Since its establishment in 1974, Takao Kogyo Co., Ltd. has been manufacturing automotive parts, industrial machinery parts, EV(electric vehicle) parts, and precision machinery parts. The company has recently been working on a new mode of production with metal 3D printers in their manufacturing services and the development of induction hardening technology.
Takao Kogyo Co., Ltd. has expanded its business by manufacturing automotive parts and precision machinery parts with advanced metalworking technology and world-class quality. In August 2021, TKE Co., Ltd. was established as an affiliate to promote the new technologies developed by the Takao Kogyo group. In this interview, we ask Mr. Yutaka Shimomura, CEO, Mr. Junichi Goya, Director, Mr. Fumikazu Goto, Manager of the IHT Development Department, and Masaomi Kawabe about the company’s efforts in developing new ways to reform production making use of metal 3D printers and induction hardening technology.
AHEAD OF 50TH COMPANY ANNIVERSARY
Mr. Shimomura, CEO:
This year marks 48 years since the founding of our company. A few years ago, we were thinking of starting something new, a new business ahead of our 50th anniversary, but everything had been put on hold for the past two years because of Covid-19. Meanwhile, in order to make use of human resources, we decided to start sales of products created with 3D printers at our IHT Development Department, something we had wanted to do for a while. We receive orders for machining/induction hardening of automotive parts, and as a manufacturer of automotive equipment, we wanted to provide tools, equipment, and parts to our business partners. So, in August 2021, we established TKE Co., Ltd. We’ve had some difficulties because of Covid-19, but I think we achieved certain results by promoting our PR activities at exhibitions. I believe we can say that we have just started activities for our 50th anniversary.
What we want the most nowis to try creating something new,changing it with the times and not continuing what we have been doing.
USING 3D PRINTERS TO BRING IN FRESH IDEAS
Mr. Shimomura, CEO:
I think everybody knows what a 3D printer is, but it is an area that has shown little progress in Japan. It was sensational to see the products of European manufacturers at an exhibition in India four years ago because the gap between Japanese and European products was all too clear. Furthermore, the Asian offices of the European manufacturers were in China and Korea. None were in Japan. It seemed inevitable that Japanese manufacturing would not be able to compete unless something was done.
The issue with induction heating is the manufacturing of heating coil by brazing which we have been doing since the beginning when the company was established. It is a process that only a highly experienced person can handle because it is extremely difficult and also required sophisticated technology. When I thought about how to fix this, I came up with the idea of creating shapes with a 3D printer and went on to develop this idea.
The idea is to reform and to realize reform I used the 3D printer. I believe awareness among employees has changed considerably. It was good PR to show our customers that we have started something new and I believe we were able to take a great step forward.
Mr. Shimomura, CEO:
No. At first, I thought that using brazing for machining would work well butcost performance was quite bad. In the end, we ended up going back to brazing. We can create shapes because our company has always been designing induction heating coils. So of course we can create the shapes by brazing. It’s just that back then, we were only successful 70% of the time. Thinking about this risk made me strongly feel we had to dosomething.
This is when we came to the idea of using the 3D printer. Unfortunately, back then, I had never seen a metal 3D printer in Japan and only resin could be used. When I asked around in Japan if metal (copper) could somehow be used in a 3D printer, I was told it was not possible. I will never forget the sensation I felt when I actually saw a metal 3D printer, sitting there like a commonplace thing, at the exhibition in India, creating a heating coil like I always imagined.
The metal 3D printers in Europe are mainly used for aircraft parts. I don’t think they are hardly ever used for induction heating. Manufacturers deliver 70% of their 3D printers to aircraft part manufacturers. They may create shapes as samples but I have never heard of anyone mass-producing heating coils. So, creating heating coils for induction hardening is practically a Takao Kogyo original.
In front of the metal 3D printer: IHT Development Dept.,
Mr. Fumikazu Goto & Mr. Masaomi Kawabe
Various heating coils created with 3D printers
3D PRINTER AND JMAG DRASTICALLY CHANGE DESIGN TIME AND ACCURACY
Mr. Shimomura, CEO:
Compared to the brazed coil which took about 2 months including the designing and trial and error phase, with the implementation of JMAG and the 3D printer, coils can now be created in about two weeks.
Using JMAG has reduced error rates to 0 in trial and error of the design phase. This is a major achievement. There is no meaning in faster manufacturing unless the created product is of high accuracy and we achieved high accuracy in a fast production cycle.
Mr. Goya:
The process of coil development is performed in the order of 1) design, 2) coil creation, 3) heat treatment testing, and if the heated pattern matches the blueprint, we pass it on to the manufacturing department. Before using JMAG, we ended up with many coils that did not satisfy the heat treatment specifications when tested. When this happened, we had to start again from the design phase and repeating this process would mean 2 cycles take 2 months and 3 cycles take 3 months. Now, it takes about one week including the design time to get feedback and if we try hard enough we can finish the 2nd cycle of corrections in about two days. The turnaround from design to manufacturing has become extremely fast. Currently, JMAG’s accuracy ratio is about 87%. I believe the accuracy will be improved more.
Mr. Shimomura, CEO:
Yes. It’s good that you can see the results immediately. I also think that the shape of products is more difficult now than they were 5 or 10 years ago. Because not having data makes it difficult to express in JMAG. I just mentioned that JMAG achieves about an 87% accuracy but I personally think it’s pretty amazing that JMAG has improved accuracy to that high a level.
Mr. Shimomura, CEO:
In the IHT Development Department, we need to train people with knowledge and know-how on induction hardening facilities, as well as using software. I believe they should learn from experience on the front lines first. I also think we need to educate people with details on materials. As for products, I have doubts about whether the material we use now is good enough. We run all sorts of tests but we have so much work to do, that we haven’t gotten around to it yet.
Mr. Shimomura, CEO:
Yes. We’re starting from absolutely nothing, so we are working on gathering human resources with a certain extent of experience rather than training people from scratch. You can’t do anything unless you know what the final product is and know what to do.
Also, we need to work together as “a team” to get anything done, not just one or two people, so collaborating with each other is quite important as well.
CHANGING THE MANUFACTURING PROCESS TO MAKE BETTER PRODUCTS
Mr. Kawabe:
On April 16, 2019, a quality improvement project was launched with the aim of improving quality. We created many heating coils for that project, but as I mentioned earlier, it took about one month to create the coils. I strongly felt it was a waste of time and money since it was a very difficult project and we often did not achieve the results we aimed for. At the time, one of the project members asked if there was a simulation software for heat treatment, and we found JMAG, by searching on the web.
Since then, we participated in the workshop in November 2019, started trial use the following year, and after the presentation to our President and board of directors, decided to use JMAG. Our objective for implementing JMAG was to shorten the time required in coil development and to obtain design information. I believe these two objectives have been fully achieved.
Mr. Kawabe:
Yes it was, because that waswhat I wanted.
Mr. Shimomura, CEO:
Honestly speaking, there were various problems including the quality, to the extent that we would not be able to take orders from Europe unless we were able to solve them. Everyone worked so hard to resolve the situation.
Mr. Kawabe:
It helps to deepen our understanding by seeing the good or bad results visually. Now, when the results are not good, we can grasp the basic idea of what area of the heating coil needs improvement. We have two PCs that are constantly running simulations.
Mr. Kawabe:
JMAG wasn’t considered reliable when we first started using it. So, we ran calculations in JMAG and manufactured heating coils simultaneously. But now, production waits until we obtain JMAG results.
Mr. Goya:
Despite introducing JMAG, I was personally concerned about how well the heating coil designers would accept the simulations, but after seeing the results, the awareness at the production site changed. Gaining the trust of simulation results was faster than I expected.
Mr. Shimomura, CEO:
Although design-related software, including JMAG, is used in research laboratories, I think it’s rare for such software to be used at the end-process of making products a manufacturing plant. Although design and development departments may use such software, manufacturing plants have never used them because they are not considered reliable. Thus, they are unable to make full use of the software. But, this is not so at our company. I believe this is the key to our business. The companies that own 3D printersare mostly research laboratories, but we use the 3D printer in our manufacturing plant. Designing cannot exist without a product, so you need to match the simulations with actual measurements. That’s why it’s important that everybody involved acknowledges that the software is reliable even if some of them didn’t feel it was possible at the beginning. I think it took only about six months or a year for awareness to change at the production site. That made me really happy.
Mr. Shimomura, CEO:
Now, we are too worried to go ahead without seeing JMAG’s simulation. Conversely, the major change is that we can still make the deadline even if we wait for the analysis results. When working on brazing, we were able to run in-house testing because we happened to have a prototype plant, but when the prototype failed, we ended up with a lot of time-consuming rework.
Mr. Goya:
In the past six months, we almost ran up to 100 simulations. I mentioned the accuracy ratio before, but in the past, we used to create heating coils that would not work in a simulation. With this in mind, when we convert that to actual cost, it is a major cost reduction and we’ve stopped wasting metal (copper). This is good for the environment.
Mr. Goya:
Our workflow is to run the simulation once the design is completed and if the results are good, go on to create the product parts with a 3D printer, assemble the parts and run a test. Two of the staff are responsible for running the simulation out of 18 people on our team. Mr. Kawabe is the leader in operating JMAG and uses two computers to run analysis on a daily basis. The department head, Mr. Goto examines heat-dependent physical properties by referring to documents and runs the actual experiments to improve accuracy. He also makes proposals for the methods and jigs used for examining physical properties. This is reviewed by everyone involved at the weekly JMAG meetings.
Mr. Kawabe:
JMAG operations are run by one person and Mr. Goto is responsible for examining data on physical properties and checking the results for use in JMAG.
Mr. Goto:
I believe that the temperature-dependent physical property of the material is extremely important in simulation, but measuring, is quite difficult, so we are currently accumulating know-how on this. We are having difficulties because there are few documents and data disclosed on the subject, we don’t get answers by asking questions and we can’t find anything about it. There is the option of asking a research facility to do the measurements, but it’s quite expensive. As we mentioned at the JMAG Users Conference 2020, we revise the physical properties so the simulation results match the actual measurement.
Mr. Kawabe:
We hold a JMAG meeting once a week. We look at the results and discuss and revise whether to make certain areas smaller or not. It is a meeting within the department, but a member of the induction hardening production site also attends. Better reviews are made this way because the production site staff knows the customers’requirements.
THE PIONEER IN ADVANCED TECHNOLOGY DEVELOPMENTS OF TOPOLOGY OPTIMIZATION AND 3D PRINTERS
Mr. Kawabe:
We presented our study on “Searching for Optimum Shapes of Heating Coils with Topology Optimization” at the Additive Manufacturing Expo held in Osaka, 2021. With machining, optimization can result in shapes that are difficult to fabricate but the 3D printer can create actual shapes. Using the optimization results as a base, we try making straight lines or round-off curves so the shape can actually be fabricated.
Mr. Goya:
I believe it is a major achievement to have verified that topology optimization can also be applied to induction heating coils. The blueprint provided by the customer has induction hardening specifications. It will take at least 10 years to envision a heating coil shape according to that hardening pattern. Then it is thought that it will take another 10 years to be able to conduct brazing on the heating coil.
Heating coil design can be done on a computer using topology optimization. A heating coil can be created without brazing skills using a 3D printer. Machines will allow anyone to do something that took 10 years for humans to accomplish on their own. It is still difficult for anyone to create heating coils on a daily basis because the massive amount of calculation and insufficient understanding of the process can affect the results. However, the possibility of creating coils using the combination of topology optimization and a 3D printer has been verified. I believe that the concept of coil manufacturing in induction hardening will drastically change in the near future.
Mr. Goya:
Yes. I tried topology optimization and was surprised with what it can actually do. The hardening conditions were also quite close. Frequency was only 2kHz different from actual hardening, output was almost the same, and heating time was only off by 0.7 seconds.
Mr. Goto:
Optimization of physical properties is run with multiple variables, but I think it would be nice if we can also practice taking measurements properly and confirm that both results match, from now on.
Mr. Kawabe:
We are also working on identifying cooling conditions from measurement results by using optimization calculation.
Mr. Goya:
We’ve been working on raising the accuracy of cooling during heating because in actual hardening, there are instances where cooling is conducted from the opposite side during heating to cool the outer peripheral surface during hardening of the inner diameter section. Fluid analysis is required to run a cooling simulation, but we are not able to run a fluid analysis with our current skills. Therefore, we have been trying to see hypothetically what value of boundary condition (heat transfer coefficient) will match the actual results by taking actual measurements and running optimization calculations for almost a year when analyzing with JMAG.
Fig.1: Heating coil created using hints from the result of topology optimization calculation
Fig.2: Comparing the results of topology optimization calculation and actual measurement
(comparing calculated temperature distribution in work and actual hardened pattern of work)
EFFECTIVE USE OF TECHNOLOGY AND SIMULATION FOR GLOBAL EXPANSION
Mr. Kawabe:
it’s more like we have more objectives now rather than differences. We’ve been using JMAG as a tool to take on new business challenges. What we need for that would be to hire more analysis experts.
Mr. Shimomura, CEO:
We need at least 2 or 3 more people. We also need to create a team for Mr. Kawabe. I want him to enhance his technical skills. There are no problems now, but it will become more difficult to try to create unprecedented types of coils without experience and I think it is necessary to work as a team.
Furthermore, simulation is most effective for creating something without the know-how. Simulation can identify the cause of problems with coils that could not be made by other companies. It’s interesting that this also leads to business opportunities.
I’m thinking of expanding facilities more when we are able to compete on a global scale.
Interviewee
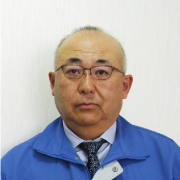
CEO
Takao Kogyo Co., Ltd.
TKE Co., Ltd.
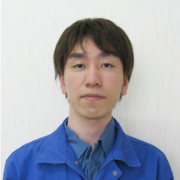
IHT Development Department
TKE Co., Ltd.
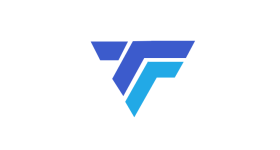
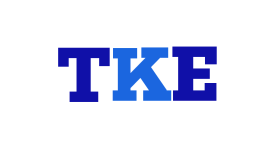
Aichi Office (Sakes Contact): 3-22 Gotoyama Yatomi-city, Aichi, Japan
– Purchase & sales of cutting tools and special tools
– Manufacturing & sales of machined parts and jigs
– Manufacturing & sales of streamlining/automated devices and conveying devices
Protected content here, for members only.
You need to sign in as a Regular JMAG Software User (paid user) or JMAG WEB MEMBER (free membership).
By registering as a JMAG WEB MEMBER, you can browse technical materials and other member-only contents for free.
If you are not registered, click the “Create an Account” button.