創業から100年以上お客様のニーズに応えるべく技術開発に真摯に取り組んだ結果、現在12のユニットでの事業展開と多種の製品を有している。「SINFONIA NEW STAGE 2024」により、高品質な製品と技術で産業システムを提供し続け、人から宇宙まで、人々の暮らしと社会の発展に貢献する。
シンフォニアテクノロジー株式会社は、回転機の技術やパワーエレクトロニクスをコア技術とする電機メーカーで、技術開発力を生かして様々な製品を提供しています。
今回は、コア技術を新しい製品に発展させることをミッションとされている開発本部の皆様にお話しを伺いました。
私たちの暮らしと社会の発展に貢献し続ける100年企業。
稲葉氏:
創業は1917年で、三重県の鳥羽造船所内の電機工場が発祥です。その後、神戸の大貿易商、鈴木商店の傘下となり、2009年に社名を「神鋼電機株式会社」から「シンフォニアテクノロジー株式会社」に変更しました。2017年に創業100年を迎えたところです。
弊社は、創業当初から続く、モータや発電機などの回転機の歴史が長く、回転機技術やパワーエレクトロニクスをコア技術とする電機メーカーとして、様々な製品の開発を行っています。現在、大きくは、「モーション機器」、「パワーエレクトロニクス機器」、「エンジニアリング&サービス」、「クリーン搬送システム事業」の4セグメントで事業を行っており、分野としては、以下の12の事業分野に分類しています。
これらの中で今一番規模が拡大してきているのがクリーン搬送システムです。半導体工場で搬送されたウェーハを半導体製造装置に受け渡しをする入口であるロードポートという製品に関しては、弊社がトップシェアを占めています。主に豊橋製作所で設計製造を行っています。
電磁力関係に関する製品としては、豊橋製作所では、自動車用試験装置の分野において、EVを含めて自動車用主機モータの性能評価用試験装置を開発しています。産業インフラ分野では、サブマージドモータという液化天然ガスなどの低温液化ガス輸送用ポンプに組み込まれ、液体の中に浸った状態で使われるモータなども開発していますし、高度な金属材料開発に貢献する超高真空溶解炉の開発でも電磁誘導加熱の設計にJMAGを活用しています。
伊勢製作所では、航空宇宙分野の製品も開発しています。H-ⅡAロケットなどの宇宙ロケットでノズルの向きを変えるために使用されている姿勢制御用サーボアクチュエータは、弊社で開発しており、近年ではJMAGを用いて設計を行っています。また、航空機CO2 排出量削減として有望視されている、航空機用高出力密度モータの開発を航空宇宙技術部が行っており、開発本部は連携して進めています。モーションシステム分野では、産業機器用のモータや半導体製造装置の小型化を支えるダイレクトドライブモータ、高速回転が特徴である繊維機械向けモータを開発しています。回転機以外の電磁応用機器も開発しており、車両制御機器分野では、鉄道車両用の速度検出器の速度発電機、クラッチ・ブレーキ分野では、電磁クラッチや産業用ブレーキの設計にもJMAGを使用しております。
電磁力応用機器を中心に紹介しましたが、近年、新規事業として再生医療分野の取り組みを始めており、完全閉鎖型の自動細胞培養装置を製品化しました。神戸医療産業都市推進機構が開設した次世代細胞受託製造施設にソリューション・ラボを新設し、効率的な細胞製造環境の構築を後押ししています。
今後としては、現在、2022年度を初年度とする中期経営計画「SINFONIA NEW STAGE 2024」を実施中であり、継続的な企業成長を実現するため、新商品の開発、新事業の育成に重点的に取り組むことで、製品ポートフォリオの変革を図り、新たなステージでの安定した企業成長と、社会のサステナブルな発展への貢献を目指しています。
稲葉氏:
新中期経営計画「SINFONIA NEW STAGE 2024」の基本方針に基づき、技術開発力の強化と新製品の開発、新事業の創出を最重要テーマとして、開発本部は活動を行っています。弊社のコア技術は、電磁力応用と強く認識しており、開発本部の研究部メカトロ技術グループでは電磁力応用技術をより深く進化させ、新しい製品に発展させる役割を担っています。基盤技術グループは、直接製品に関わるというよりも設計開発のための基盤技術の開発が主で、4つのチーム(分析、材料開発、振動を応用する技術開発、解析技術の技術構築)があり、それぞれが開発力を下支えする役割を担っています。
実際の製品モデルを例題とした教育で、技術向上と自社製品の理解を深める。
稲葉氏:
弊社では、古くから自社製の有限要素法解析ソフトウェアを使用しておりましたが、1990年代になってからは、商用の汎用有限要素法ソフトウェアを併用して設計を行っていました。ただ、静磁場解析であったため、回転機設計への利用は限定されていました。その後、2000年代初頭に3D-CADが社内で普及し、3D-CADとの連携を目的に2006年にJMAG-Designerを導入したのが始まりです。設計者にとって使い勝手がよく、回転機設計に使いやすいという評判が広まり、稼働率も非常に高かったので、導入と同じ年に二度も追加導入しました。その後も断続的にライセンスを増強しています。
稲葉氏:
今回インタビューに参加しているメンバーのうち2名は2012年度入社ですが、新入社員向けに2012年度から毎年継続してJMAGを用いた磁界解析の講習会を実施しています。彼らが加わった後から、各事業部でのJMAGの利用が増加しているので、社内講習会を継続的に実施する効果があったと認識しています。教育は対面にて行っており、操作教育についてはJMAGに搭載されているSLS(セルフラーニングシステム)を利用していますが、解析に重要なモデルリング方法を伝えるため、弊社製品に合わせた例題を作成して教育を行っています。やはり操作教育だけでは、実務で使うには不足しているので、実際の製品を例題にモデル化や評価の方法も伝えられるようにしています。とは言え、導入教育にすぎないので、講師を研究部のメンバーが担当することで、実際に解析を行う時の相談先としての面識ができ、新入社員が相談しやすくなる効果を期待しています。また、CAE技術というのは一つの手段ですので、それをどう設計に使うかというところまで一緒にやらないときちんと伝わらないと考えています。また、新入社員向けだけでなく、次の中核となるモータ設計者を育成するための少人数教育も2021年から開始しています。
藤岡氏:
解析ユーザーを数値でお示しすることは控えさせて頂きますが、新入社員への解析教育を10年以上継続してきたことで、各部門で確実に増加しました。また、磁場解析だけでなく、構造や伝熱などのモータ設計に必要な解析も含めて行っています。根本や渡邉が所属しているメカトロ技術グループでは、主にモータに関する新しい技術の構築に各種解析を活用しています。私と稲葉が所属する基盤技術グループでは、解析精度の検証や、設計での汎用性や使いやすさを高めるために解析技術の構築を行っています。
藤岡氏:
よかったなと思うことは、電磁気設計を語る上での社内の共通言語になりつつあるということです。設計ツールを使っていたこともありますが、モータの寸法や流す電流の値を入れてトルクの出力を計算するだけのものでした。JMAGは出力の計算だけでなく、実際にフラックスラインやコンター図で物理現象を視覚的に捉えることもできるのが良いですね。「今ここに磁束が集中しているからトルクが出ないんだ」とか「今はここで交番磁界から鉄損が発生しているんだ」とか、設計の改善ポイントが見えやすくなりました。
磁場解析以外ではありますが、他の解析ソフトと較べてJMAGは扱いやすいです。使いやすさは非常に重要だと思っていて、どんなに結果の精度がよくても、使いづらいソフトだと社内普及は難しいです。特定の人しか使えないソフトでは全体的なレベルアップにつながりませんし、みんなが使える、みんなが理解しやすいソフトというのは非常に大事です。そういう意味でJMAGは、ソフトとしても扱いやすく、結果も評価しやすいので、社内の設計レビューでもJMAGの画面を実際に見せて「電磁気設計ではこういうことが起こっている」というのをプレゼンしたり資料に載せたりしています。
要望としては、損失解析の精度向上ですね。今後も情報共有をしていただきたいと思っています。あとは計算時間の短縮。今でも年々高速化していただいて嬉しいのですが、今後も期待をしています。
渡邉氏:
交流損の計算の時や部品を細かく見る場合、一個一個の設定に時間がかかることがあって、そこはパターン化するような機能があるといいなと思います。
根本氏:
事業部ではより短期間での設計が求められるので、JMAG-Designerで全部設定するのが煩わしいという意見もあって、人によってはJMAG-DesignerよりJMAG-Expressを使っていたりします。開発本部だと比較的時間に余裕があるのですが。
習熟度の面でも、モデルや材料など条件を色々変える度に時間がかかってしまうのが気になっています。SPEEDやJMAG-Expressは、もう少しモータ設計者に寄り添っていて、「モータ設計者だとこうするよね」というものがツールに入っているので、設計者としても使いやすいのかなと思います。
あとは形状エディタがもっと使いやすくなると嬉しいですね。SOLIDWORKSと連携できるので良いのかもしれませんが、連携すると更新時間がかかって最適化が進まないこともあったりするので、JMAGのみで完結できるのがベストだなと思っています。
JMAGの使用が、社内・社外の円滑な情報共有に貢献。
藤岡氏:
最初の話にあった通り、弊社の製品は多岐に渡っていて歴史も古く、部門によってモータの容量や使用環境、用途が異なるため、独自色の強い製品展開をしている部分があります。ですので、設計に使っているツールが部門ごとに異なっていました。電磁気学の式を基にモータ設計用のプログラムを作成している部門では、過去の実績や経験から補正を加えている場合もあります。そのため、他部門の設計者と交流をする時にちょっとしたハードルがありました。近年では、部門を越えた製品展開も検討されていますので、やはり共通の設計ツールがあると部署同士のやり取りがスムーズになって非常に便利です。これが、最近特に効果を感じているところです。
各部門にJMAGを使える担当者がいる状態となったことで、部門間で電磁気的な設計情報をやり取りする時にはJMAGのデータを元にしてコミュニケーションをとるので、かなり部門間の技術横断がやりやすくなったと感じています。
藤岡氏:
そうですね。今はモータの外注先やモータの分析を依頼する先でもJMAGが使われています。最近では、社外に色々お願いすることがありますが、やはり同じ解析ソフトを使っていると、こういう方法で鉄損を計算したのなら、こういうところは精度がよさそうで、こういうところは精度が悪そうだなというのが共通でわかるため便利でした。
藤岡氏:
私や渡邉は各部門にJMAGが使える設計者が行き渡った最初の世代なので、JMAGの使い始めは苦労しました。解析結果がどこまでが正しくて、どこからが正しくないのだろうといった線引きが難しくて。
社内の過去実績を元にした開発だと予測と解析結果がどの程度合うかが何となくイメージつくのですが、大幅な仕様変更を求められる開発の場合は、過去の知見が通用しないこともあるので、JMAGを使って検証したい。けれど、技術部の設計者から「この解析はどこまで信じていいの?」と質問されたりもする。実際、開発本部としても「トルクだったら大体合うけど、損失は違うこともあるよな…」という実績を積んでいる状態がかなりありましたので、最初に苦労したのはそこですね。
藤岡氏:
はい。解析実績を蓄えていく中で「こういう機種のモータだったら、これくらい損失が違うかな」といった経験値は溜まりつつあります。ただ、まだまだこれから普及して使っていく中で、もっと経験値を増やしていきたいなと思っています。
「損失推定の高精度化」で高効率な製品開発へ。
藤岡氏:
私が取り組んでいることとして、損失解析の精度向上という課題があります。JMAGを使い始めた当初は、材料データを参照して鉄損を計算するという方法でした。その後2015年か2016年くらいからプレイモデルや1D法という、より磁束密度を高周波なところまで広げた鉄損の計算手法が実装され、さらに異常渦電流損が一定値での補正だったのがテーブル補正をできるようになり。どんどんJMAGに新しい計算手法が取り入れられたので、それに合わせて新しい手法を適用するとどうだろうということをやっています。
以前、モータの効率を上げるという課題に対し、どう設計変更をしようか、損失分布をコンター図で確認して検討していました。この分布を可視化できるというのは非常に便利な機能だと思っています。この時、損失計算を新しい手法に置き換えたところ、今まで損失が発生していたと思っていた場所が、実は別のところで集中的に発生していたことがわかりました。そこで、実際にそこの損失を減らすための寸法変更をしたら、モータの体格を保ちつつ効率アップが実現できたことがありました。
藤岡氏:
今モータの高速化がどんどん進んでいます。高速になると鉄損が実測と合わないというのは昔から言われていることではありますが、そこを何とかうまくとらえて鉄損を抑えたいと思っています。あとは、熱設計ですね。熱が出たからには冷やさないといけないので、どこでどうしてどのくらい発生しているのかというメカニズムの把握もしています。
藤岡氏:
製品によって使い分けています。例えば試験装置だと2次元解析でも比較的精度のよい結果を得ることができますが、扁平なモータを扱っている部門では、概略設計では2次元解析を使用して、最終的に漏れ磁束を考慮した判断をする段階で3次元解析を行うなどがあります。
根本氏:
補足すると、インダクションモータはPMモータよりも漏れインダクタンスの影響がかなり大きいので、3次元解析をやらざるを得ないです。JMAGのアプリケーションカタログである程度提案されているように、3次元解析で一度漏れインダクタンスの影響を確認して、それを2次元解析に補正として入れ込むという方法も採用しています。補正すれば基本的には合わせこむことができています。
1.ヒステリシス損の分布(時間平均値)
2.渦電流損分布(瞬時値)
モータ損失の結果図
藤岡氏:
各事業部の設計者とのつながりがあるので、損失解析に関してなどの相談を受けた際に、構築してきた解析技術を適用できるようにサポートすることで展開を図っています。解析技術の評価は開発本部が行っているので、事業部の課題を一緒に検討して解決するように動いています。最近は色々な部門から高速化に伴う設計の相談を受けたりしています。
根本氏:
もちろん、すべてのモータで高速化が求められているわけではなく、低速で回したり、きれいに回したりするのが重要なモータもあります。モーションシステムの分野ですと、すごく遅い回転速度で回して、位置決めの用途で使われることも多いので、相談内容はアプリケーションによりけりだと思います。
これまでにない高出力密度達成のために。
根本氏:
はい。航空用途として期待されている多極化モータの研究開発を行いました。高出力密度化設計の検証を行い、設計手法として確立させるため、2019 年度から2021 年度「NEDO先導研究プログラム/エネルギー・環境新技術先導研究プログラム/低CO2エミッション航空機実現に向けた推進用高出力密度電気モータシステムの研究開発」に参加しました。
高出力密度達成のために、マグネットをV 字配置することで、省スペース化を図りました。多極化による高周波損失の低減については、分割マグネットを採用することでマグネットに発生する渦電流を抑制。エッジワイズコイルを採用することで、コイルに発生する交流損を抑制するよう対応しました。JMAGを活用して、それら高出力密度達成のための対応策を反映し、かつ設計諸元を満たす設計を行いました。高出力なので発熱も大きく、最適な冷却システムを構築することも課題でしたので、熱流体解析を用いたモータの冷却最適化技術の開発と共に技術構築を進めています。
根本氏:
元々機械的な構成含めての軽量化が求められますので、最初の頃は、JMAGでの高精度な解析というよりも、ある程度おおざっぱな体格検討を行います。その上で、モータ設計の上位の検討において、JMAG-Expressのようなすぐにモデル化して計算できるツールを使って、体格とトルクのバランスを見ながら絞り込んでいきます。次にJMAG-Designerでは磁気回路設計の部分を見ますけれども、他の機械設計なども含めて、これだったら成立しそうだと細部の設計を詰めていって、精度を上げていくという形で進めています。
根本氏:
モータの構造検討では、要求仕様があったらそれを満たすように設計するという感じでしょうか。結構制約が厳しいものもありますので、制約を満たす中でどのくらいトルクが出るのか、理論ベースで予測するだけでなく、さらに詳細に検討する場合はJMAG-Expressを使ってみます。JMAG-Expressの検証だけでは製品として色々足りないところもあるので、そこからJMAG-Designerに移して、少しずつ精度を上げていくという流れです。後者の方がやはり計算時間も多くなりますので、モータ設計の上位の方で構造設計の色々なパターンを検討してみたりします。
航空機用高出力密度モータ外観図
根本氏:
本当の初期段階では熱流体解析はしていません。流体については理論的にこのくらいの熱伝達ができるのかはわかりますので、初期の段階では概算でやっています。詳細な形状ができてくると、圧力損失などの問題も出てくるので、少しずつ精度を上げていきます。
稲葉氏:
熱流体は、ここ数年で設計に適用できるレベルになってきましたが、計算だけではまだ信用できないというのが正直なところです。想定される冷却システムの要素実験と解析や伝熱工学の実験式による計算を併用しながら、精度検証をして、実験式で扱える範囲であればそれを使うのが一番効率いいですし。ここは解析を使わないとまずいな、というところを見極めて、あとは、熱の計算自体は伝熱解析に熱伝達率を適用してという形で進めています。
藤岡氏:
鉄損に関しては、まだ解析ソフト側の課題もあると思っていますが、ユーザー側の課題も多くあると思います。導入当初に比べると、間違いなく実験と解析の差は小さくなっているので、入力する電流波形をどうするか、形状モデルに対して実寸法のバラツキをどう考慮するかなど、今後も継続してもっとつめていきたいです。
プレイモデルに関しては、自社で完結できるように、プレイモデル用のヒステリシスループを測定する装置を導入しました。せっかくよりよい高精度な新しい鉄損推定手法が実装されたのだから、それに入力できるデータを社内で取得して活用したいと思っています。
部分設計から全体設計へ。シミュレーション技術を用いた新たな挑戦。
藤岡氏:
昨年末のJMAGユーザー会でも感じましたが、ここ数年の傾向を見ていると、JMAGだけで完結した取り組みだけでなく、熱解析や構造解析、制御回路との組み合わせなど、様々な解析と組み合わせて、システム全体として検討する事例が増えていると感じます。
弊社も、モータの高速化とともに、小型化や軽量化という要求もあるので、振動や騒音が課題になることがあります。そのため、振動解析との連成により、モータの電磁加振力を元にした、振動や騒音の検討をさらに進めていきたいと思っています。
あとは先ほど言った熱です。これもモータ出力を保ったまま小さく軽くしていくと、発熱密度が上がるため、熱がこれまで以上に課題になってきています。JMAGと熱解析を組み合わせて「ここを集中的に冷やそう」、「ここの損失を集中的に減らそう」といったトータルでの検討もしていかないといけないと思っていて、解析分野を跨いだ取り組みに力を入れたいです。
藤岡氏:
そうですね。やはり多くのモータメーカーさんの中で、他社に追いつけ追い越せじゃないですが、「他社さんは、もうこういうことができるレベルにいる」とか、「最低限あそこまでいっていないと同じ土俵にも立てない」という確認ができるので、JMAGユーザー会は有用な情報収集の場所になっています。
以前、モータ単体で電磁加振力を小さくする内容の講演が集中していた年もあったと記憶がしています。モータモデルで電磁力を求めて「電磁力を減らすためにコアの形状をこうしました」とか「電流波形をこうしました」という内容だったと思います。
それが近年では、電磁力を受けた上で構造系はどうなる、さらにそれを積んだ車はどうなるなど、全体設計にどんどんシフトしていっているという印象を受けました。
本日はありがとうございました。
お話を伺った方
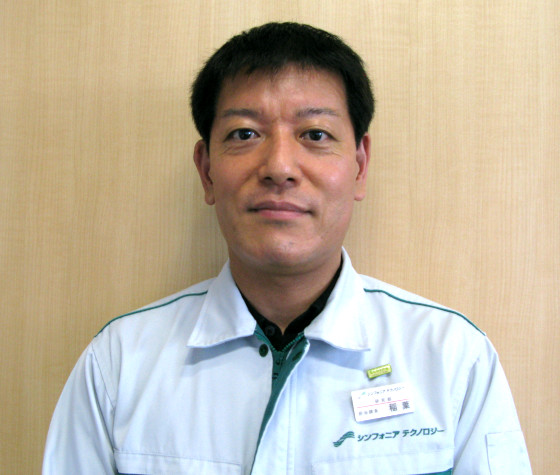
担当課長
稲葉 純吉氏
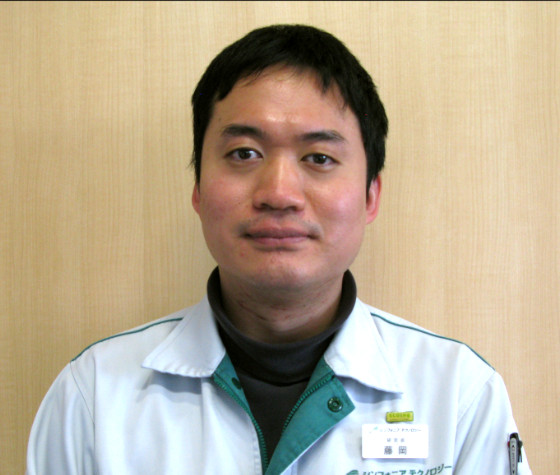
基盤技術グループ
藤岡 雄大氏
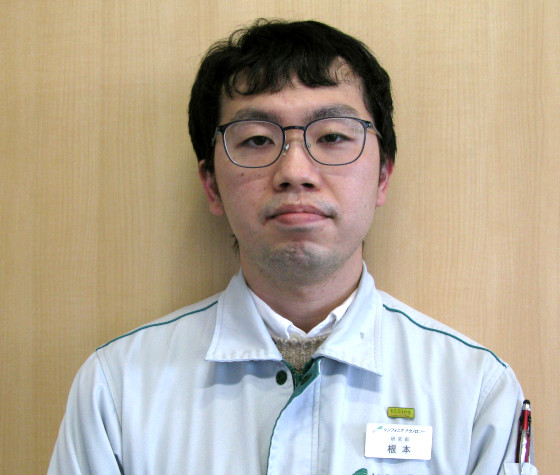
メカトロ技術グループ
根本 達也氏
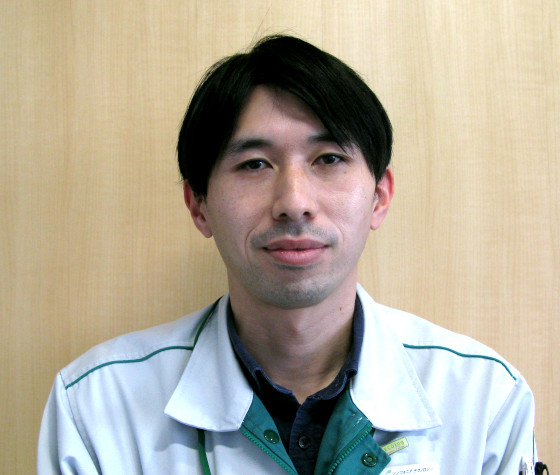
メカトロ技術グループ
渡邉 瞬也氏
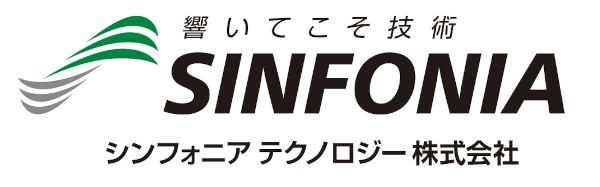
東京都港区芝大門1-1-30 芝NBFタワー
- クリーン搬送システム(半導体)
- 試験装置
- 振動機
- パーツフィーダ
- 産業インフラ
- 社会インフラ
- 航空宇宙
- モーションシステム
- モーションシステム(車両制御機器)
- 大型搬送システム
- プリンタシステム
- クラッチ・ブレーキ
- 再生医療、物流、農業
『JMAGソフトウェア正規ユーザー(有償会員)』または『JMAG WEB MEMBER(無料会員)』でサインインが必要です。
『JMAG WEB MEMBER(無料会員)』へ登録することで、技術資料やそのほかの会員限定コンテンツを無料で閲覧できます。
登録されていない方は「新規会員登録」ボタンをクリックしてください。
他の導入事例はこちら
高出力密度モータのシミュレーション技術に興味がある方におすすめの資料
- 岡山大学:「モータの更なる高出力密度化に向けて」, JMAGユーザー会講演論文集, 2022
- 多摩川精機株式会社:「高密度高出力 推進用モータの最適化設計」, JMAGユーザー会講演論文集, 2022
- Rolls-Royce Hungary kft:「Electrical Machine Loss Simulation and Model Validation Using JMAG and MATLAB Simulink」, JMAGユーザー会講演論文集, 2022
- IAV GmbH:「Next Generation EV Motor Design Using JMAG-Designer」, JMAGユーザー会講演論文集, 2021
- 株式会社 本田技術研究所:「電磁界解析(JMAG)による電動車用埋込型磁石モータの性能分析技術」, JMAGユーザー会講演論文集, 2021
- 住友電気工業株式会社:「圧粉磁心を搭載したアキシャルギャップモータの解析/実機比較」, JMAGユーザー会講演論文集, 2020
- AVL software & function GmbH:「Load Influence on AC Resistance of a High-Speed Permanent Magnet Electric Machine for Electric Vehicle Applications」, JMAGユーザー会講演論文集, 2019