アプリケーション / ソリューション
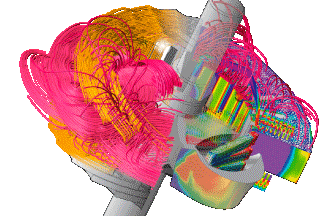
モータ設計
JMAGはモータの解析に絶対の自信をもっています。長年に渡るモータ分野で培われたノウハウが使いやすい形で提供されています。
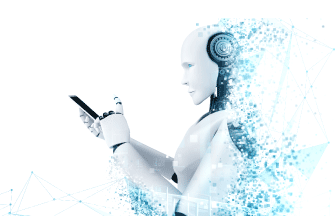
ロボティクス
バッテリー駆動がメインとなるヒューマノイドでは、小型・軽量でありながら、高出力、高精度な制御、高い耐久性を持つモータが求められます。
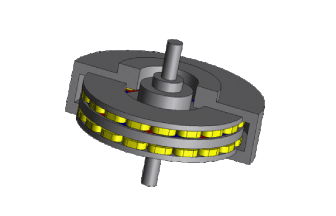
アキシャルギャップ型モータ
アキシャルギャップ型モータは軸方向の磁束を利用して円板状に配置された回転子と固定子が対向して回転する構造です。
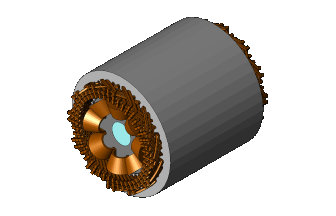
巻線界磁型同期モータ
巻線界磁モータ(WFSM/EESM)は広い駆動範囲で高効率が要求される駆動用モータとして着目されています。
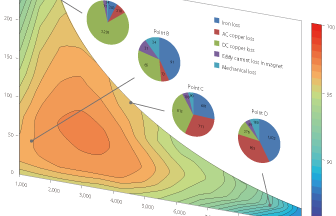
モータのモデルベース開発事例
モータ設計で高い実績を持つJMAGがモデルベース開発のための新しいワークフローを提案します。
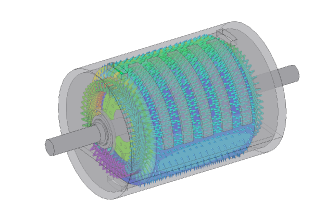
JMAGが提案するモータ設計のための熱解析
磁気設計段階において精度と使いやすさのバランスが取れた熱設計手法が求められています。
JMAGは磁界解析と熱解析のモデルで設計変数を共有化することで磁気特性・熱特性の評価を同時に行います。
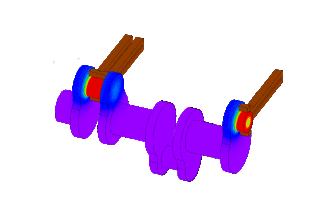
誘導加熱
焼入れ、焼嵌めなどの生産技術から電磁調理器の設計開発まで、様々な用途で利用されています。
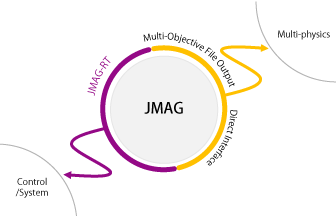
JMAGオープンインタフェースプログラム
連携解析の必要性や、多目的ファイル入出力ツールについてのご紹介を含め、よりご利用しやすいページへとリニューアルしました。ユーザによる導入事例や、お申し込み方法などもこちらよりご覧いただけます。