1974年の創業以来、自動車部品、産業用機械部品、EV(電気自動車)部品、精密機械部品等の製造を行う金属加工メーカーです。近年は、金属3Dプリンターによる受託造形と高周波熱処理技術の開発で新しい「ものづくり」に取り組んでいます。
高雄工業株式会社は、これまで高度な金属加工技術と世界基準の品質で自動車部品及び精密機械部品等の製造分野で発展してこられました。2021年8月には高雄工業グループの新しい技術開発の発信を担う関連会社としてティーケーエンジニアリング株式会社が設立されました。今回のインタビューでは、金属3Dプリンター受託造形と高周波熱処理技術を活用した新しい生産改革の取り組みについて、代表取締役 下村 豊氏、取締役 合屋 純一氏、高周波事業本部 部長 後藤 文和氏、河辺 正臣氏にお話を伺いました。
創業50周年に向けて
下村社長:
今年で会社創業から48年が経ちました。数年前から50周年に向けて新しい改革と言いますか、新しい事業の立ち上げを考えていましたが、この2年間はコロナ禍で止まってしまっていました。そんな中、人材を活かすためにも、以前からやりたかった3Dプリンターでの造形品の販売を高周波事業部で始めることにしました。また、弊社は自動車部品の機械加工・高周波焼入れの受託を受けていますので、その取引先に対して、装置メーカーとして工具、機器類および部品の販売供給を実施したいという思いもあり、新しくティーケーエンジニアリング株式会社を2021年8月に設立致しました。コロナ禍ですので非常にやりにくい部分はありますが、展示会への参加などを通してPRを強化し、一定の成果は出たのではないかと思っています。今ようやく50周年に向けて本格的なスタートがきれた、というところでしょうか。
今の一番の思いは、今までと同じことを続けることではなく、さらなる新しいものづくりに挑戦する、ものづくりを新しい形に変えていかなければならない、ということです。
3Dプリンターでものづくりに新しい風を呼び込む
3Dプリンター自体はみなさんご存じだと思いますが、実は日本ではまだまだ進んでいない分野です。ちょうど4年前のインドの展示会でヨーロッパメーカーの製品を見た時、ものすごくショックを受けました。ヨーロッパメーカーとの差が歴然だったからです。さらに、ヨーロッパメーカーのアジア営業所はほとんどが中国と韓国にあって、日本にはなかったからです。これはもう、このままいったら日本のものづくりは負けてしまうなと思いました。
誘導加熱についての問題は、創業当初から行っているろう付けによる加熱コイルの製作です。ものすごく大変で、なおかつ高度な技術が必要なため、ベテランの方がいないと絶対できない仕事でした。そこをどうやって改善するか、と頭の中でめぐらせていく中で、3Dプリンターによる造形体の製作を思いつき、その開発に至りました。
とにかく改革する、変革するための武器として、3Dプリンターを利用しました。社員の意識もだいぶ変わったと思います。お客様に対しても、新しいことを始めたというPRになりましたし、大きな一歩を踏み出せたと思います。
下村社長:
すぐには結びついていません。最初はろう付けから機械加工にしようと思っていました。ところがコストバランスが非常によくありませんでした。それで結局またろう付けに戻りました。元々弊社は誘導加熱コイルの設計をしていましたから、形状を作ることはできます。ろう付けも、もちろんできます。ただ、確率としたら当時7割くらいが成功で、失敗もしました。そのリスクを考えると、このままではダメだという思いがどんどん強くなりました。
そんな時、3Dプリンターにたどり着きました。しかし、当時日本では金属3Dプリンターを見たことはなく、また樹脂しか扱えませんでした。そこをどうにか金属(銅)を3Dプリンターでできないか、と。国内で色々聞いてみても難しいという回答しかありませんでした。なのに、インドの展示会ではあまりにも普通に置いてあって、思い描いていた加熱コイル造形を実際に目にした時の衝撃は今でも忘れられません。
ヨーロッパの金属3Dプリンターの用途は航空機部品がメインです。誘導加熱はほとんどしていないと思います。3Dプリンターメーカーの納品先は7割方航空機部品メーカーのようで、サンプルとして形を作ることはあっても、量産型の加熱コイルを作ったという話はあまり聞かないので、高周波焼入れ用加熱コイルはほぼ弊社のオリジナルです。
3DプリンターとJMAG導入で設計工程の時間と精度が大きく変化
下村社長:
ろう付けコイルの場合は、設計の試行錯誤も含めて2か月くらいかかっていたのに対して、JMAGと3Dプリンターの導入によって2週間くらいの製作期間で可能になりました。
設計の部分に関して言うと、JMAGの導入によって設計段階でのトライアンドエラーはゼロになりました。それは本当に大きな効果です。早くできても良いものができないと意味がないので、それが精度よく早いサイクルでできるようになったというイメージです。
合屋氏:
コイルの開発は、①設計、②コイル製作、③熱処理試験、の順で開発を行い、図面通りのパターンができたら製造部門へ引き渡しますが、JMAGがない時代は、熱処理試験の時に熱処理仕様を満足できないコイルが多々発生しておりました。そうなるとまた設計からやり直し、ということを繰り返し行っていたため、2回転すると2か月、3回転すると3か月かかるという状況でした。今は設計時間も含めて1週間くらいでフィードバックされるので、がんばれば2日くらいで2回目の直しまで終えることも可能となり、設計から製造までのサイクルが非常に早くなりました。今のところJMAGの正解率は87%くらいです。これからもっと改善すると思っています。
下村社長:
そうです。結果がすぐにわかるのが良いです。また、5年10年前より商品自体の形状が難しくなってきていると感じています。データが手に入らず分からない部分があり、それをどうやってJMAGで表現していくかというところが難しく、さきほど87%の正解率と言いましたが、私からするとよくそこまで正解率が向上したなと思っています。
下村社長:
高周波事業部に関しては、高周波の設備やノウハウ、そしてソフトウェアを使える人を育てなければいけません。その前に現場をある程度勉強してもらった方がいいかなというのもありますね。それと、材料に関して詳しい人間も育てていかないといけないと思っています。製品につきましても今の材料で本当に良いのかという気持ちがあって、色々テストはしていますけど毎日の仕事が増えてきていて手が回っていないというのが現状です。
下村社長:
はい。まったくゼロからのスタートなので、人材もゼロから育てるというよりある程度経験がある人材を集めて取り組むというイメージです。最終的に何を作って、何をするか、というレベルのことを知っていないとできませんから。
それと、必要な人材は1人2人じゃなく、やはりチームで作っていかないといけないので、そのチームがうまくコントロールできるかどうかというのも重要です。
ものづくりのプロセスの変革でよりよいものを作る
河辺氏:
品質向上を目的に2019年4月16日に品質改善プロジェクトが発足しました。そのプロジェクトのためにたくさん加熱コイルを作ったのですが、先ほど言いましたように製作に1か月くらいかかる上に、かなり難しいプロジェクトだったので狙ったような成果が出ないことが多く、時間やコストの無駄を痛感しました。そこでプロジェクトメンバーの1人から熱処理のシミュレーションはないのかという話しが出て、WEBで調べた結果、JMAGというソフトウェアを知ったというのがきっかけです。
それから、2019年11月に体験セミナーに参加し、年明けからトライアルを利用、3月には社長や役員の前でプレゼン後、導入が決定されました。JMAG導入の目的は、コイル開発の時間短縮と設計情報の入手でした。それは完全に達成できたかなと思っています。
河辺氏:
そうですね。待っていた答えが出たのはやはり決めてとなったところですね。
下村社長:
正直言って、品質問題など色々な問題があって、ヨーロッパからの受注も品質がクリアできないと受注できないというレベルだったので、みんなが必死になってやってくれていました。
河辺氏:
よい結果も悪い結果も視覚的に見て理解を深めることができるので、今だと悪かった結果の時に、加熱コイルの改善箇所にあたりがつくようになりました。パソコン2台は常時シミュレーションで稼働している状態です。
河辺氏:
JMAGを導入した当初は、社内ではまだ信用されませんでした。ですので、JMAGの計算と加熱コイル製作を併用していました。それが今ではJMAGの結果が出るまで製作を待つという流れになっています。
合屋氏:
私自身導入したのはいいものの、加熱コイルの設計者がどこまでシミュレーションを信じてもらえるか危惧していましたが、結果をみて2~3か月で現場の意識が変わりましたね。シミュレーションの結果を信用し始めるのは思ったより早かったです。
下村社長:
JMAGを含め設計に関するソフトウェアは、研究所には入っていても工場の末端で活躍しているというのは少ないと思います。設計とか開発は入れているところがあっても、工場はあまり信用していないから使ったことがない。ゆえに使いこなせない。でも、弊社の場合はそうではない。そこがポイントだと思います。3Dプリンターを持っているのは研究所だけという会社がほとんどかと思いますが、私たちは工場の中に3Dプリンターを入れて使っています。商品あっての設計だからこそ合わせなくてはいけません。だからみんなが信用できるかできないかが大事で、最初はダメだと思った人もいると思う。それくらい作る側が変わった半年、1年だったなと思います。それが本当に嬉しいです。
下村社長:
今ではJMAGでのシミュレーション結果が出てこないと怖くて先に進めません。逆に言うと、解析結果を待っても納期に間に合うというのが大きな変化です。ろう付けの時は、たまたま弊社は試作工場を持っているので自社でテストができましたが、試作が失敗すれば何度も繰り返しになり、本当に時間がかかっていました。
合屋氏:
この半年で100件近くシミュレーションを行いました。正解率は先程言いましたが、昔はシミュレーションでだめとなるような加熱コイルをそのまま作っていたわけですから、それを金額換算すると以前と比べて大きな経費削減になっていますし、無駄な金属(銅)を使わなくてよくなりました。それは環境にも良いことです。
合屋氏:
設計ができたらシミュレーションを行い、結果が良ければ、3D プリンターで作って、組み立てて試験という一連の流れで仕事しているのですが、18名いる部員のうちシミュレーションを担当しているのは2名です。河辺リーダーがJMAGの操作担当でコンピューター2台を駆使して日々解析を行っています。後藤部長は、熱依存物性値を文献で調査したり、実際に実験を行ったりして精度向上を行っています。物性値調査の実験では、実験方法・使用する治具等など後藤部長が発案し、毎週行っているJMAG定例会議の中で関係者全員で検討しています。
河辺氏:
JMAGの操作は今のところ1人で行っていて、後藤部長にはJMAGで用いる物性のデータの調査や結果の確認などをお願いしています。
後藤氏:
シミュレーションでは材料の温度依存物性値というのは非常に重要だと思いますが、測定自体がとても難しいのでそこのノウハウを今蓄積しているところです。公開されている文献やデータが少なく、聞いても教えてもらえませんし、探しても出てこないので苦労しています。どこか研究機関に測定を依頼するという選択肢もありますが、非常にコストが高いですからね。2020年度のJMAGユーザー会講演の発表の中でも伝えましたが、シミュレーション結果が実測値と合うように物性値を見直したりしています。
河辺氏:
週に1回JMAGの打合せを行っています。そこで結果を見ながら話し合って、ここの部分を小さくした方がいいねとか、見直しをしています。部署内の打ち合わせですが、熱処理製作現場からの1人も交えて行っています。製作現場の人は、お客様の要求もよくわかっており、より良く見直すことができます。
トポロジー最適化と3Dプリンターの先進的な技術開発のパイオニア
河辺氏:
2021年大阪で開催された次世代3Dプリンター展で、トポロジー最適化で加熱コイルの最適形状の探索について発表しました。最適化の結果として機械加工では難しいような形状が出てしまうことがありますが、3Dプリンターではそれを実際の形にすることができます。最適化の結果をアイデアの元として、実際にそこから先加工できるように、ここは直線にしてここはRにしてみたりと試しています。
合屋氏:
トポロジー最適化が誘導加熱の加熱コイルにも適用できることを検証できたのが大変大きいと思います。お客様に頂いた図面に焼入れパターンの仕様が書いてあるのですが、その焼入れパターン通りの加熱コイル形状が想定できるようになるまで早くても10年はかかります。それから、加熱コイルのろう付け作業ができるようになるのにも10年かかると言われています。
加熱コイル設計はトポロジー最適化を使ってコンピュータでできる。ろう付けの腕前がなくても、3Dプリンターを使えば加熱コイルを作ることができる。人間が10年以上かけて今までしてきたものが、機械で誰でもできるようになるのです。計算環境も影響するので日常的にはまだ難しい部分もありますが、今回のトポロジー最適化と3Dプリンターの組合せで可能であることが検証できましたので、近い将来、高周波熱処理においてコイル製作の考え方が大幅に変わってくる可能性もあるのではないかと思います。
合屋氏:
はい、トポロジー最適化をしてみて、実際そのすごさに驚きました。焼入条件もかなり近い線で結果がでました。周波数は実際の焼入れの時と2kHzしか変わっていないし、出力もほぼ同じで、加熱時間が0.7秒違うだけでした。
後藤氏:
物性値の最適化を多変数で行っていますが、今後は測定もあわせてちゃんとやれるようになるといいかなと思います。
河辺氏:
他には、測定結果から冷却条件を最適化計算で同定することに取り組んでいます。
合屋氏:
実際の焼入れでは、内径部の焼入れ中に外周面を冷却する等、加熱中に反対面から冷却を行う場合があり、加熱中の冷却について精度を上げることに取り組んでいます。冷却をシミュレーションで模擬するためには、流体解析を行う必要がありますが、今の実力では流体解析を行う力はありません。そこで、簡易的にJMAGでの解析時に境界条件(熱伝達率)をどの値にすれば実態と合ってくるのかということを実際の測温や最適化計算等で求めることを1年近く取り組んでいます。
技術×シミュレーションの有効活用で世界を目指す
河辺氏:
変わるというか追加されている状況ですね。新しいビジネスへのチャレンジのツールとしてJMAGを使わせていただいています。課題は解析専任者を増やすことです。
下村社長:
少なくとも2、3人は必要になると思います。河辺リーダーのチームを作る必要があります。そして、河辺君もさらに技術向上を目指してほしいです。今のところは問題なくやっていますが、前例のない加熱コイルを作ろうとした時、経験のない人間が作ろうとしても、もっとハードルが高くなると思いますので、チームで取り組むことが必要です。
また、ノウハウがわからないものを作るには、シミュレーションはとても有益です。他社でうまくいかないコイルもシミュレーションで原因究明ができますので、それもビジネスに結びつくから面白いですよね。
今後は、世界を相手にできるようにいずれはもっと設備を整えていこうと思っています。
本日はありがとうございました。
お話を伺った方
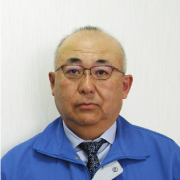
ティーケーエンジニアリング株式会社
代表取締役社長
下村 豊氏
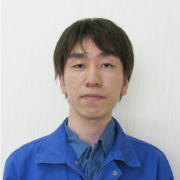
高周波事業部
高周波開発部
熱処理技術課
河辺 正臣氏
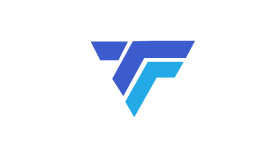
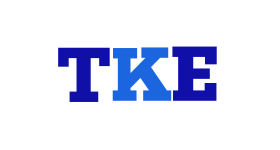
愛知事業所(営業窓口):愛知県弥富市五斗山3丁目22番地
・切削工具 および 特殊工具の仕入れ、販売
・機械加工による部品、治工具の製造、販売
・省人化・自動化装置ならびに搬送装置の製造、販売
『JMAGソフトウェア正規ユーザー(有償会員)』または『JMAG WEB MEMBER(無料会員)』でサインインが必要です。
『JMAG WEB MEMBER(無料会員)』へ登録することで、技術資料やそのほかの会員限定コンテンツを無料で閲覧できます。
登録されていない方は「新規会員登録」ボタンをクリックしてください。
他の導入事例はこちら
トポロジー最適化に興味がある人におすすめ資料
- 株式会社東芝:「JMAGトポロジー最適化による耐減磁性能向上の検討」, JMAGユーザー会講演論文集, 2021
- Volvo Car Corporation:「Topology Optimization of Electric Machines for E-mobility Applications」, JMAGユーザー会講演論文集, 2021
- 株式会社デンソー:「JMAGの密度法によるトポロジー最適化適用事例」, JMAGユーザー会講演論文集, 2020
- 日立オートモティブシステムズ株式会社:「自動車駆動用モータへのトポロジー最適化解析技術の適用」, JMAGユーザー会講演論文集, 2020
- [JFT057] トポロジー最適化の実行方法, 機能チュートリアル
- [JAC257] IPMモータのトポロジー最適化, アプリケーションカタログ
誘導加熱に興味がある人におすすめ資料
- 光洋サーモシステム株式会社:「クラウド活用による誘導加熱解析の高速化」, JMAGユーザー会講演論文集, 2021
- 日本精工株式会社:「AMD製CPUによる計算速度向上と中規模モデルにおける並列計算について」, JMAGユーザー会講演論文集, 2021
- 高雄工業株式会社:「最良焼入れパターンを目指したIHコイルの最適形状探索」, JMAGユーザー会講演論文集, 2020
- 高周波熱錬株式会社:「2重硬化層高周波焼入れ”WIQ®”シミュレーション」, JMAGユーザー会講演論文集, 2019
- 株式会社エィ・ダブリュ・エンジニアリング:「JMAGと最適化ツールHEEDSを活用した誘導加熱用コイル形状探査」, JMAGユーザー会講演論文集, 2017
- NTN株式会社:「JMAGとHEEDSの連携による加熱コイル形状の自動設計」, JMAGユーザー会講演論文集, 2017
- 光洋サーモシステム株式会社:「JMAG-Optimus連携による誘導加熱コイルの形状最適化」, JMAGユーザー会講演論文集, 2017