハードルもあり、新しいことを考えてもなかなか実際に作って試そうというところまではいきませんでした。
吉野氏:
経験がものを言っていた時代は、着磁ヨークを10種類も20種類も作って、その中でベストなものを選んで、量産に適用することもありました。でもそれは、小型の着磁ヨークならば、数万円くらいで安く作れたからです。
でも今は小型モータの製造は海外が主流になり、日本で製造されるモータは、高価なモータばかりになってしまいました。サーボモータや自動車に使われる駆動用モータ、ロボット用の高性能モータは大型なので、着磁ヨーク一台が数十万から数百万クラスになります。それを何台も作って試してみましょう!というのは、正直許されなくなっています。一発勝負なので、解析で色々なパターンを作って最適なものを提案する必要があります。営業としては、検討結果を見せられるようになったというのは大きいですね。
課題を乗り越えて、常にチャレンジする。
最初は着磁ヨークのモデルを作って、そこから磁界を発生させるというところまで、ひたすらサポートの方に教えていただきました。2次元の立ち上げはあっという間でしたが、着磁解析は2次元では満足できないので、3次元の過渡解析にトライする必要がありました。この3次元過渡応答解析結果と実機との合わせには特に苦労しました。着磁電源を繋いだ電流値の計算まで合わせようとするとうまくいかず、様々な実験・考察を繰り返してきました。弊社独自の解析方法の確立ができたのも、この苦労の賜物だと思います。
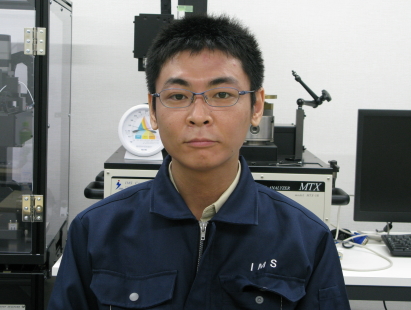
岩瀬氏:
そうですね。サポートの方には色々質問させていただき、具体的なやり方を教えていただきました。技術資料もたまに見ています。参考にしてみてうまくいかなかったら、また模索して、それでもわからなかったらサポートに相談して、またやり方を変えていくということを繰り返しています。
吉野氏:
未だに着磁は極限状態の世界です。JMAGには材料データが2テスラくらいまで入っていますが、実際には8テスラ、10テスラの世界なので、線形のまま持っていっていいのかはわかりません。あと、渦電流が今のところ合っていないので、それも課題です。
実際にマグネットの入るところに磁気測定器を置いて実際の磁場を測定すると、解析通りの磁場が出ていましたが、その磁場の強さであれば飽和するはずのマグネットが飽和しませんでした。原因は、渦電流がマグネット内に発生し、その反磁場で着磁磁界を遮蔽しているとしか考えられませんでした。それを確かめるために、マグネット側に渦電流が発生しない工夫を施して実験をしてみると、見事に着磁されました。つまり、実験結果は渦電流が原因であることを指し示していますが、同じような状況を解析上で再現しようとすると、なかなか上手く行きません。この件も引き続き追いかけていこうと思っておりますが、私たちは常に利益を出さないとなりませんので、ある程度割り切ってシミュレーションを使用することも重要だと考えています。
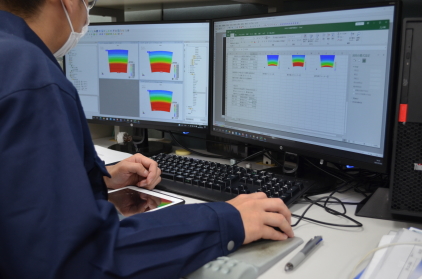
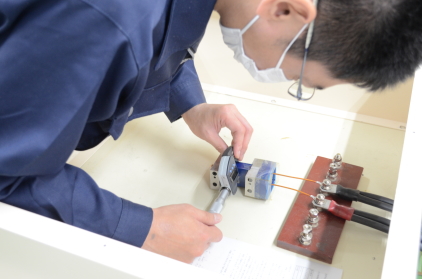
話は変わりますが、JMAGの社内教育はどのようにされているのでしょうか。
吉野氏、岩瀬氏:
社内独自のチュートリアルのようなものを作ってあるので、それを見せながらOJTをしていく感じです。
吉野氏:
JMAGは機能が多すぎて覚えきれないので。(笑)未だにコイルの巻き数や抵抗値は回路で入力する巻き数と同じだっけ?フルモデル分だっけ?みたいな。不安になると、簡単で速く計算できるモデルを使って、フルモデルと部分モデルの両方の解析を回して確かめたりしています。
吉野氏:
今まさにやろうとしているのが着磁ヨークの破壊です。着磁ヨークは仕様上どうしても壊れてしまうことがあるのですが、すぐに壊れるのは困ります。
ものすごく磁場がかかって大量の電流が流れるので、瞬間的に何百キロという力が電線にかかるのです。それを樹脂材でモールドして抑えているのですが、その樹脂材の厚みをいくらにすればいいのか、というのを経験則ではなく数値化していきたいと考えています。瞬間的なローレンツ力は計測が難しいのでJMAGでローレンツ力を解析し、それを実験器具で同じ力を出した時に樹脂が割れるか割れないかみたいな評価をしていきたいです。
あとはJMAGだけだと難しいのかもしれないですが、熱解析もやっていきたいと思っています。着磁ヨークは瞬間的に何十度も上がるのでヒートサイクル試験をやっているようなもので、それによって樹脂が劣化し電線が動くようになると絶縁が破壊されてしまうのです。できるだけ壊れないように作りたいという思いがあり、そのために今後もJMAGを活用できればと思います。
そういった新しいチャレンジをしていくというのがうちの会社のいいところです。
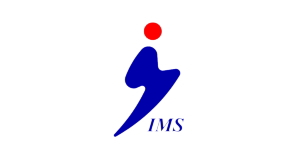
各種生産機器の設計・製作・販売
各種測定器・検査機器の設計・製作・販売
その他、ユーザーに基づき各種装置の設計・製作
『JMAGソフトウェア正規ユーザー(有償会員)』または『JMAG WEB MEMBER(無料会員)』でサインインが必要です。
『JMAG WEB MEMBER(無料会員)』へ登録することで、技術資料やそのほかの会員限定コンテンツを無料で閲覧できます。
登録されていない方は「新規会員登録」ボタンをクリックしてください。