はじめに
電動化におけるキーコンポーネントであるモータに要求されるのはコンポーネントとしての高い性能だけでなくシステムとの高い整合性です。
シミュレーションを活用したモデルベース開発はモータ開発においても必須になりつつあります。
モータ設計で高い実績を持つJMAGがモデルベース開発のための新しいワークフローを提案します。
事例では、EV用のモータの開発が、システム設計、コンポーネント設計、試作・性能評価、システム検証の中で具体的にどのように進んでいくかを示しています。
尚、示されている事例は全て一貫してJMAGを使ったシミュレーションによるものです。
モータ開発ワークフローについて
EV用を想定したモータ開発ワークフローをシステム設計、コンポーネント設計、試作・性能評価、システム検証の4つのフェーズに分けて表現しています。
4つのフェーズで一つのV字の開発ワークフローを表します。ただしここで示されるのは既存のワークフローではなくシミュレーションをベースとしたモデルベース開発のワークフローです。
1. システム設計
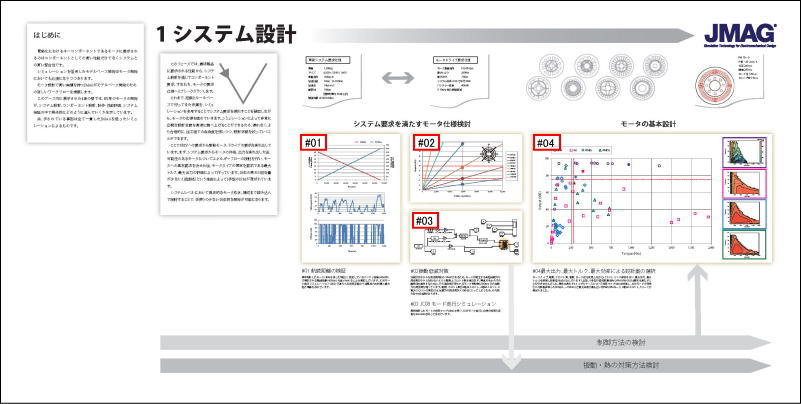
これまで、経験とルールベースで行ってきた作業を、シミュレーションを多用することで、システム要求を満たすことを確認しながら、モータの仕様を固めていきます。シミュレーションによって非常に広範な設計空間を高速に調べ上げることができるため、漏れなく、より合理的に、後工程での自由度を残しつつ、設計空間を絞っていくことができます。
ここではEVへの要求から駆動モータ、ドライブの要求を割り出しています。まず、システム要求からモータの体格、出力を割り出した後、可能性のあるモータについてエネルギーフローの検討を行い、モータへの基本要求を決めた後、モータタイプの選定を要求である最大トルク、最大出力の評価によって行っています。効率の高さと磁石量が少ない(低価格)という理由によってI字型のIPMが選ばれています。
システムレベルにおいて具体的なモータ形状、構成まで踏み込んで検討することで、手戻りの少ない効率的な開発が可能になります。
#01 モータドライブ要求仕様の決定証
システム設計は車両システム要求から始まります。車両システム要求が与えられモータドライブ、バッテリ、制御、冷却、駆動系のサブシステムの要求が決まります。今回、重量1,300kg、サイズ4,300×1,800×1,600、最高速度 160km/h、加速性能0-100km/hまで10秒、加速度10km/h/s、静音性については100km/h巡航時車内55dB以下という要求から始まりました。車両の重量、最高速度が決まるとモータの最高速度、最大出力、最大トルクが見積もれます。今回は車両システム要求から最高回転数10,000rpm以上、最大トルク260Nm以上、最大出力75kW以上、システム効率をWLTCモードで平均90%以上としました。
ただし、ここではモータドライブ仕様が車両システム要求を満たすかどうかはわかりません。そのためモータの基本設計を行い、要求の一つである航続距離を走りきれるかどうかの検証を行います。その際にはバッテリや駆動系についても基本設計の情報が必要です。
#02~#04についてはPDF版をご覧ください
PDFを見る
2. コンポーネント設計
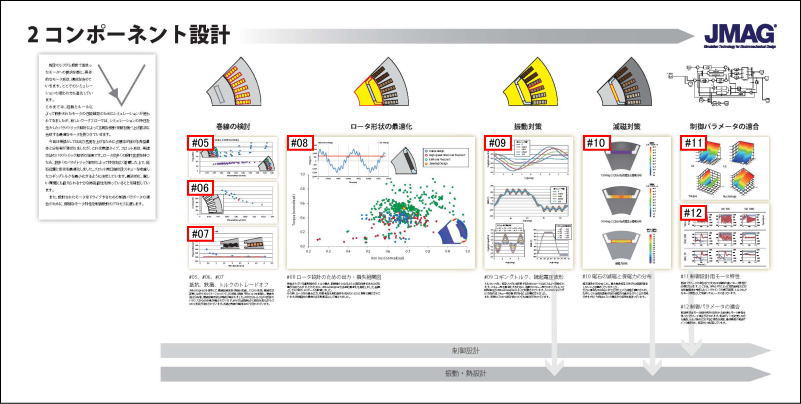
これまでは、経験とルールによって設計されたモータの性能確認のためにシミュレーションが使われてきましたが、新しいワークフローでは、シミュレーションの特性を生かしたパラメトリック解析によって広範な設計空間を調べ上げ要求に合致する最適なモータを見つけていきます。
今回は巻線としては出力密度を上げるために占積率が稼げる角型導体と分布巻が選ばれましたが、これは素線タイプ、スロット形状、巻線方法のパラメトリック解析の結果です。ロータは多くの設計変数を持つため、数多くのパラメトリック解析によって特性を広く俯瞰した上で、磁石位置と形状を最適化しました。スロット開口幅は段スキューを考慮したコギングトルクを最小化するように決定しています。最終的に、厳しい環境にも耐えられる十分な減磁耐性を持っていることを確認しています。
また、設計されたモータをドライブするための制御パラメータの適合のために、詳細なモータ特性を制御設計のプロセスに渡します。
#05 抵抗
図5-1 巻線方法とトルク・抵抗のトレードオフ
#06~#12についてはPDF版をご覧ください
PDFを見る
3. 試作・性能評価
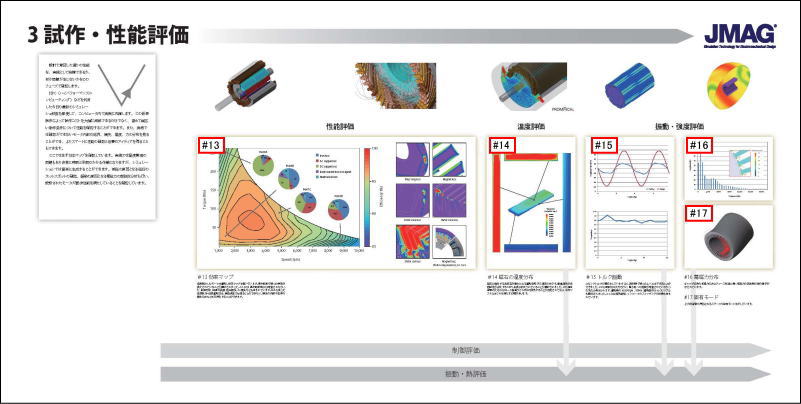
HPC(ハイパフォーマンスコンピューティング)などを利用した今日の最新のシミュレーション技術を駆使して、コンピュータ内で実機に肉薄します。この仮想試作によって試作コストを大幅に削減できるだけでなく、極めて幅広い動作条件について性能を確認することができます。また、実物では確認ができないモータ内部の磁界、損失、温度、力の分布を見ることができ、よりスマートに性能の確認と改善のアイディアを得ることもできます。
ここではまず効率マップを確認しています。実機では温度管理の問題もあり非常に時間と手間のかかる作業になりますが、シミュレーションでは簡単に生成することができます。減磁の原因となる磁石のホットスポットの確認、振動の原因となる電磁力の詳細な分析も行い、設計されたモータが要求性能を満たしていることを確認しています。
#13 効率マップ
図13-1に効率マップを示します。これは各動作点で制御、回路を考慮した実駆動時の電流波形を入力したFEAを繰り返し計算し損失を求め作成しています。この時、磁石、コイルには渦電流の計算をし、鉄損は後処理で求めています。基本設計時に効率マップを評価する際は正弦波電流を仮定し渦電流の効果は考慮されません。基本設計時とここでの効率マップの差を図13-2に示します。高速域では効率に5%ほど差が生じていることがわかります。また図13-1には4つの代表的な動作点で損失の内訳を示しています。Point Aは高負荷で大電流が流れるため銅損が支配的です。Point Bは低速・低負荷でPWMのキャリア周波数成分が多く含まれるため鉄損が大きな割合を占めています。Point C、Point Dは回転速度が上がりAC損失が大きくなることがわかります。図13-2(a)-(f)は各部の損失密度分布を表しています。ここではプレスリングなどの詳細部品に生じる漂遊損失も評価します。プレスリングやロータ、ステータ表面、コイルエンド部はおもにはコア表面から漏れる磁束によって渦電流が生じます。このモータでは磁束がギャップを渡る際に軸方向の磁束が生じ、それが各部損失を生じています。図13-2(f)に磁束の周波数成分と損失密度の関係を表しています。ステータコアと磁石の部分にはキャリア周波数成分の磁束線と損失密度分布を示しています。仮想運転では損失の発生要因を可視化・分析することが可能です。
図13-1 試作・検証時効率マップ
図13-2 各部損失密度分布
#14~#17についてはPDF版をご覧ください
PDFを見る
4. システム検証
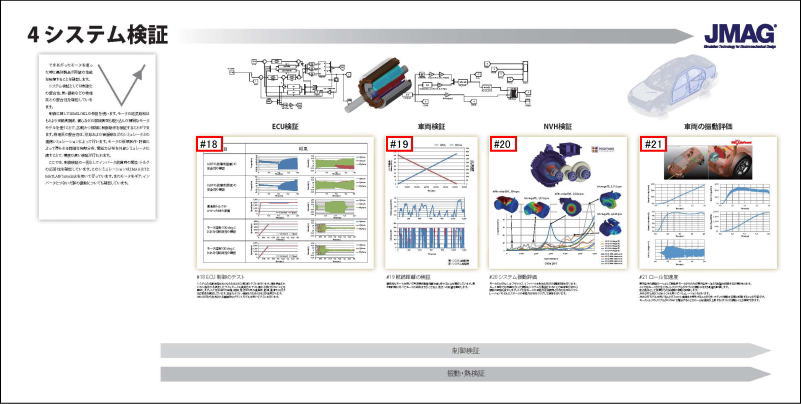
システム検証としては制御との整合性、熱・振動などの物理系との整合性を確認していきます。
制御に関してはMIL/HILの技術を使います。モータの磁気飽和はもとより空間高調波、偏心などの詳細情報も取り込んだ精緻なモータモデルを使うことで、広範かつ詳細に制御動作を検証することができます。物理系の整合性は、冷却および音振動などのシミュレータとの連携シミュレーションによって行います。モータの仮想試作・評価によって得られる詳細な発熱分布、電磁力分布を外部シミュレータに渡すことで、精度の高い検証が行われます。
ここでは、制御検証の一例としてインバータ故障時の電流・トルクの応答性を確認しています。このシミュレーションはJMAG-RTとMATLAB/Simulinkを用いて行っています。またモータをギア、インバータとつないだ際の振動についても確認しています。
#18 ECU制御のテスト
図18に代表的なテスト項目とテスト結果を示します。ここではJMAG-RTとSimulinkを使っています。IGBTの固着や断線による故障状態を模擬し電流が流れすぎないことを確認します。実機による故障時のテストは危険を伴いコストがかかります。モデルベースで行うことで安全に効率よくテストが可能です。次に運転中に170Nmの高い負荷をかけた際のモータの挙動を確認します。1秒間170Nmの負荷をかけてもインバータ最大電流(250A)に抵触することなく、速度も指令値にすばやく戻ることが確認できました。温度を変えた際も指令値に遅れなく追従できており問題ないことが確認できました。
ここではJMAG-RTから生成されるプラントモデルを用いてシミュレーションを行います。JMAG-RTモデルは磁気飽和、空間高調波を詳細に再現するため定常状態ではない動作環境であっても実機同等のモータ挙動を再現します。またJMAG-RTモデルは様々なHILSでそのまま利用可能です。
図18 ECU制御の代表的なテスト項目とテスト結果
#19~#21についてはPDF版をご覧ください
PDFを見る
関連資料
- [L-OP-03] JMAGで行う多目的最適化
- [L-MU-07] 専用ツールとの連携によるマルチフィジックス解析
- [W-MO-23] 永久磁石モータの振動/騒音の実測と解析モデルの構築
- [L-OP-25] クラウド環境でのJMAGの活用
- [L-OP-26] 多ケース計算のライセンスコスト削減
- [L-HU-43] デスクトップ並列ソルバ SMP メニーコア対応
- [L-MB-55] JMAG-RTを用いた制御回路シミュレーションのための高精度プラントモデルの生成
- [W-MA-70] コイル交流損失計算のためのメッシュモデリング
- [L-MO-77] JMAG-ExpressとJMAG-RT Viewerでモータ概念設計
- [L-OP-78] ユーザ定義の形状モデルライブラリ
- [L-MB-79] 制御系を考慮した回路連成機能
- [L-SE-81] メッシュ検討をより高速に
- [L-MB-82] FEAモデルを短時間でプラントモデルへ
- [W-MO-85] 高調波損失を考慮した効率マップ評価
- [W-MA-88] 異常渦電流損失の高精度化
- [L-MO-89] モータ設計ツールJMAG-Express
- [L-MO-90] モータ用コイルの詳細なモデリング
- [L-MU-91] JMAG/RomaxDESIGNER連携によるEVドライブラインのNVH解析
- [L-MU-92] JMAG/Particleworks連携によるモータの冷却解析
- [L-MU-93] JMAG/Adams/Simulink連携による車両走行シミュレーション
- [W-OP-96] 駆動用モータの多目的最適化のためのGAの重要性
- [W-SE-101] 並列計算によるモータ渦電流の詳細解析
- [W-MB-102] モデルベース開発とシミュレーションによるモータ効率マップ
- [L-MO-105] モデルベース効率マップ開発のシステム設計(速度優先モード)
- [L-OP-107] 極数、スロット数をパラメトリックに変更可能な巻線エディタ
- [W-MO-114] 効率マップ実測比較
- [W-OP-119] 設計空間の絞り込みを用いた多目的・多制約最適化問題の大域的設計探査
『JMAGソフトウェア正規ユーザー(有償会員)』または『JMAG WEB MEMBER(無料会員)』でサインインが必要です。
『JMAG WEB MEMBER(無料会員)』へ登録することで、技術資料やそのほかの会員限定コンテンツを無料で閲覧できます。
登録されていない方は「新規会員登録」ボタンをクリックしてください。