解析屋が見た損失評価
山田 隆
漂遊負荷損とは、全損失から鉄損など素性の確かな損失を差し引いた残りの損失ですので、言い換えれば、素性の怪しい損失、とも言えます。そうは言っても損失を生じる電磁界の現象はそれほどなく渦電流による損失が殆どを占めるようです。問題は発生する場所が”漂遊”していることです。導体が変動する磁界に触れれば渦電流が発生しますので、機器内のあらゆる箇所に漂遊負荷損は発生する可能性があります。典型的な例としては、モータのプレスリング、ケース、コア端部など、広い意味では希土類磁石の渦電流損失やコイルの循環電流も漂遊負荷損になります。
漂遊負荷損の素性は渦電流損失ですから、渦電流解析を行えばそれを予測することはできます。鉄損のような複雑な材料モデリングや材料測定はいりません。単純です。単純ですが大変です。三次元の渦電流解析をやらくてはならない上、渦電流の発生する場所も範囲も明確ではありません。そもそも、それを見つけるのが解析の目的ですから。さらに、多くの場合、渦電流は導体表面に集中するので、それを考慮したメッシュを作らなくてはいけません。結局、解析モデルを準備するのが大変なうえ大規模な問題を解くことになります。大変です。
大変だからと言って避けていては立派な技術者になれません。頑張りましょう。実際、この漂遊負荷損の解析はモータ解析の定番アイテムになりつつあり、多くの事例があります<14>-<21>。漂遊負荷損の解析は発電機などの大型機の分野では大変進んでいます。大型機は長い歴史を経て100%に迫る高効率を実現しており、その中で、わずかな損失も逃すまいと徹底的な解析と対策が施されています。それらの事例は今後取り組む人には参考になると思います<21>-<32>。
<晴海1号の漂遊負荷損解析>
私たちが行った計算結果もご覧ください。晴海1号の端部と磁石の渦電流損失を計算してみました。解析モデルと解析仕様をそれぞれ図48と表6に示します。端部の影響を見るためにコイルエンドもモデル化しています。入力は100Hzの正弦波電流です。
図49はメッシュ分割の様子です。端部への磁束は主にギャップから漏れますのでその付近に十分な要素分割を与えています。また、端部の損失は電磁鋼板面内を流れる渦電流によって発生しますので、積層構造をモデル化する必要がありますが、電磁鋼鈑と絶縁被膜をそのままモデル化すると大変なことになりますので、電気抵抗率と磁化特性に異方性を与えることで積層を表現します。
尚、このモデルのメッシュ生成には、もちろんJMAGの自動メッシュ機能を使っています。コア部分は軸方向に一様であるため、この部分は同じパターンのメッシュが積み上げられています。その直上のコイルエンド部は一様性がないため通常のテトラ要素で分割されています。このようにJMAGが形状を認識して適切なメッシュを自動的に生成します。これによって、必要な精度を確保しつつ要素数を抑えることを可能にしています。
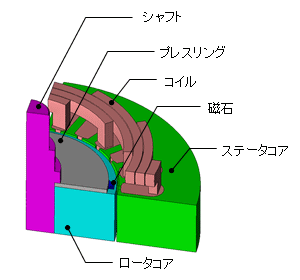
ソルバー解法 | A-Φ法 |
電流振幅 (A) | 4 |
周波数 (Hz) | 100 |
電流位相 (deg) | 30 |
回転数 (r/min) | 3000 |
渦電流計算対象 | 磁石 プレスリング ステータコア [*1] |
要素数 | 101万 |
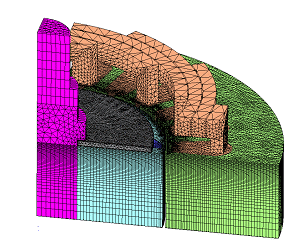
磁石、プレスリングには表皮メッシュを生成。ステータコア表面のメッシュ分解能をあげた。
結果を見てみましょう。図50にプレスリング、磁石、ステータ端部の渦電流損失の時間変化、図51に各部の損失の分布を示します。
ギャップ付近から漏れた磁束がステータ端部に侵入し損失を発生させている様子がわかります。一方、このケースではプレスリングには大きな損失は発生していないようです。磁石には予想通り大きな損失が発生しています。磁石表面の損失分布をみると、スロット高調波に起因していることがわかります。
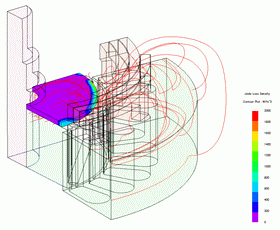
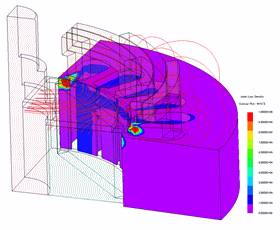
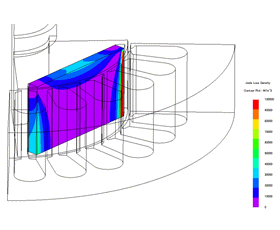
(a) ギャップ部に発生したスロット高調波を含む磁束がプレスリングに鎖交することでジュール損失を発生させている。
(b) コイルエンドで発生した軸方向磁束がステータコアを鎖交することで特に端部でジュール損失が発生している。
(c) ステータ、ロータ間を行き来する磁束が磁石端部を鎖交することでジュール損失が発生している。

プレスリングに生じる損失(右軸)は磁石、ステータコアの渦電流損(左軸)に比べると小さい。プレスリングと磁石はスロット高調波の影響で、ステータコアの損失に比べて高い周波数で変化していることが分かる。
<並列計算>
今回のように100万要素のモデルで180ステップの解析計算となると、かなりの計算時間がかかります。このような解析には並列計算が効果的です。この計算では32並列の並列計算を行いました。今回使用した計算機環境を表7にまとめます。
CPU (1ノード) | Intel®Xeon® E5-2670 × 2 CPU(8 core × 2) |
メモリ (1ノード) | 32GB (4GB × 8) |
ネットワーク | Infiniband (QDR) |
並列数 | 32 (1ノード8並列 × 4) |
総計算時間は2日2時間20分でした。決して短い時間ではありませんが週末を使えば結果を得ることができます。もし、並列計算を行わなければ1か月以上かかってしまいます。つまり、今まで現実的には不可能であった計算が並列計算によって現実のものとなったわけです。今後、漂遊負荷損の計算は増々重要になってくると思いますが、その際、並列計算は必須の解析技術になってくることは間違いありません (図52)。
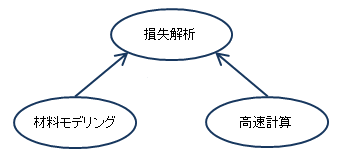
損失解析技術は材料モデリングだけでなく高速・並列計算にも支えられている。
JMAGもそのニーズに応えるために並列計算技術の開発を鋭意進めています。2015年中に現在の速度を3~4倍まで引き上げることを目指しています。例えば上の例で言えば2日程度かかっていた計算が1晩でできるようになります。この高速化によって同じ計算時間でモデルの詳細度を1段階上げることができるようになるはずです。今回のような解析に加えて、コイル内の表皮効果・近接効果を取り込んだ電流分布解析や、電磁鋼鈑間の絶縁破れなどを考慮した解析は既に始まっており<33>、将来的には重要な評価技術になると思います。現在の問題の処理の高速化とともに、詳細度の高い問題への対応に向けて並列計算技術の開発を行っています。
<モデル化について>
確かに漂遊負荷損解析のモデルは大規模になりがちで、高速計算が必要なことは間違いないのですが、モデル化の工夫は常に大事です。その意味で、正直なところ、上でお見せした晴海1号のモデルはあまり良い例ではありません。何を言い始めるのだ、気は確かか?と言われそうですが、大丈夫です、気は確かです。あのモデル化は良くありません。私は隣のJMAGエンジニアに”コラムに載せるから漂遊負荷損の事例作ってよ”と頼みました。数日後、彼が持ってきたのが上の事例です。私は気が小さくて面と向かって言う勇気がないので、紙面を借りて伝えたいと思います。
確かに僕は、大規模問題がテーマになるって言ったけど、こういう大規模化はどうかな。毎日の通勤にトロリーバックを薦められているような感じがする。確かに梅雨のこの時期、傘くらいはあってもいいけど、スーツ、下着、靴まで、毎日、日帰りの通勤で持っていく必要はないと思います。
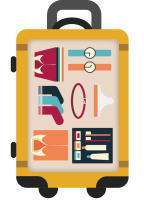
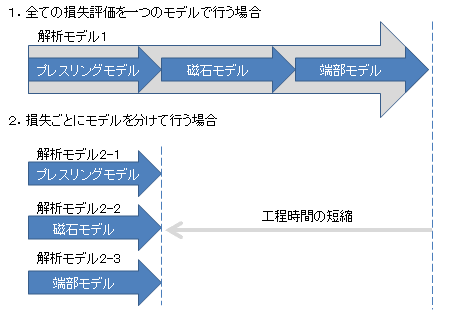
実際、漂遊負荷損の解析が進んでいる大型機の分野では、目的に応じたモデル化によって効率的な解析が行われています。何しろ、解析対象は数メートルを超える巨大構造物である一方で、鉄などの表皮厚さは無情にも材料特性と周波数にしか依りませんから、効率的なモデル化が必須です。
S君には挽回のチャンスを与えたいと思います。
次回は、「加工・組み立ての影響、そして異常渦電流損失について」です。お楽しみに。
[*1] ステータコアは異方性電気抵抗率を設定し、鋼板面内渦電流を計算